Virtualized Process Automation System Increases Sleeman Breweries Production Capacity by 50%
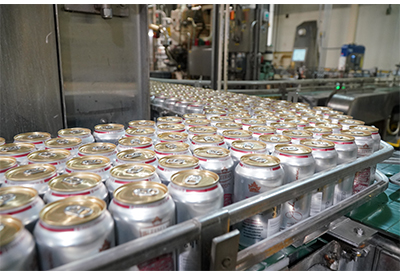
April 16, 2019
Process automation system from Rockwell Automation provides internal process and recipe control
Taking Advantage of the Boom
Ten years ago, tourists looking for a taste of the local life in Southern Canada may have asked for one of the region’s best wines. Today, it’s all about craft beer.
From entrepreneurial newcomers to large-scale producers, brewers in Canada are cashing in on the thirst for craft beer. The number of microbreweries – producing less than 25,000 cases of 24 – has more than doubled in the last seven years.
The explosion in craft beer popularity had one company – Sleeman Breweries – bursting at its production seams. The third-largest brewer in Canada, Sleeman brews and distributes popular beers from lagers to pale ales.
With a notorious past in bootlegging and a brewing history dating back to 1834, the company has re-emerged as a powerful presence in the craft beer market. Sleeman operates three brewing production facilities located in Ontario, Quebec and British Columbia.
Modernizing Craft Brewing
An increase in craft beer demand is ideal for a company like Sleeman, but running out of production capacity is not. At its Okanagan Spring Brewery (OSB) in Vernon, British Columbia, the company was struggling to meet market demand for its OSB beers. The management team was looking for ways to increase output beyond the maximum of eight brews per day.
If unable to increase production capacity at OSB, the company could be faced with the need to build a new facility at a high capital investment cost.
At the time, Sleeman had engaged third parties to produce enough to meet customer demand – not ideal for managing costs, ensuring consistent quality and flavor, and meeting delivery deadlines.
Not only was the facility limited in its ability to increase production, the existing infrastructure was based on an antiquated, semi-automated control system. Changes to the brewing process – including adding new recipes – needed to be made manually, which increased the risk of human error or inconsistencies.
Throughout the production process, operators needed to be at the right place at the right time. If the operator was not on the line to move production forward, brewing would be on hold.
These constraints limited Sleeman’s ability to respond quickly to changes in consumer taste or trends in the industry. The manual approach also hampered access to accurate and timely production metrics needed to fully control the brewing process.
Batch reporting was ad hoc and required operators to input numbers on paper, limiting real-time access to critical information such as pressure and flow rates.
Better Control Means Better Brews
The Sleeman team worked with McRae Integration, a Rockwell Automation Recognized System Integrator, to design and implement an integrated process automation system to increase capacity, reduce risk and provide access to real-time production data.
The Sleeman team was hoping to standardize on one solution across its facilities. A single platform would enable executives to view production metrics and operations data for all facilities from the corporate location.
With one common platform, in-house mechanics and electricians also could more easily transition from one facility to another and keep parts storage streamlined.
“A single platform would give us insights across the line and between facilities, so we could build on successes and meet our goals for continuous improvement while continuing to make great beer,” said Stefan Tobler, brewmaster at OSB. “We had already standardized on Rockwell Automation equipment at our other facilities, and knew McRae could help us meet our goals with a single platform based on the Rockwell Automation technology.”
Brewery automation: Brewery Production and Packaging Automation and Control Systems
McRae implemented a phased approach based on the PlantPAx® distributed control system (DCS) from Rockwell Automation and McRae’s own Meridian BrewSoft and BrewSight software, now FactoryTalk® Brew™.
The system includes reporting and historian software that collects, tracks and records key process data to pinpoint brew cycle trends, allowing operators to proactively make changes to brews as needed. The Rockwell Automation library of process objects provides predefined controller code and faceplates, and the new system helps Sleeman operators more quickly configure new batches and build recipes.
McRae customized the solution for brewing applications with its software solutions, which provide operators with complete control of the process through easily operated web interfaces.
Allen-Bradley® PowerFlex® 525 and PowerFlex 755 drives from Rockwell Automation deliver flexible motor control in the brewing process and help communicate device diagnostics to the control system.
To complete the implementation, McRae worked with Sleeman’s IT team to install VMware® virtualized servers. The Sleeman team had implemented redundant servers at its Vernon facility a few years earlier, but found the costs of the equipment and additional storage space difficult to maintain.
The VMware virtualized servers provided automatic redundancy for production data with enhanced data recovery and expanded data storage. One virtualized server can replace up to four physical backup servers, which greatly decreases the equipment hardware costs.
It also provides the Sleeman team with the ability to create copies of the virtualized servers to run simulations offline and test production changes before they are made.
Ready for More Beer
Within two weeks of the implementation, Sleeman increased production by 50 percent at its Vernon facility going from eight brews to 12 brews per day.
The brewing team can now complete all brews on-site without using third-party producers. And they have avoided the cost of a new facility or significant equipment upgrades or additions.
Additionally, operators have gained more control over the brewing process. With web browser-based recipes, operators can more easily build a new recipe, create a test batch, and store the recipe in the system for additional testing and production.
Brewing managers can simply make process and recipe changes via a web browser interface, without additional personnel.
Management can check on any production issues leveraging the PlantPAx system’s trending capabilities and the BrewSight software’s reporting. With exception reporting, the system creates reports to track progress as the brews reach fermentation and emails management if any brew variables deviate.
The brewing team can take any corrective action needed and reduce downtime, rather than reworking and blending off the brew in small amounts later.
The software upgrades have kept the brew quality high while increasing production speed. The Vernon facility now has an industry-leading, two-hour brew cycle, with improved consistency in flavor and quality.
The Sleeman team is not done – they plan to implement the PlantPAx platform throughout the rest of the Vernon facility, including the tank farm and packaging lines. As the standardization across all areas of Sleeman’s facilities expands, corporate visibility will improve, allowing the company to more effectively make decisions that will grow their business.
The results mentioned above are specific to Sleeman Breweries’ use of Rockwell Automation products and services in conjunction with other products. Specific results may vary for other customers.
Allen-Bradley, FactoryTalk Brew, PlantPAx and PowerFlex are trademarks of Rockwell Automation Inc.; VMware is a trademark of VMware Inc.