Schneider Boosts Oil and Gas Operational Productivity with New Approaches to Power Infrastructure Deployments
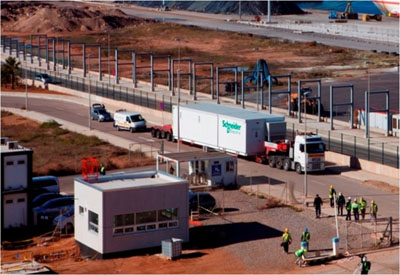
December 19, 2017
Deployment of electrical distribution systems can be challenging for the oil and gas industry. Harsh environments, such as offshore platforms and onshore drilling and extraction sites often make it difficult for electrical distribution and power systems to be installed, commissioned and operated in traditional ways. Implementations are costly and systems uptime becomes a concern because of the complexity involved in making all the part pieces work together in a reliable fashion.
Two recent innovations have now made it possible for oil and gas companies with power distribution challenges to streamline the power system deployment process while contributing to profitability:
- The first is a “fit for purpose” methodology, that helps to avoid the oversizing that has typically burdened many power distribution projects with high costs and low efficiencies.
- The second is a new trend involving the delivery of end-to-end pre-packaged electrical distribution systems that are pre-assembled and pre-tested in the factory and that are ready to plug in on arrival to a designated site (i.e., an off-shore platform, or a drill and extraction site).
In the case of the fit-for-purpose approach, the goal is to implement a step-by-step methodology that redefines traditional modelling of electrical architectures by abandoning “Rules of Thumb” and historical “Cut-Copy-Paste” approaches. During the years when oil prices were high, many in the oil and gas industry fell into an accepted practice of relying on 30 to 40-year-old electrical distribution designs that were reused again and again. The mindset was “It’s ok, we have the money, it’s expensive, but we know the ‘old reliable’ approach has always worked in the past and should work in the future.”
However, today’s low commodity prices are driving cost control pressures that demand a reexamination of inefficient traditional practices. Now, digital tools allow designers to propose co-designed solutions that incorporate both energy supply, process automation and energy management systems. Better integration of process and power, from design to engineering to management, can help reduce deployment costs by up to 35% and shorten delivery times by 6 to 12 months. New power system engineering simulation and calculation tools allow for much higher degrees of optimization than in the past.
The “fit-for-purpose” approach relies on optimization-driven designs that are based on practical analysis of the customer environment and business need. For example, where a traditional, “rough approximation” set-up would habitually specify 20 transformers to address a given need, now 10 may be enough, with assured reliability and redundancy. The new emphasis is on a methodology that eliminates waste and that specifies more compact solutions with less risk. These changes can drive up to 25-30% power distribution architecture CAPEX reductions.
Prefabricated power distribution productivity advantages
In the case of the prefabricated modular power distribution center or “E-house,” the pre-configured transformers, switches, cables, circuit breakers, uninterruptible power supplies, precision cooling, and other electrical and mechanical devices arrive on site, enclosed in a “house,” which offers protection from the outside elements.
Cost optimization and schedule optimization are two significant advantages of the E-house approach. The delivery of a pre-built, pre-tested self-enclosed unit avoids a situation where dozens of contractors need to be dispatched to the site, all scrambling to finish their piece of the project. This results in fewer project scheduling interdependencies and higher safety and efficiency. The responsibility for the proper configuration, testing, delivery, installation, and commissioning all lies with the manufacturer of the E-house. Planning for mechanical, electrical, and systems interoperability is simplified.
Shorter delivery times, fewer people in the field and pre-fabricated design are all elements of this new plug-and-play deployment mentality. This new approach has resulted in productivity gains in the range of 30-50% when compared to traditional deployments.
To learn more about how power infrastructure can be reengineered to drive profitability, download the new Schneider Electric white paper “How Oil & Gas Technology Investments Help Executives Secure Project Payback in a Low Commodity Price Environment.”