PLCnext Technology Open Control Platform
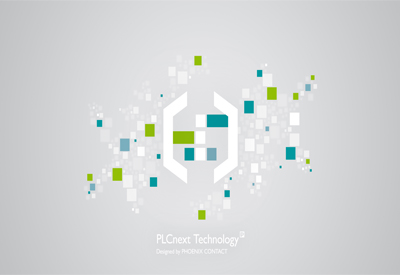
March 13, 2018
By: Frank Walde, Competence Center Automationworx, Phoenix Contact Electronics GmbH
In recent years, automation technology has undergone rapid change. Examples of this include the Internet of Things (IoT), Industrie 4.0 or the constantly growing threat posed by unauthorized access attempts and malware. But what does this mean for manufacturers and users? And what opportunities could arise from such technological developments? The new PLCnext Technology for the up-and-coming controllers from Phoenix Contact provides practical answers.
Like its customers, Phoenix Contact as a traditional manufacturer and a driving force for innovation in automation technology is constantly trying to determine which future trends are really relevant and which solutions the current and future market will expect in this context. It is important to identify the individual aspects of new technological trends and to then determine their impact on the daily work of developers and the needs of users. In order to identify the key characteristics of a modern control architecture, the specialists at Phoenix Contact have examined the requirements of both long-term users and sales partners. One thing that these target groups are concerned about is how they can bring solutions to market faster than their competitors. They also want to be able to offer an ever-increasing number of product versions with minimal effort and to meet the IT security needs of as many different applications as possible. Can the challenges of the forward-looking Industrie 4.0 project be met? In any case, the relevant approaches will contribute to successful business operations.
Hardware-independent platform based on Linux
In order to meet these requirements, PLCnext Technology will be redeveloped from scratch.
For all of these activities, the focus is on users, who are even directly integrated in the development process. Here it became clear at an early stage that openness and consistency were important features. Through the use of Linux as the operating system, PLCnext Technology can use a standard basis on virtually all hardware architectures. Linux is not only absolutely real-time capable, it also offers Phoenix Contact – and therefore its customers – quick participation in the latest developments of the Linux community. However, Linux is only one operating system and therefore does not yet meet the needs of all existing and future challenges.
With PLCnext Technology, Phoenix Contact is now offering a hardware-independent platform which uses Linux and makes it easy to benefit from the advantages of this system. At the same time it offers all the stability and functions that are expected from a modern control concept. Unlike other solutions, with PLCnext Technology the developer no longer has to worry about which PLC will actually later be used. At the end of the project, the developer simply selects a controller with PLCnext Technology in the relevant performance class. This means that the application can be scaled flexibly and complete solutions can be reassembled repeatedly.
Programs can be created in any language
The basis of PLCnext Technology is an intelligent layer between the application program and operating system, which all system components use to exchange data synchronously and in real time, and which also provides easy access to system services such as Ethernet sockets. Due to their open interfaces, the user can use the intermediate layer to integrate and install their own programs (“Apps”) without problems and to communicate with all other system components and the operating system. This is true regardless of whether the programs are created conventionally in IEC 61131-3, in high-level language – such as C# or C/C++ – or via Matlab Simulink. The developer decides on the most suitable software tool for the relevant application or can even combine various tools. While an IEC 61131-3 programmer can use the new PC Worx Engineer software or generate and upload models directly in Matlab Simulink, a high-level language programmer can choose between Visual Studio and Eclipse. This means that every employee is developing in their preferred tool, which eliminates any costs for training in other programming tools.
As mentioned above, PLCnext Technology can be used to create all the specified programs. They can be executed both in cyclic and in event-based tasks. Multi-core systems are also supported. Stringent real-time requirements with minimal jitter can of course also be met. This means that developers can create solution modules and then freely reuse them, which leads to shorter development times and modular system concepts.
Current and future transmission standards are supported
While the developer decides on the programming languages and the necessary tools, the controller must conform to the communication landscape and directives of the end customer or industry. It is therefore important for it to support key transmission standards and to be open for additional protocols. One relevant standard here is OPC UA. Increasing numbers of industrial components exchange data flexibly and securely via the non-proprietary protocol and thus create intelligent and networked systems. PLCnext Technology therefore features an integrated OPC UA server as standard. In this context, the connection of all components to the intermediate layer is a particular advantage. In conjunction with integrated synchronous data loggers and the OPC UA server, a comprehensive data acquisition and signaling solution can be created in a few minutes without any programming.
In addition, PLCnext Technology works with proven PROFICLOUD services and also supports the integration of proprietary cloud solutions. This represents a step toward preventive diagnostics and IoT. Conventional fieldbus systems – such as PROFIBUS, CAN, Modbus/RTU, and INTERBUS – as well as real-time Ethernet standards – e.g., PROFINET and Modbus/TCP – are of course also supported. PLCnext Technology is therefore consistently designed for the later integration of additional protocols so that users can respond flexibly to future developments.
Programming software bundles all functions of the architecture
The success of a project depends not only on the controller and its basic technology, but above all on its optimal integration into development tools. While developing PLCnext Technology, the team at Phoenix Contact in addition to providing the best possible engineering support has therefore concentrated on ensuring that the developer can use their own methods when necessary. As a result, all PLCnext Technology components are modular, and all important parts can be configured. This ensures that the user has full control of the system.
Thanks to the advantage of bundling all functions, in most cases the new PC Worx Engineer software can be used for programming and configuration of the PLC. Its interface also focuses on the user and is therefore consistently designed for user-friendly operation. In addition to IEC 61131-3 programming, all functions – such as web visualization, functional safety, and the modularity of PLCnext Technology – are included in this tool. Due to the central configuration, data can be shared for example with synchronous data loggers, the OPC UA server or the web visualization with just a few clicks of the mouse. Furthermore, PC Worx Engineer has integrated safety functions so that
safety controllers can also be programmed directly.
Access security in accordance with IEC 62443
Now and in future, industry-specific requirements for IT security should be added to the existing functions. Network security and remote maintenance are undoubtedly important in this context, but there is more to IT security than these considerations. Demands on modern systems include integrity, availability, and above all the confidentiality of all data (Figure 3).
This is only possible with a deep integration of different mechanisms and procedures on all levels of PLCnext Technology, as well as the PC Worx Engineer development environment. PLCnext Technology therefore offers security by design, so that security aspects can be implemented according to the leading international standard IEC 62443. IT security is therefore no longer an obstacle, but is the key to new project ideas based on PLCnext Technology.
With PLCnext Technology, Phoenix Contact meets the needs of developers and users in a simple manner. This makes it possible to shorten development times, minimize costs, and enables the people involved to focus on the project and their core tasks.
Download the Digital brochure here
Visit the webpage here