Panduit: Automating Safety Solutions Since 1955
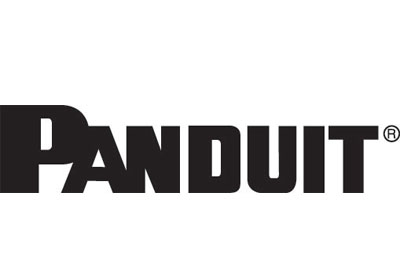
May 19, 2018
Panduit is all about connectivity and has been a driving force behind this for over 60 years. Working within the manufacturing, education, healthcare, transportation, and energy sectors, to name but a few, Panduit is working to ensure each of the sectors has comprehensive, stable infrastructure solutions. The solutions offered by Panduit provide physical, electrical and network infrastructure that are leading their clients into the future. Not only are they providing system solutions but have a strong focus on developing connected safety options designed to protect equipment and workers.
For the month of June our theme is safety, and Panel Builder & Systems Integrator had the opportunity to gain insight the philosophy and safety offerings of Panduit from Marty Kronz, Manager of Business Development at Panduit Corp.
- Can you provide a little general information on Panduit?
Since 1955, Panduit’s culture of curiosity and passion for problem solving have enabled more meaningful connections between companies’ business goals and their marketplace success. Panduit creates leading-edge physical, electrical, and network infrastructure solutions for enterprise-wide environments, from the data center to the telecom room, from the desktop to the plant floor. Headquartered in Tinley Park, IL, USA and operating in 112 global locations, Panduit’s proven reputation for quality and technology leadership, coupled with a robust partner ecosystem, help support, sustain, and empower business growth in a connected world.
Panduit has a significant focus on safety and security, can you outline your safety related programs?
Panduit has a strong and long-standing presence in the industrial safety market with a robust Lockout/Tagout and Hazardous Communication offering. This includes a Panduit developed Lockout/Tagout training video that is available to the broad market and utilized by thousands of companies to train their employees. Panduit has also recently expanded this industrial safety offering to include a Prevention through Design (PtD) solutions for control and power distribution applications.
Managers play a key role in facility safety; how does Panduit assist managers in overcoming safety challenges?
It’s important to have a manager that understands how keeping up with the times is paramount to staying safe in the workplace. Much can be done about creating an electrically-safe workplace, but it is the responsibility of any manager to provide that type of environment to its employees.
Panduit works closely with managers to make sure that they are aware of changes in standards. As safety standards evolve, so too must the company and its workforce. For instance, in Canada, the CSA Z462 Workplace Electrical Safety Standard provides guidance and best practices for establishing an electrically safe workplace and is generally harmonized with the USA standard NFPA 70E. Panduit is actively engaged within these committees by developing and sharing new technology and best practices to further mitigate risks in the workplace.
Additionally, Panduit works with managers to assess how changes in the plant will impact their overall electrical safety. For instance, when new machines are added, the electrical capacity needs grow, and thus an increased need for overall, plant-wide electrical safety grows. Sometimes, there can be an overcrowding in electrical rooms and production areas with added equipment. Other times, challenges are created when multiple suppliers of equipment create anomalies. While codes and standards evolve, and as equipment is added, there can be these compatibility issues. Standardizing processes and procedures can help minimize or prevent human error. Panduit provides solutions for the electrical infrastructure that can help bridge multiple vendors or areas of equipment as additions take place.
With new technology continuing to change how facilities and personnel operate how does Panduit stay ahead of emerging technology and the safety related issues they generate?
New equipment brings new types of hazards and risks. Being able to identify these hazards and having tools, safety procedures and instructions available to mitigate risk is essential to ensuring safety. Perhaps even more game-changing than automation is the availability of connectivity and networking on the plant floor. This allows safety procedures to become more connected and integrated into workflow with the ability to track and log tasks, as well as access to video for training and recording purposes.
Automation is the name of the day and Panduit has recognized this with the introduction of AVT; Can you explain a little more about this technology and how it is changing safe practices?
Absence of Voltage Tester (AVT) is a relatively new innovation. Unlike traditional voltage testers, the AVT is permanent and is installed in the equipment it is testing. Thoroughly different in its application, and more comprehensive than a permanently-mounted voltage indicator, an AVT is used to determine if and when a circuit part is de-energized before opening doors and removing covers from electrical equipment. AVTs automate the functions of handheld voltage testers for this specific task and display information about the status of voltage inside equipment without exposure to electrical hazards. This is game changing for managing safety, as AVTs ensures workers can perform their jobs at the highest, safest level possible, avoiding injury and reducing the risk of arc flash.
Do you have any application/case or just stories from your clients that identify an instance when your products prevented a potentially dangerous situation?
We’re finding that many of our customers who are interested in AVTs are from utilities or are safety, electrical engineering or plant managers within a manufacturing environment. The importance of a robust preventative maintenance and safety program in these industries can’t be understated, especially when it comes to reducing the risk for arc flash and shock hazards. Accuracy and repeatability are critical to any maintenance operation, but that also applies to the preventative maintenance and safety program itself. Facility and safety managers understand that repeatability makes work easier to implement and avoids human error. Even the most conservative estimates say that there are up to five arc flash explosions occurring in electric equipment every day in the United States. Considering these high electrical incident rates, many of our customers are specifying and implementing AVTs into their safety program to significantly lower the risk of an occurrence creating a safer electrical workplace.
Does Panduit work with clients to determine needs and potential future safety products?
Innovating is core to Panduit’s DNA, and we make a conscious effort to take the feedback we hear to help address our customers most pressing concerns. We are problem solvers, developing solutions that result in mitigating electrical hazards in control and power distribution applications. Panduit is always working with our clients to determine needs and anticipate what safety products they may need in the future. This will become especially important as manufacturing environments become “smart.” Not only will electrical safety need to reflect these changes in the plant environment but ensuring regular maintenance of electrical equipment and wiring will be critical.