Is a Smarter Batch in Your Future?
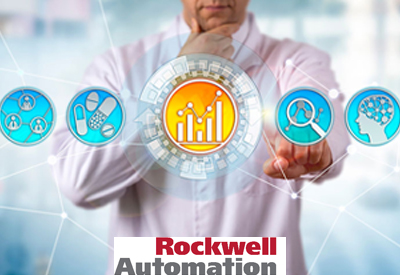
November 26, 2018
By: Dan UpDyke, Market Development Manager – CPG and Life Sciences Industries, Rockwell Automation
The Industrial Internet of Things (IIoT) continues to advance at a rapid rate. And pharmaceutical companies are transforming the industry by using smart, connected devices, analytics, and machine learning to improve drug manufacturing processes and deliver better patient outcomes.
Pharmaceutical companies have also dramatically increased the use of smart technology and automation in their production facilities to improve drug quality and speed innovation. And many have streamlined operations with modern MES and EBR systems.
But as the number of intelligent devices has proliferated, manufacturers have struggled to use the Big Data generated across the plant floor and beyond in truly transformative ways.
It’s About (Hidden) Relationships
In a pharmaceutical plant, a scalable analytics platform can ingest data from diverse data types – and help cut through the clutter by modeling data to find meaningful correlations that lead to new insights.
Pharmaceutical manufacturers regularly rely on analytics for reporting purposes and equipment diagnostics on the plant floor. However, few manufacturers have taken the next step toward more predictive and prescriptive analytics that can impact ongoing continuous and batch processes.
To successfully predict a future outcome and also prescribe actions related to that outcome, an analytics engine must take full advantage of structured and unstructured data from various devices, sensors, tags and business systems.
Historically, the key challenge has been not only accessing and aggregating data from disparate devices, systems and networks, but also delivering advanced analytics based on massive datasets quickly enough to impact production processes in real-time.
Now, thanks to advanced industrial connectivity, data aggregation and automated analytics capabilities, manufacturers can exact more value from more disparate data sources faster than ever before.
Leveraging a secure IIoT infrastructure, the latest capabilities can quickly connect all data that’s important on an asset or a line – and immediately monitor performance as well as make predictions about that performance.
Maximizing Efficiency. Minimizing Process Deviations.
For pharmaceutical companies, predictive and prescriptive analytics hold great promise. For example, batch process deviation management is critical in any pharmaceutical plant to maintain both product quality and regulatory compliance.
Deviations can occur for many reasons – and determining the root cause for a deviation is essential to correcting it. Today, pharmaceutical companies use a variety of methodologies to determine root cause – with limited success.
The latest analytics platforms can bring more clarity to root cause analysis by casting a wide net that extends beyond the process environment to data generated by all relevant IIoT devices and machines.
In addition to pinpointing the cause of deviation based on historical batch records, analytics capabilities such as native anomaly detection can use historical data to improve quality monitoring in real time. Native anomaly detection increases machine monitoring capabilities by automatically learning what normal behavior is – and raising alerts when something is abnormal.
Machine learning is just one way advanced analytics platforms can help pharmaceutical companies maintain product quality – and achieve the ever-elusive “golden batch” cycle after cycle.
See how you can use the latest analytics platforms to capture more value from IIoT devices throughout your production process.