Revolutionizing Just-in-Time Inventory Management With IIoT
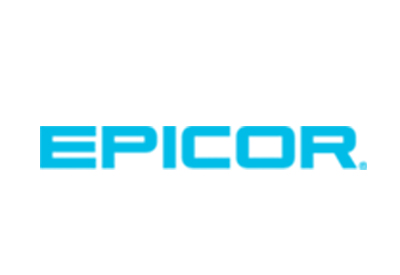
November 29, 2018
Through the use of IIoT to connect wireless pushbuttons in the field to ERP inventory and order management, Jergens Industrial Supply is transforming its business for the digital future of industry.
Jergens Industrial Supply (JIS) is a leading industrial distribution company founded in 1960 that presents itself as Ohio’s largest distributor of industrial products. JIS, which represents more than 300 of the top manufacturers of industrial supply products in the U.S., believes it is not just a company that sells product to customers, but a “partner in productivity.”
JIS generates about 30 percent of the business conducted by its parent company Jergens Inc., a manufacturer of standard tooling components, fasteners, hoist rings, vises and other work holding equipment.
Like many distributors, JIS found itself needing to reinvent its value proposition in the midst of many disruptive forces. These forces included increased competition from industrial supply behemoths with vast order volume and buying power, as well as the need to cater to a more empowered customer base with many buying options. Meanwhile, as Baby Boomers head off to retirement, JIS has had to also redefine its value proposition for a new generation of Millennial buyers with high expectations for an online customer experience.
In keeping with its commitment to add value to processes and reduce waste, JIS set out to offer a frictionless inventory management solution for today’s real-time, always-on manufacturing enterprise. This process began with the deployment of an AutoCrib vending machine system about seven years ago. The machines, which feature integrated barcode scanning, are stocked with up to 5,000 inventory items at a price point previously agreed upon with the customer. Personnel receive a unique pin code and “order” the parts they need for a job by scanning a barcode. Established parameters govern dispensing; for example, workers are given access to one set of gloves every 24 hours.
In 2015, realizing the opportunity to convert these vending machines into “smart machines,” JIS approached MindHarbor for help integrating its vending systems with its Epicor Prophet 21 enterprise resource planning (ERP) system. Once this integration was complete, the two companies began studying the early Internet of Things (IoT) Dash Buttons from Amazon. From there, a plan to engineer a solution to support a simple, on-premise product resupply using WiFi-enabled IoT buttons—known as JIS Express buttons—was born.
Here’s how the system works: At 3 a.m., JIS vending machines place replenishment orders, which are then automatically logged, invoiced and staged with labels and delivery tickets for drivers. The JIS Express buttons, which are affixed to racks or shelving on or next to equipment or drawers, are installed onsite and connected to an on-premise wireless network and the JIS ERP system. The buttons are customized with a distributor’s name and/or the name of a frequently ordered product. Pushing a button triggers an order. One push equals one item at a pre-configured reorder quantity, and a confirmation email is sent to a pre-approved order manager. These confirmation orders include a link to the customer control portal—a secure webpage accessible by smartphone, tablet or PC. The order notification alerts track all buttons pushed in a 24-hour period. The order manager can review, edit and/or approve items ordered in the past 24 hours.
The system batches all items at 3 p.m. every day so orders are built and reviewed daily by the customer. Confirmed orders go directly from the customer portal into Prophet 21 for review and approval and are then either shipped to the customer for replenishment or delivered by the distribution team.
Metrics that matter
With 115 vending machines in the field now integrated into this system, JIS has experienced 30 percent improved productivity, allowing the company to grow without having to increase its headcount. In addition, drivers now cover more ground on any given day when they manually restock machines on their routes, since now all they need to focus on is fulfillment following order directions via an iPad.
JIS has also seen a significant reduction in customer service effort and costs since product costs are now negotiated up front, eliminating the need to quote items for replenishment and manage orders.
Since JIS launched its JIS Express buttons in October 2017, demand has been substantial. The company has been doubling the number of buttons deployed in the field—as well as the number of orders received and corresponding sales volume—every two months.
The buttons have proved to be an exceptional entry-level offering for smaller customers with lower inventory volumes. Additionally, the solution provides a replenishment method to manage and maintain oversized items that are too large to fit into vending machines. The JIS Express buttons cost only $10 to $15 each, as opposed to the vending machines that can run from $10,000 to $50,000.
Additional benefits
Because tool cribs can be a massive inventory black hole—leading to products being lost, horded, misused or simply not used—inventory waste consists not only of the cost of carrying excess inventory, but also the costs to finance, store and handle the inventory.
With JIS Express, JIS brings the concept of just-in-time inventory to a whole new pushbutton level. Effectively, the inventory is consigned yet available only steps away, so manufacturers are billed for inventory as it is dispensed.
This project demonstrates how the digital disruption can bring benefits and efficiencies to the manufacturing floor and the back office simultaneously. Every time a JIS Express button is pushed, it collectively represents hundreds and millions of dollars saved from the perspective of:
- Manufacturing floor workers—reduced walk time and “talk time” to get the tools and materials needed. Improved safety via quick, easy access to all requisite equipment and supplies (e.g., safety glasses, hard hats, etc.).
- Manufacturing back-office personnel—reduced time and effort in contracting and purchase order processing, and improved inventory management visibility, traceability and accountability.
- JIS customer service personnel—reduced time and effort in contracting, order entry and fulfillment.
With its JIS Express buttons, JIS has been able to reach a whole new customer demographic and box out competitors by giving customers a reason to continue giving JIS their business: a smart and easy-to-adopt, just-in-time inventory management solution that offers ultimate convenience and can scale as they grow.
The company’s innovation and growth in its JIS division has also brought another big benefit to the company as a whole—a buffer from fierce economic realities. The company has been paying an additional 20 percent for steel since the tariffs took effect and has had to raise its prices to cover this increase. Jergens anticipates customers will likely push back against further increases, so the growth of JIS via its innovative inventory management solutions provides a solid business strategy to offset these business realities.
As Industry 4.0 continues to have widespread impact in manufacturing, examples of innovative use cases like this one will go from novel to normal. By connecting people, processes, data and things in an intelligent and strategic manner, organizations can streamline shop floor activities for greater efficiency, agility and customer-centricity.
Read the full article here: