The Benefits of Automating your Maintenance and PPE Inventory
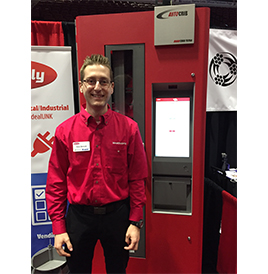
January 4, 2019
By Blake Marchand
Automated vending solutions can help distributers manage customers inventory and reduce waste throughout various industries. They can allow manufacturers the ability to better track inventory, as well as regulate the consumption of everyday-use items like gloves, ear plugs, and tie back sleeves. In machine shops they can be utilized to manage various tools like cutting wheels and drill bits, also ensuring older equipment is used before new inventory. Which not only enables end-users to track and manage inventory, but it allows the supplier to provide a more detailed, customer driven experience.
These machines can vary from the standard coil vending machine you use to buy potato chips and candy bars on your lunch break, to full tool room and warehouse automated systems. With the latter, employees enter the crib with their employee badge or a punch in number, scan the crib for the tool/item they need, press a button that automatically scans the product, issues a receipt, and unlocks the doors.
In the mining industry vending machines are being placed in the mine to distribute PPE (personal Protective Equipment). Auto manufacturers can utilize vending applications to distribute aerosols, cleaners, safety glasses, and other standard tools and equipment.
Ideal Supply, one of Ontario’s premier industrial suppliers, has been providing these types of solutions for two years, and the trend in the industry is growing. Nick Bewick of Ideal Supply explained that they began offering Auto-Crib’s full line of solutions based off demand from their customers and seeing it being used in factories more and more.Inventory can then be tracked and managed through internet-connected devices.
An automated inventory system such as this also increases a manufacturers ability to eliminate unnecessary stockpiles, as well as other inventory inefficiencies like improper identifications and oversight.
Bewick noted one of the biggest advantages is accountability and data collection, “a lot of reports can be generated [with the use of industrial vending],” he said nowadays, “the more data you have the better, you can tie in exactly where everything is being used and where it’s going.”
Machines can be programmed to a specific employee or employee group, a specific quantity, or within a specific time frame. Ultimately streamlining the use of inventory and eliminating misuse. They can also set a minimum threshold for a specific product and have that inventory automatically stocked once that threshold is reached. Which can be particularly useful given the 24-hour nature of the manufacturing industry.
The service is not necessarily a new development in the industry, although due to automation, IoT, and cloud-based technological advancements vending solutions have become a more viable time and cost saving measure.
“I think it will grow in popularity as the technology grows and as it gets out there more, certainly the owners like it because they can track where their product is going, and it also saves on labour costs,” said Bewick.
Ideal Supply’s most popular industrial vending product tends to be carousel/coil crib systems, noted Bewick, along with locker systems. Bewick explained there are not many disadvantages to vending, other than the cost, which can still be prohibitive to smaller operations.
Industrial vending solutions can also reduce the amount inventory a factory needs to carry. With the use of smart bins, lockers, cabinets, and vending machines, real time data is communicated to suppliers and inventory managers so that they know exactly what is being used. The increased capabilities of IoT eliminates latency in the processes, in which data is not passing through multiple digital hands. The result is increased floor space and the ability for facility managers to more accurately target their procurement needs.
For example, Able Engineering used an automated vending solution that automatically replenished their inventory, resulting in a reduction of 41.5% in their tool usage. It allowed employees to focus on value added work, rather than spending added time monitoring tool supply lists, as well as reducing on-hand inventory to free up working capital. Similarly, CNC Manufacturing was able to reduce its tool inventory by 80% using automated inventory systems.
In 2016, the industrial vending machine market was valued at $715.6-million and is projected to reach $1.43-billion by 2025 (Research and Markets). Coil vending machines are expected to be the fastest growing area of the industry due to their ability to hold significant amounts of inventory, low-energy costs, and low levels of maintenance. Carousel style machines, typically utilized to house tools, cutters, and testing equipment are also projected to hold a significant share of the market due to their affordability in comparison to other types of machines such as lockers and cabinets that may require customization. Before cloud-based storage and data sharing, a considerable amount of time and labour was needed to produce the necessary data to share with a supplier. This put the value of the technology into question. IIoT and data sharing has enabled suppliers to eliminate that inefficiency. Since 2008 the supporting technologies required to make industrial vending viable have been developed to the point where it is now a proven practice.