Five Easy Digital Wins for Mining Companies
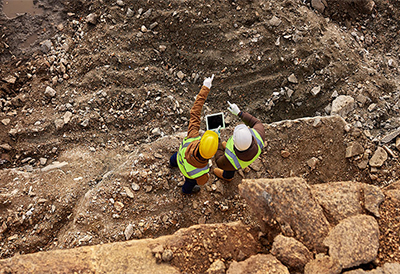
February 7, 2019
By Fabio Mielli, Rockwell Automaiton
Digital transformation provides a major opportunity to address some of the mining industry’s greatest challenges. The World Economic Forum projects that digital transformation initiatives will result in more than $320 billion of value before 2025.
And yet, most digital initiatives are failing.
The problem isn’t isolated to the heavy industries. Last year, a Gartner analyst reported that an estimated 85% of big data projects fail. And Cisco has recently revealed their estimate that 75% of all IoT projects currently underway are failing.
So how can a mining company “go digital” safely? I believe that quick digital wins are the answer. Here are some ready-to-use technologies able to deliver these quick wins and also address some of the major business challenges mining companies face.
Most of these technologies are relatively simple to implement and are also scalable, which means they can be applied in one area, validated, and then expanded to other areas and applications.
One: Augmented Reality (AR)
The concept is well known. The idea is to superimpose digital information onto real objects or equipment. It can be done using tablets, mobile phones and wearables.
Sound complex to set up? Think again! Modern AR technologies allow quick development of applications without coding! And this implementation goes beyond the standard overlay of digital information over real objects: it also enables virtual collaboration.
This means that, in addition to providing field personnel with real-time information in context of the actual process, this technology helps mining companies enable remote expert advice for equipment maintenance, as well as augment the training process to create customized, memorable instruction for new workers.
Two: Hybrid Architectures (when mainstream sensors meet industrial applications)
The beauty of a combined platform is that it allows you to mix data from mainstream low-cost sensors or devices on equipment with industrial automation information. Imagine integrating information from environmental monitoring (from IoT sensing technologies) with real-time production information coming from process automation systems.
In my opinion, incorporating information gathered with IoT mainstream (and low cost) devices into mining automation systems provides a huge opportunity to gain operational visibility, limited only by your creativity. For example, there are ready-to-use IoT development kits for environmental monitoring that can be ordered on the Internet.
Mobile tools, like our FactoryTalk® ViewPoint application, allow field workers to monitor, manage, and control processes in a secure mobile environment.
Three: Mobility
By nature mining operations are very spread out geographically. Field workers often find themselves servicing or operating equipment without a direct view into how the specific piece of equipment is currently performing. This lack of visibility and information can reduce productivity and also result in unsafe operations.
Mobile tools, like our FactoryTalk ViewPoint application, allow field workers to monitor, manage, and control processes in a secure mobile environment. These tools can be accessed via web browser, which means no client software to install and maintain, a lower total cost of ownership, and a more straight-forward implementation.
Four: Analytics
One of the major challenges mining companies face is disconnected and siloed information. It’s a constant struggle to find ways to aggregate and contextualize information from various areas of the business to enable better, more holistic decision-making.
Today, technologies like FactoryTalk InnovationSuite, powered by PTC, exist that allow mining companies to collect structured and unstructured data from nearly any source within the enterprise and quickly build applications and decision tools.
In addition to using analytics to gain broad, operation-wide visibility, you can also use it at a smaller scale to improve equipment performance. Controller-based modules, like our LogixAI module, available this spring, can be plugged directly into your controller’s chassis, where it will analyze device data and automatically build a model for optimal operational parameters.
The module can also monitor equipment performance over time and alert operators when conditions are outside of your set parameters. This means mining companies can begin using self-service predictive, and even prescriptive, maintenance strategies.
Advanced simulation tools like Arena® enable a process called discrete event modeling.
Five: Simulation
Mining supply chains are an intricate sequence of material movements and processes, and there are several potential combinations of material movements across the value chain: extraction, conveyance, stockpiles, processing plant, rail and port.
Simulation tools can help mining companies analyze potential changes to their operations and supply chains, and even incorporate the impact of external factors like weather, market demand and commodity prices.
Advanced simulation tools like Arena enable a process called discrete event modeling. Discrete event modeling is the process of depicting the behavior of a complex system as a series of well-defined events. This works well in virtually any process where there is variability, constrained or limited resources, or complex system interactions.
Discrete event simulation allows users to quickly analyze the behavior of a process or system over time, ask “why” or “what if” questions, and test designs or changes to processes or systems without any financial implications.
These are just few examples of how ready to deploy digital technologies can help mining operations be more productive, cost-efficient, and safe. You can learn more about the ways Rockwell Automation is enabling the Connected Mine.