How Automation and Robotics Will Change Food Manufacturing
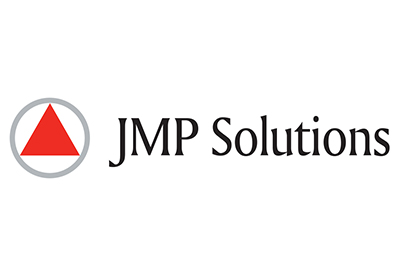
April 18, 2019
Nelson Leite
Director, Sales and Marketing, Automation & Robotics Division
Food & Beverage is one of the fastest changing industries in business today. Consumers are demanding products that can be more difficult to process, and companies need to respond with safe, quality goods that are not going to put off the buyer in terms of price. To stay ahead of their competition and contribute to the bottom line, companies must remain flexible and diligent in making sure their facility is clean in order to ensure food safety.
A key driver for many manufacturers looking at robotic solutions is economics. Because the unemployment rate has dropped significantly, particularly in the area of general labor, and the minimum wage has increased, it is difficult to meet the demand for people. Robots can fill the gap. In addition, cleaning duties on a food line tend to the toughest positions to fill and keep filled, so robots can solve that issue as well.
Robots are more and more being integrated in processing applications in order to save time and space, as well as improving cleanliness and safety. Therefore, robotics can be the answer for manufacturers who need to increase safety in their operations. And, as government regulations become more stringent and competition intensifies, the need for robots is increased in the food & beverage industry. Robots can also increase operational efficiency, throughput and quality, all while protecting employees, the company and maximizing process flexibility.
Good manufacturing practices (GMP) include many basic operational conditions and procedures that are required to be met by food processors. These include the adequate maintenance of equipment and utensils used within the processing business, the use of suitable chemicals within and around the plant including cleaning chemicals, pest control chemicals and machine lubricants, and the cleanliness of the food manufacturing facility, equipment, utensils, floors, walls and ceilings.
Robots, with their small footprint, low cost and high throughput rates, are a valuable addition to this process. By limiting contact with human beings, robots reduce the risk of contamination leading to foodborne illness.
From a food safety perspective, robots can be designed to prevent bacteria, they are easy to clean in high temperatures, and they do not collect dust. That means that they can help prevent food contamination. Robots feature smooth surfaces that are not subject to the harsh corrosive effects of chemicals used to clean the equipment as they are used in the food preparation process.
A key application that robots can play a role in is Clean in Place (CIP) within the plant processes. Clean-In-Place is a procedure for cleaning interior product manufacturing contact surfaces such as process pipes, vessels and equipment, without disassembly. CIP applications have been around for more than 50 years, and use of a mix of chemicals, heat and water to clean machinery. CIP systems circulate detergent and disinfectant solutions and water through the processing equipment. This ensures consistent and high-quality cleaning of equipment surfaces which is critical to food safety.
Typical food and beverage applications are cleaned using an automated CIP system are product transfer lines, processing tanks, homogenizers, mixers, blenders and fillers. The benefit to food & beverage manufacturers that use CIP is that the cleaning is faster, less labor-intensive and more repeatable, and poses less of a chemical exposure risk. In fact, processors can employ a high-speed robotic solution that picks product by day and self-cleans at night.
As pick and place becomes a more prevalent application for robotics in the food industry, it is important to factor in the safety aspects of this growing trend. Robots do speed up the process of food manufacturing and can be customized to fit specific production requirements.
They also can increase output in the plant as they don’t need to take breaks and work at a consistent and efficient speed throughout the shift. In addition, in packaging applications, robots can be equipped with intelligent vision systems that allow accurate placement of products on a belt or in a container that ensure consistency and efficiency.
As manufacturers look to automation to make a difference in their business, they should take a hard look at adding robotics to their operations. Robots provide consistency, they are always available, and they are easily programmed and tooled to provide accuracy, increase quality and keep their products, and their businesses safe.
For more information, visit HERE.