Considerations for Automation Upgrades, An Analytic Approach
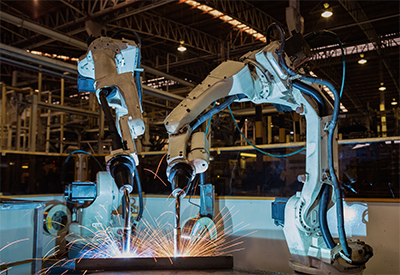
May 29, 2019
By: Blake Marchand
In the past, companies leaned towards moving their operations to developing markets where they could cut costs by finding inexpensive labour. Increasingly, with rising labour rates in countries like China and India (Trading Economics), liabilities associated with LTI (long term injury), and labour shortages, it seems that we are reaching a point where low-skill labour and offshoring is becoming more inconvenient and less cost effective for manufacturers looking to maximize cost efficiencies when compared to the cost associated with automating their factories.
As Glenn Snyder explains in his article The Automation Evolution, “Against a backdrop of developing economy labor cost inflation and other economic trends, automation advances are becoming cost competitive with the alternative of high labor staffing, ultimately decreasing the importance of labor cost as a critical location factor for new manufacturing” (Automation Evolution).
Nevertheless, automating still presents a significant investment as well as risk, in particular if the proper technologies aren’t deployed and if the workforce is not prepared with the required technical skills.
In Canada, aside from increasing labour rates, safety concerns, liabilities, environmental considerations, manufacturers are having a difficult time finding and retaining low-skill labour (Manufacturing in the US, for example, has been steadily rising while the labour force in that sector is steadily decreasing. They are producing more with less workers (Automation Evolution). Despite the potential for automation to take off in the way it has often been theorized, it still presents a large initial investment as well as risk. With respect to the latter it comes down to ensuring you are employing the correct technologies to allow for the maximum return on investment.
In the 1980’s GM made a dramatic shift toward automating its production facilities attempting to compete with their Japanese counterparts Toyota and Nissan. Both of which were producing more cars with less people due in part to automation. As a case study detailed by Snyder explains, “GM failed to account for the indirect labor costs, operators and technicians needed to transition to automation” (Automation Evolution). Additionally, Toyota and Nissan found success because they were designing their components to suit an automated production line. So, two of the issues that got in GMs way were that the workforce wasn’t prepared with the necessary skillset, and their products were not optimized for automated processes.
All of which points to the importance of multi-factor-based decision making.
In his 1993 paper, A Modified Analytic Hierarchy Process for Automated Manufacturing Decisions, Stephen Weber of the United States Department of Commerce presented a formula for multi-criteria decision making that incorporated weighted attributes that accounts for factors that are not easily quantified in financial terms. He modifies the AHP (Analytic Hierarchy Process) developed by Thomas Saaty to suit automation. The example he provides is how to best automate a machine shop.
“Decisions on adopting new manufacturing technologies are often biased because they are based only on those impacts that can be expressed in financial terms. Multi-criteria decision tools that include nonfinancial impacts avoid this bias,” (Weber 75) he explains in his introduction.
Weber placed a weighted value on each identified factor or criteria that correspond with the available automation options (alternatives), which are determined by a mathematical equation. Each alternative will have a score for its financial impact, performance, as well as its long-term strategic benefit. The alternative with the highest overall weighted rating will have the greatest benefit.
“The modified AHP is used here to decide on the best way to automate a machine shop. The four steps are: (1) specify criteria and alternatives; (2) weight criteria using pairwise comparison judgments; (3) rate alternatives with respect to criteria; and (4) compute the overall weighted score for each alternative. This approach preserves existing reliable financial information and integrates it with both nonfinancial quantitative performance data and qualitative informed judgments” (Weber 75).
Weber explains that traditional benefit-to-cost-ratio (BCR) examinations can be misleading due to the long-term benefit of automating.
“The option with the highest BCR may have only a moderate benefit with a very low cost. Since decision makers may select only one option, they might easily forego a preferable option with greater net benefits (Weber 78).”
Typically, and certainly in the early 90’s, automating presented a high initial cost that would become more and more profitable. However, in recent years that initial risk seems to be leveling off. As Snyder explains, “Manufacturing decisions have for so long been driven by cost reduction efforts that production has effectively become a commodity to be procured at the lowest possible cost. The viability of new technologies, combined with other factors, creates long-term options with the potential to set companies apart, if they can maintain the research and development commitment to realize long-term benefits” (Automation Evolution), this means transitioning from offshoring – high volume labour at a low cost, to next-shoring – manufacturing with an emphasis on skilled labour, innovation and proximity to the markets being served, may be key to maintaining success as a manufacturer given the changing industry landscape.
“Ultimately,” Snyder adds, “companies that view the intersection of technology and geography as a strategic manufacturing opportunity are likely to be better positioned as automation changes the game.”
In 2019, it’s not unreasonable to expect a positive ROI (return on investment) by the second year simply from the amount saved in wages. Although, that still depends on the application and the number of workers required. For example, if the initial cost of automating is 400,000 but you can reduce the number of operators required from 8 to 2, and the yearly cost for each labourer is $35,000, than the savings on labour is $210,000; the 2-year cost for manual labour would be $560,000 and the 2-year cost to automating would be $470,000. However, the time frame for your ROI in this scenario hinges on the number of workers required before and after automation. If you require four workers rather than two, the cost over two years to automate in this scenario would be $680,000 compared to $560,000 for manual labour. Precision Automation provides a case study that allowed a customer to reduce their operators from eight to one, saving $548,000 after the second year, “This solution would only require a single production worker per shift. The automation included a robot, tooling, conveyors and the full system installed and integrated on the customer’s floor. The automation solved the challenges with their labor shortage, training and quality. In addition, the customer could re-allocate their labor force to other areas in the plant and discontinued the use of temporary labor” (Precision Automation). Although, this does not account for factors not defined in financial terms or non-salary benefits and training.
For Weber, “the proper approach,” in determining the overall benefit analysis, “is to construct a single consolidated hierarchy including both advantageous (benefit) and disadvantageous (cost) elements, instead of using the two separate hierarchies to form a ratio (Weber 78).”
Weber’s AHP structures a complex decision into a hierarchy of its criteria and the potential alternatives.
“The particular AHP hierarchy I used to evaluate the machine shop alternatives has three levels,” he explains, “Monetary criteria, engineering performance measures, and strategic considerations. Monetary criteria include initial cost, operation and maintenance costs, and training costs. Engineering performance criteria are production rate, cycle time, setup time, and scrap. Strategic considerations are manufacturing flexibility, product quality, business growth, and implementation risk (Weber 78).”
The weighted factors allow the decision makers to put a numerical value to the elements that are not easily calculated in financial terms.
“Once I established the weights and ratings, I combined them to compute an overall weighted rating for each alternative,” Weber continues, “this overall rating equals the sum of the products of the criteria global weights times the criteria ratings (Weber 82).”
In Weber’s machine shop example he presented three options: retrofit with a power feed, digital readout of positions, and numerical control (NC); buy a new computer numerical control mill with an interactive graphic controller (CNC) and computer-aided design (CAD); or replace the mill with a machining centre and programmable tool changer. Weber concluded the hypothetical machine shop manager should select the option with the highest overall rating, which would be the machining centre. The machining centre has the largest initial cost by a wide margin in this scenario. The NC option presented an initial cost of $12,000, CNC with CAD $25,000, and the machining centre $120,000.
The machining centre has the lowest monetary rating, being significantly more expensive initially. However, Weber’s monetary category has a ratio of 0.263, while the strategic category ratio is 0.578 and the performance ratio is 0.159. Meaning strategic considerations are over twice as important. Even though the machine centre is given a 0.063 monetary rating compared to 0.633 for numerical control and 0.304 for CNC and CAD, it ends up with the highest overall ratio because of the benefit it has with respect to performance and long-term strategy.
From a 2019 perspective, criteria that can be added into the equation would be costs associated with long term benefits and injury liability for the monetary category. While the labour uncertainties with respect to finding and retaining quality employees, given in the current manufacturing climate in Canada (Business Development Bank of Canada), could be added into the strategic category. Other factors would include savings with respect to training and non-wage benefits, workers compensation insursance, payroll taxes, and auxiliary safety equipment. From a more intangible standpoint decision makers may also want to factor in safety risks and product loss due to human error.
Despite headway made with respect to education and technical skills, there is still on-the-job training associated with automation, and as new products and solutions are released more training may be required. However, with labour intensive workforce that cost is certainly more significant.
The current state of manufacturing in comparison the landscape in the 90’s, presents an increased emphasis on worker safety and environmental responsibility. In part due to workers rights and expanded human resources considerations, but also because it is more profitable to conserve energy and protect workers from injury. This would include taxes associated with emissions and rising electricity rates, as well as significant fines and lawsuits for unsafe working environments. Ultimately, companies that consider technology and geography strategically will be well positioned to meet the changing industry landscape. In meeting the demands of a rapidly growing market, companies will require the flexibility to work with multiple manufacturer components while maintaining accuracy and speed. Which includes the ability to get product the markets that are being served faster and more reliably.
Sources:
Weber, Stephen f., “A Moduified Anelytic Heirarchy Process for Automated Manufacturing Decisions.” Interfaces, Vol 23, No 4. Jul-Aug, 1993. Pp 75-84.
https://www.arnoldmachine.com/automation-or-human-labor-heres-what-to-consider/
https://www.bdc.ca/en/documents/analysis_research/labour-shortage.pdf
https://p-a-t.com/blog/labor-vs-automation-infographic-how-robotics-can-increase-your-bottom-line/