Benefits of OEM Parts and Repairs
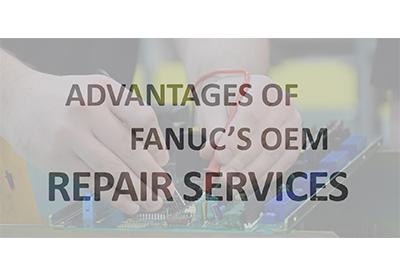
July 16, 2019
FANUC products have a well-earned reputation for performance and reliability. Whether it’s a FANUC CNC system or robot, customers know when they turn on their machines – they will run. Over time however, parts do wear out and sometimes components need to be repaired or replaced. Having a well-thought-out repair and maintenance program in place will ensure that the equipment is functioning for the long-haul, reducing any downtime and of course, keeping the safety of both the equipment and the operator in mind.
The question now becomes ‘who will you use to service your investment?’ Will you consider using a third-party repair company or will you go to the source? Let’s first consider some of the hazards of utilizing the services of a third-party company versus direct support from the original manufacturer.
Concerns with Third-Party Repair Companies
You’ve seen the advertisements. “Our technicians have experience with all major brands.” Of course, these companies are in business to earn a profit from selling parts and performing repair services for a variety of product lines. But, in reality, can they possibly be experienced with ALL of the makes and models of each of the manufacturers?
If you are considering using a third-party, be sure to keep in mind some important determining factors:
- Safety. Since machining equipment operates at very high speeds, even the slightest deviation from the manufacturer’s specification can lead to severe damage the machinery or pose a safety threat to the operator.
- Quality of work. Shortcuts, shoddy workmanship, substandard components. Although some companies may stand behind their work, you may be setting yourself up for additional repair expenses, downtime, and repeat service requests.
- Efficiency. Third-party repair companies don’t know products inside and out the same way the original manufacturer does. Without that inherent knowledge, it’s hard to tell if your repair is being done as efficiently as possible.
- Communication. Any amount of time that your equipment is down is time and money taken away from your operation. That being said, communication is key during this critical period. Lack of communication and transparency only leads to added stress.
Benefits of OEM Repair Services Offered by FANUC
The FANUC brand and its reputation is built largely upon the reliability of its products. Machine and operator safety and a minimal downtime are the cornerstones of the FANUC service philosophy. Our ServiceFirst philosophy means that we make servicing our products and our customers our highest priority. FANUC stands behind its equipment and will never turn anyone away, even if you have used a third-party company to service your equipment in the past.
So, what makes FANUC repairs stand out from those of a third-party repair service? Let’s take a look into some of the benefits:
Standards
FANUC built a reputation for reliability because its products are reliable. They are designed specifically with reliability in mind. Whether it is the size of a bearing, or a microchip in a circuit board, there is no such thing as ‘almost as good’ or ‘practically the same’. Every single part and component that goes into a repair must meet strict FANUC standards. Neither cost nor convenience take priority over reliability and safety. FANUC has our brand and our reputation resting on the performance of our products, and we put a higher priority on their performance than we do on profit.
Parts
Being the only authorized repair facility in North and South America, FANUC has the distinct ability to obtain replacement parts directly from the factory in Japan. Even as equipment ages and new technology emerges, parts are still available. Usage has been anticipated and parts stockpiled to ensure that older models can still be serviced. FANUC provides lifetime support for all of their products as long as they are in use, so you never have to worry about FANUC equipment becoming obsolete.
Because of this strategy, FANUC is able to offer several options to its customers for parts replacements. For example, a customer may purchase a reconditioned or new part and receive it the next day. The customer will also receive a discounted rate or credit when the defective part is returned. Another option is a repair and return service which may require a few more days.
For repairs that no longer make economic sense, FANUC has engineered solutions to integrate modern technology into older platforms. For example, it wouldn’t be cost effective to repair or replace a CRT screen on an older CNC. FANUC developed a plug-and-play LCD replacement to match the specifications of older CNC panels, right down to the mounting screws. In the end, this provides a more cost effective solution with upgraded technology.
All items and parts are serialized to allow for traceability and warranty guarantee. If a part shows repeated issues, it is scrapped and replaced.
Knowledge Base and Experience
As the developer of the automation products, FANUC technicians ensure that all repairs meet factory specifications. If there are any engineering changes, updates are done automatically; something that third party companies cannot offer.
Having equipment in small and medium sized businesses around the world, FANUC has the ability to collect information about durability, life cycle, and repairs, and maintains an extensive knowledge database. Technicians may contact engineers in the facility in Japan for assistance with technical issues if necessary. All repairs are fully documented and shared globally. FANUC has decades of repair documentation to make troubleshooting faster, easier and more accurate.
All FANUC technicians are factory trained. Each technician participates in a dedicated training program locally based on the skillsets needed and then is sent to the FANUC factory in Japan for hands-on training on state-of-the art equipment. The average technician with FANUC’s service team has more than ten years’ experience and many have more than thirty.
FANUC and its trained team of service professionals is dedicated to ensuring that the reliability and efficiency that you are expecting remains consistent during the life of the product.
Protection
So, how do you make sure your parts are serviced by FANUC? If you work through your dealer, distributor or integrator for repair and maintenance, ask that any replacement parts be serviced by FANUC. If you manage your own maintenance, simply contact FANUC by phone, e-mail, or log in to the customer portals. Here you can access pricing, availability, repair times and learn about other available options.
Service contracts are a highly effective way to manage machine maintenance while keeping costs steady and predictable. Service contracts cover a wide variety of repair and onsite service calls and are a high enough value that they typically pay for themselves in a single service call. Talk to your local FANUC representative for more details.
With experience, commitment to customer satisfaction, parts availability, and knowledge, FANUC’s support is second to none. What more do you need when you are looking to ensure the safety of your employees and the longevity of your equipment? Contact your FANUC service technician to learn more.