How to Find the Most Reliable Supplier for 1.27mm pitch Connectors
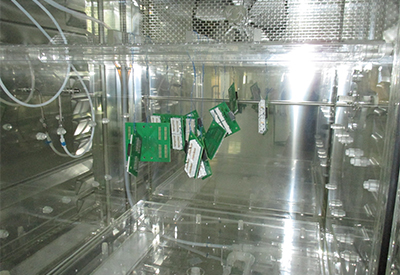
August 22, 2019
By Phill Shaw, Senior Product Manager, HARTING North America
Globally recognized certification standards for connectors offer peace of mind, and are an important tool for original equipment manufacturers (OEMs) and designers.
When PCB connectors are manufactured to a standard, designers and OEMs can rely on the comfort that the components will perform reliably on day one and for many years to come.
However, not every connector type available has a governing standard. Products from different manufacturers can differ considerably, despite being similar in appearance and basic functionality. Most manufacturers provide information about their products, so studying information carefully is critical to making a well-informed decision.
Standards for connectors typically start from a demand for a specific system architecture. This is an important point, as these certification standards are developed as a reaction to a demand, not proactively as new technologies are developed.
Connectors such as DIN 41612 (IEC 60603-2), Hard Metric IEC 61 076-4-101 and VITA46 were all developed for system architectures like VMEBus, Compact PCI, NuBus, VPX and other bus systems. Some connectors are not derived from specific architecture needs, but are made for more general-purpose use. The 1.27mm pitch connector is one such example.
When there is no global standard for a PCB connector…
There is an extra step in the purchasing process when there is no standard to reference – researching and comparing suppliers. 1.27mm pitch connectors have evolved based on the need for a small connecter rather than for a standardized system. As a result, engineers have to sort through different manufacturers to select the right connector for them. This can be challenging, as different manufacturers are not required to comply to a specific rule set.
If there is not a compliance standard, the connector manufacturer should be performing their own tests to guarantee the reliability of their products. A company invested in a reliable product will use guidelines set by standards for similar products to ensure quality in a way that can be easily understood. For example, HARTING developed its 1.27mm har-flex® product line based on another common connector standard, the IEC 60 603-13.
HARTING’s har-flex® was put under several tests for shock, vibration, rapid temperature change, durability and many more. In addition, the information HARTING provides customers is based on common connector standards.
HARTING defines the current carrying capacity data according to IEC 60512-5-2. Working voltage is measured according to IEC 60664-1. This standard sets the minimum insulation distances for equipment, but also can be used to determine the maximum working voltage for certain conditions, such as clearance, CTI-Value, Isolation group, installation category, degree of pollution, etc.
With all brands of 1.27mm connectors, contact durability is an important variable. The highest durability rating is typically 500 mating cycles, which means that the connectors have been connected and disconnected 500 times without contact plating degradation and negative impact on contact resistance measurement. That is a widely accepted benchmark, even if the application for which the connectors are to be used does not involve frequent mating and un-mating.
Some manufacturers may only perform standard contact resistance testing, while others, including HARTING, perform industrial grade testing, as proven in the IEC 60512 test reports. Industrial grade testing is widely accepted benchmark to see if the application is intended for industrial environments.
Standard contact resistance testing without gas tests may not reveal defects that could reduce reliability in industrial environments. Industrial grade testing is important, as it may uncover flaws that would have developed over time in the field. Usually, such flaws are the result of inferior plating materials or thickness to reduce the cost of manufacturing the connector. How a manufacturer tests connectors puts the product’s durability claims in the context of “real-world” applications.
Industrial grade testing usually involves a test that “ages” the contacts by exposing them to adverse conditions to mimic prolonged exposure to environmental conditions in the field. It provides a better measure of the contact reliability provided by the chosen level of plating.
HARTING’s har-flex® testing for Performance Level 1 is recommend for most applications, as it submits the connector to 250 mating cycles. This initial test is followed by mixed-flow gas testing over a 10-day period, then an additional 250 mating cycles, followed by contact resistance testing with final visual inspection. Upon completion, there must be no abrasion of the contact finish through to the base material, and no functional impairment.
The har-flex® is suited for these industrial applications because of the plating materials and quality of the plating process. Its plating consists of a nickel barrier layer and a palladium nickel layer with gold flash, which has proven its reliability during test for industrial grade. This hard gold-flashed palladium-nickel coating is particularly suitable for low voltages typically used for data and signal transmission and in corrosive environments.
When the right tests are not performed, problems can occur
An independent research lab test has proven that some 1.27mm pitch connectors in the market have a minimal gold flash over nickel in the contact area, meaning plating contains only 1 micro-inch of noble metal. The labs performed mixed flow gas testing of those products that claimed 500 mating cycle durability. After the 500 mating cycles were completed, 56 of the 104 tested contacts exceeded the contact resistance limit of 25mΩ. Additionally, traces of corrosion were present.
Corrosion and wear of the plating can have a big impact on the performance of connectors. As contact corrosion will accelerate over time, the potential for performance degradation – even the failure of the machine or device dependent on that PCB – will increase accordingly.
Corroded contacts can be the result of simple wearing of the gold or other plating down to exposed contact material. The manufacturer may have plated to their required thickness, and the surface may look good to the naked eye. However, microscopic examination reveals pores in the plating, a process defect that exposes the base contact metal.
When making a decision, talk to the source of the product
In selecting PCB connectors, some customers always settle for the cheapest version of a product, even if it means accepting lesser quality. Others have very strict performance requirements, defined to meet an internal standard or market requirement. The latter might insist on a specific plating thickness, like 50 micro-inch of gold plating, a requirement non-negotiable within their specific industry. Most customers fall in between these two extremes.
In making purchasing decisions, no extensive technical knowledge about plating materials is required. However, in the absence of a system standard, communicate with the manufacturer to ensure the product will perform to your expectations. Learn more about contact plating by reading this plating guide.
Go HERE for more information