Why Your Digital Initiatives Need a Strong Partner Ecosystem
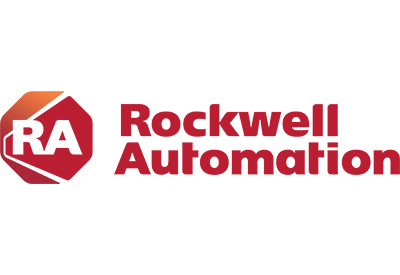
November 25, 2019
By Chirayu Shah
Sometimes, when we’re presented with disruptive change – like we are today with the industrial IoT – we can learn a lot by looking to the past.
For decades, industrial producers have built their production systems by turning to a mix of vendors – distributors, machine builders, system integrators and many others.
And often, these vendors have worked to create relationships or even formal partnerships with each other. Why? To improve how their technologies work together, fill gaps in their product portfolio and offer more robust services to customers.
The benefits of working with this ecosystem of closely aligned partners are clear. You don’t just get pieced-together production systems. Rather, you get well-integrated systems that can be deployed more easily and deliver more ROI when production starts.
Today, this ecosystem approach is needed more than ever, if you’re deploying industrial IoT technologies to improve your business.
By working with allied and partnered vendors, you can more quickly deploy new digital technologies. You can better solve challenges like data-integration issues and security risks. And ultimately, you can capture more value from the technologies to help meet your business goals.
Finding the Right Digital Partners
You may think you can work with a single vendor to implement industrial IoT technologies. But the truth is, nobody can do the job alone.
Challenges like combining different data sets and securely deploying technologies across multiple organizations require the support of several partners – like cloud providers, security experts, smart-device and smart-machine suppliers, and more.
But how do you determine who you should work with? And how do you get the most from them, not just as individual partners but as a whole ecosystem?
Experience should be a top priority. It can be hard to put your trust in someone to implement your digital initiative, if they can’t show results they’ve achieved for others – especially those in your industry.
Also, your partners should be able to show they have strong relationships. It’s one thing to have a collection of partner logos on a website. It’s another to have long-time strategic alliances and partnerships with others.
Finally, this may seem like a given, but make sure any potential partners have your best interests in mind. For example, do they challenge your ideas they think are unrealistic? Are they dedicated to making sure you get the best results from your digital initiative – like the highest uptime, the best quality or the fastest repair times?
Again, look to the past. Does a vendor, for instance, still support decades-old, discontinued products that customers are still using? Or are they only focused on selling their newest products?
Partnerships in Action
Companies across industries are forever changing how they operate by working with partnered vendors for their digital initiatives. Here are just a few examples.
Food and Beverage: When Great Lakes Brewing Company wanted to scale up production without sacrificing product quality, it turned to an analytics solution that was collaboratively developed by two giants in the automation and technology worlds.
The solution provides health and diagnostic analytics from devices on the brewery’s plant floor. It can also interact with production staff using natural language processing to help them identify and address equipment challenges in real time. Now, staff can use a wealth of existing data to solve problems quickly.
Life Sciences: Swiss pharma maker Lonza is tapping a strategic partnership between two automation and IoT solution providers to enable new ways to develop and deliver its life-saving cures.
The company will use the vendors’ joint industrial IoT software offering in nine of its facilities that make drug capsules. The goal: improving product traceability down to the individual capsule carton level and gaining new insights into performance and production.
Mining: One mining company is using a jointly developed industrial IoT solution that combines mine equipment, data and cloud computing to improve its performance. The solution helps mine workers understand process performance and even predict component wear and failure.
In one instance, remote experts used the tool to look at data from a crusher that was experiencing excessive vibration. They found the machine was coming loose from its foundation. This allowed the mine to fix the problem relatively quickly and easily, avoiding a big breakdown that could have led to costly repairs and lost production.