When is a Cobot Right for You?
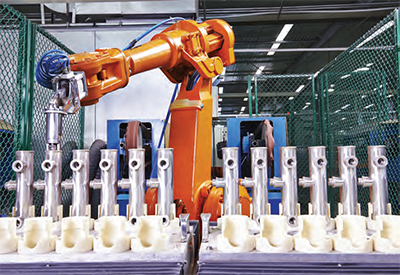
January 24, 2020
By Blake Marchand
Robots – or more specifically cobots, may or may not be coming for your job. But they may very well make it easier.
Robotic systems are most commonly utilized in self contained fenced off configurations with significant safety measures to keep workers safe, although in recent years cobots have begun increasing market share.
Automated robotic systems generally take up significant floor space, are designed for a specific application or product, and require complex programming to integrate into production. This makes them lucrative in high-volume, heavily automated production lines. But for small and medium size operations or low-volume manufacturing, those systems are likely either too expensive or not flexible enough to make sense financially.
On the other side of the industrial robotics spectrum, collaborative robots (cobots) are smaller, portable, more scalable, more affordable and can be used alongside operators. Their versatility and relative affordability increase the ROI (return on investment) potential for small and medium sized enterprises. Cobots are designed to be user friendly. They can be programmed with script or visual flowchart software, as well as by physically guiding the robotic arm through the required movements.
“Configuration software is flowchart-based with standard drag-and-drop functions. Minutes after unboxing and watching an introductory video, users can be training a cobot to move. Some cobots offer multicolor indicator lights letting users know exactly what mode the cobot is in, while a handheld pendant control interface allows users to stop and replay preconfigured actions,” explains the experts at Allied Electronics and Automation.
Stuart Shepherd of Universal Robots adds, “They are easy to program, simple to use, and some even utilize AI and machine learning to enhance their performance or usefulness over time.”
This cuts into programming cost and set-up time, allowing cobots to be programmed for quick changeovers. Generally, a cobot can be programmed for multiple functions, and the tooling at the end of the arm can be easily switched out for different applications.
Like robots, cobots are heavily regulated for safety and will require a risk assessment. Because robots are typically operating at high speeds with large payloads, they are caged off and equipped with sensors to protect against human interference and injury. Cobots operate alongside people so they are regulated for speed and payload and equipped with various sensors to avoid collisions.
“Cobots are designed to comply with ANSI RIA and ISO safety requirements and standards. Besides the ability to interlock with traditional safety sensors, cobots protect nearby humans by using low inertia force torque limited servo motors, force sensing, elastic actuators, collision detection and safety-rated axis limits to prevent injury from contact,” note the experts at Allied Electronics and Automation.
That puts a limit on what they can do. The positive is they can be utilized to enhance production working alongside operators by taking up repetitive tasks, increasing accuracy, and limiting waste. With their consistent, regulated speed, production lines can be closely synchronized. Adding to potential output.
“Cobots protect human workers by reducing the risk of injury from dangerous jobs and repetitive movements, and they improve overall equipment efficiency—all while enabling human workers to get their jobs done faster and more easily than ever before,” explains Shepherd.
Another benefit associated with cobots is to alleviate worker shortages. Shepherd touches on this while also addressing the concern of robots taking jobs.
“What’s interesting is that, in reality, demand for manpower is actually outpacing supply. Baby boomers are retiring, and Gen-X, Gen-Y, and Millennials are not interested in manufacturing and warehouse jobs. There simply aren’t enough human workers to get the job done.”
Cobots are ideal for repetitive tasks that require interaction with people but don’t require a high level of dexterity. They save workers from repetitive task/ergonomic injury, while also limiting interaction with potentially dangerous machinery. Adding to ROI and protecting companies against potential liability.
Currently, cobots are used most in applications involving machine tending, pick and place, packaging and palatizing, quality control, as well as in flexible manufacturing assembly. As well as finishing applications like welding, polishing, grinding and gluing.
They are great for high variety, low volume product manufacturing operations because they can be programmed for multiple functions, easily re-tooled and can be mounted to portable workstations.
Ultimately, determining when cobots are right for you comes down to the particulars of your operation and the goals you want to achieve. Are you looking to complement production lines or fully automate? How much floor space do you have? Are your payload requirements compatible with cobots? What are your long-term goals for growth? Is scalability important? It is important to assess all possible scenarios.
But perhaps the most important factor is ROI. What is going to provide the maximum benefit for your investment? With automation there are a number of factors that aren’t so plainly quantifiable in financial terms. Quality, waste, production rate, cycle time, set up time, manufacturing flexibility, business growth and implementation risk, should also be considered.
The most expensive, high tech option isn’t necessarily going to translate into the greatest return. Adversely, the cheapest option won’t necessarily provide the greatest value. When deciding if cobots are right for your operation it is important to weigh all potential variables to determine what is going to provide the best value for your investment.