Upgrading a Manufacturing Plant to Meet Production Demands
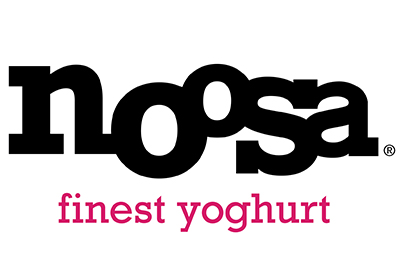
March 2, 2020
Panduit IIoT ecosystem helps noosa yoghurt speed production at maximum efficiency while increasing network reliability and productivity.
At the recommendation of Malisko Engineering, Inc., a Panduit ONESM Gold Partner, noosa yoghurt consulted with Panduit Advisory Services to design the complete physical layer of its new industrial network. Malisko Engineering is strongly committed to working with Panduit to help deliver the most efficient solution and superior value to noosa yoghurt. The Panduit/Malisko Engineering collaboration prompted noosa yoghurt to deploy a network design that aligns with the Converged Plantwide Ethernet (CPwE) Cisco Validated Designs (CVDs) to reduce risk, time to deployment, and total cost of ownership. Malisko Engineering was also responsible for the full logical design and configuration, including specification and commissioning of the active network and security gear.
Business Challenges
noosa yoghurt’s commitment to making a superior product propelled the company to invest in a $5 million plant upgrade that was completed in 2015. This project allowed noosa yoghurt to increase production and nationwide awareness of the brand while remaining a leader of current dairy and food trends.
As the original plant (built in 2012) increased production, a small, standalone industrial network grew organically as product demand surged. As the network grew without standardized methods, it became cumbersome to troubleshoot, often resulting in costly unscheduled downtime.
Documentation of the plant’s physical network infrastructure was minimal, and as cable rerouting and building designs changed, it was clear that the old network could not support the expansion because it lacked the inherent scalability of today’s future-ready industrial networks.
As a greenfield installation for the expansion, a standardized design would allow noosa yoghurt to work on different cells, one zone at a time, without affecting production uptime. In addition, the zone placements could be broken up by functional areas, complementing a future-ready, segmented logical design.
With both enterprise and plant floor network workstations in the same locations throughout the plant, the company also needed to assure a clear demarcation between enterprise and manufacturing zone network resources. This would allow these critical networks to coexist without adversely affecting one another in the case of a network event.
Strategic Objectives
The plant upgrade would position noosa yoghurt to maintain a competitive advantage while solidifying its position as a major contender in the food and beverage industry. The upgrade would also allow the company to increase its quality of service through improved network traffic and increased network uptime and availability.
In addition, it was important for noosa yoghurt to establish a solid network infrastructure that uses standardsbased design elements to comply with current industry regulations. Executing these improvements would give noosa yoghurt the ability to expand into additional markets.
To address these challenges, noosa yoghurt needed a robust, future-ready solution that could accommodate its expected growth, decrease downtime, and promote product standardization.
{videobox}2h1nHpGU5l4{/videobox}
Design
The new design was created under CSI Division 27 specifications. It comprises various systems from the Panduit offering and has allowed noosa yoghurt to simplify its industrial network and IIoT deployment. These systems include a manufacturing fiber backbone, enterprise fiber backbone, and a spare fiber backbone for future scalability.
Panduit provides expertise in physical infrastructure deployment for CPwE using best practices and a building block approach. This approach allows noosa yoghurt to achieve a simplified, resilient network and IIoT deployment designed to enhance industrial network performance.
Malisko Engineering recommended a structured cabling approach using permanent links for copper end points out in the field, improving operational efficiency, productivity, and flexibility. The design team communicated best practices aligning with TIA standards and helped noosa yoghurt adopt the use of DIN rail mount patch boxes and single-port patching inside control panels. To mitigate risk and achieve resiliency in critical process areas, Malisko Engineering incorporated both redundant star and REP ring topologies in various areas of the plant. Additionally, the design called for redundant backbone pathways from one end of the plant to the other. This ensures continuous availability between the server room and the network core located in the middle of the plant.
The solution for noosa yoghurt’s 32,000 square feet new facility consists of the Pre-Configured Micro Data Center (MDC), Switch Ready Network Zone System, Pre-Configured Industrial Distribution Frame (IDF), control panel solutions, and fiber and copper connectivity. The CPwE CVDs that Malisko Engineering specified were developed through strategic partnerships with Cisco (networking and switching technology) and Rockwell Automation.
Connecting the Enterprise to the Plant Floor
The MDC facilitates the connectivity from the plant floor to the enterprise, giving greater visibility into the manufacturing processes to quickly identify problems and maintain network uptime. The MDC is in a small telecom room that houses the server assets for manufacturing operations. It includes a fault-tolerant server running several virtual machines for the plant’s automation system in addition to the network and security hardware required to build a robust Industrial Demilitarized Zone (IDMZ) between the enterprise and manufacturing zones.
Distributing Ethernet Throughout the Plant Floor
Integrated Network Zone and Switch Ready Network Zone Systems are deployed throughout the industrial network. The Integrated Network Zone Systems use Rockwell Automation Allen-Bradley® Stratix™ Industrial Ethernet switches along with a battery-free, Ethernet-enabled Uninterruptible Power Supply (UPS) to reduce maintenance and ensure maximum switch uptime. The Switch Ready Network Zone Systems accept managed switches from various manufacturers to provide flexibility.
Along with the network zone systems, noosa yoghurt specified NEMA 4X stainless steel sloped-top zone enclosures. The enclosures were designed and developed for harsh washdown environments such as those found in the food and beverage industry. Each enclosure features corrosion resistance and mechanical strength, important qualities on the plant floor. In addition, the enclosures prevent contamination and are easy to clean and maintain, which helps to improve hygienic conditions. The sloping feature allows for quick washdowns and prevents water from collecting on the top of the enclosure.
A later addition to the project was a network zone enclosure housed in noosa yoghurt’s remote waste water treatment building. This network zone houses a layer-3 Stratix 8300 switch and was configured to act as an autonomous network while still maintaining connectivity to the main network core.
An IDF was selected for quick deployment and protection of noosa yoghurt’s rack-mount Cisco StackWise Ethernet switches. These switches serve as the network core.The IDF also helps achieve rapid and easy maintenance of network switch equipment. Located centrally on the plant floor, the IDF accommodates a three-switch stack acting as the distribution/core switches. Centrally locating the network core aided in establishing shorter fiber runs from the network core to the various zones in the process areas. noosa yoghurt used Panduit 8-inch one-to-one patch cords and various wire managers to connect the Cisco switches, resulting in a well-managed, easy-to-service rack.
Tested and thermally verified by Panduit Laboratories, the IDF achieves 25% faster installation than a nonpre-configured IDF installation. The additional back-end space allows for 3X the cooling capacity over typical deployments for increased reliability. Provisions for optional AC units, if required, are provided.
Connecting the Machine to Plant Floor Architecture
noosa yoghurt incorporated Panduit IndustrialNet patch cords to support Industrial Ethernet from the Local Area Network (LAN) based support offices to the processing devices on the plant floor. The industrial Ethernet patch cord is a key component to an overall Industrial Ethernet application. It is the interface that protects the integrity of the Ethernet data transfer from the switch or PLC out to the devices or up to the horizontal plant backbone.
Deploying Ethernet on the Machine
The backbone of the industrial network consists of Dielectric Conduited Fiber (DCF) OM4 multimode fiber to meet current environmental requirements and future performance needs. DCF fiber provides high-density connectivity and ease of installation within buildings and allows easy troubleshooting for noosa yoghurt’s network connections. The J-Pro Cable Support System routes the DCF fiber, maintaining bend radius control, which helps prevent degradation of cable performance. In addition, the conduited cable is color-coded aqua for easy identification in noosa yoghurt’s existing pathways, which also contains various power cabling and pneumatic tubing.
Strengthening the Network from the Ground Up
The grounding and bonding system reduces intermittent failures and personal hazards. Visually verifiable connections and dedicated grounding paths help maintain noosa yoghurt’s system performance and protect personnel and equipment.
Business Benefits
noosa yoghurt’s new industrial network system supports the increased production demand while effectively managing risk to its physical layer. This decreases challenges in its physical infrastructure as it increases network availability and reliability. Panduit Advisory Services and Malisko Engineering understood the importance of the logical and physical topologies to meet system requirements and identified future growth needs while suggesting suitable solutions.
Rexel’s technical assistance and history of working with other partners in the ecosystem helped to ensure the products were on site in a timely manner. This positively impacted supply logistics and allowed the installation to remain on schedule. Piper Communication Services, Inc. handled the electrical and office low voltage installation and submitted the 25-year Panduit Industrial Automation Certification PlusSM System Warranty. This warranty provides noosa yoghurt with the assurance that its newly installed cabling system will meet performance expectations and future networking needs.