A Recap of International Robot Safety Conference and Predictions for the Future
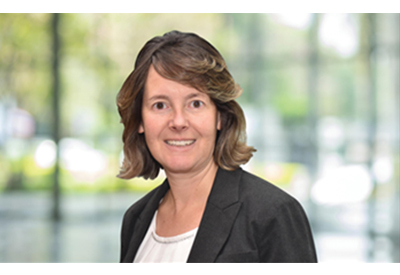
March 9, 2020
By Tina Hull
Gone are the days when the primary examples of robotic safety were electromechanical switches on automotive welding systems. At this year’s International Robot Safety Conference in Indianapolis, Indiana, most presentations featured solid-state technology used with mobile and collaborative robotic applications in the packaging or warehouse industry.
These trends are very exciting for anyone using Omron products, since we already have the most extensive product range to support them. If our AI Controller is any good indication of where we’re going, the future is so bright that we’d better start wear shades.
Omron’s presentation at the conference
I had the pleasure of representing Omron at the conference with a talk titled “Demystifying the Use of Category 2 and Category 3.” The current industrial robot standard, ISO 10218 / ANSI RIA R15.06, has a minimum requirement of PLd with structure category 3 or SIL 2 with HFT=1 and a proof test at least 20 years unless the risk assessment allows for something different.
In my presentation, I focused on ways that technology has expanded to design a system that is just as reliable using a Category 2 architecture with reasonable diagnostics. One thing that remains the same is the importance of doing a risk assessment. The processes described in ISO 1200 and ANSI B11.0 have proven themselves to be suitable for just about any system.
More attention is being devoted to the verification and validation (V) model. An example of verification is when a programmer uses the simulator in Sysmac Studio to check their logic flow. Validation, on the other hand, would be when an operator makes sure the logic works correctly on an actual system.
What developments will we see in the near future?
Based on the presentations I saw at the event, here are some of the predictions I came up with for the future of robotic safety solutions.
- 1. Safe motion technology – including functions such as STO found in the MX drive, G5 and the 1S servo controller – will continue to expand.
- 2. Integrated 3D vision will be used as a means for speed and separation distance. At the moment, nearly everyone – including Omron with the OS32C – uses safety area scanners.
- 3. More new devices will be embedded and will use solid-state technology. (Did you notice that companies haven’t been releasing new electromechanical switches lately?) Fun fact: a transistor can switch up to 150 times faster than an electromechanical switch!
- 4. There will be a greater understanding of how humans respond to and interact with machinery, and human-to-robot interfaces will grow in importance. (If your boss sends you to a psychologist, it might be for a “top secret” work-related project!)
- 5. We’ll see more methodology to counter the effects of cybersecurity breaches on functional safety. Right now, the best resource are white papers from the National Institute of Standards and Technology (NIST). Of course, using the SQL database is an easier way to keep information isolated from outside threats.
- 6. The use of the term “robots” is expanding to cover more than just industrial robots. While it continues to be strong in the automotive industry, it’s quickly growing in the packaging, distribution centers and service industries. The fleet manager software with the LD mobile continues to be a clear winner with its tracking capability.
- 7. Modeling will transition from predictive systems (i.e. ISO 13849-1) to adaptive systems (with the use of AI). Omron’s Forpheus robot is an excellent example of an adaptive system.
Be sure to mark your calendars for next year’s conference, which will be held at the Hyatt Regency Hotel in Columbus, OH on October 13-15, 2020. Also, stay tuned for future webinars that discuss the current trends in robotic safety measures and more.