4 Ways Automation Technology Makes Things Better for Customers
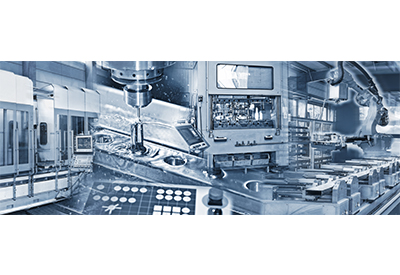
March 11, 2020
Whether it’s increased productivity, lower costs, greater flexibility, or reduced time to market, we often talk about the benefits of automation technology as they relate to manufacturers. The right technologies, incorporated effectively into the production processes, can make a significant difference on your business results.
What’s missing from these conversations around efficiency and throughput, however, is how technology impacts the customer. As competition increases and consumers have more choice than ever before, manufacturers need to understand how the equipment, systems, and processes they put in place can be used to benefit consumers and create value that keeps them coming back.
This article will shift the perspective and explore four ways that consumers benefit when automation technology is implemented in your facility.
New product innovation
Customers have grown to expect constant innovation. From the latest smart phones to new flavors of toothpaste, innovation occurs at an almost overwhelming rate. It’s not long before trends change, and the hottest product is replaced by something new. This, of course, benefits consumers by giving them more choice, but it also places pressure on manufacturers to keep up.
By leveraging data to predict trends and installing flexible, agile, and adaptable equipment into manufacturing facilities, some brands have been able to take this to the extreme and disrupt entire markets in the process. Fast fashion brands, for example, have compressed the design, manufacturing, and distribution cycle from months to weeks or even days. Customers can find something new every time they walk into a store, while the brands themselves can offer the latest looks at a low cost.
Increased product availability
Running out of inventory is expensive, and a missing component or supply chain issue can shut down production lines and create bottlenecks that lead to costly delays. In a time when online shopping has trained customers to expect that products will always be in stock when they want them, shortages mean lost sales, reduced customer loyalty, and long-term damage to your reputation.
This can have a huge impact on customers depending on the type of product. Drug manufacturers, for example, need to ensure people have access to the medication they need. Advanced data and analytics technologies allow manufacturers to manage inventory, forecast demand, and avoid shortages. Not only does this reduce cost and risk for the manufacturer, it also benefits consumers who can be confident they can get the product they want when they walk into a store.
Personalization at scale
Mass production has led to incredible advances in efficiency and has allowed manufacturers to take advantage of economies of scale. Personalization, on the other hand, has historically been an entirely different approach. Until recently, it was possible in relatively small batches but increased costs, lead times, and complexity.
All of that is shifting as customers demand more personalization and customization. Automation technology such as additive manufacturing and more adaptable robots are allowing companies to scale up personalization at little to no additional cost. One company, for example, lets customers design their own reusable bottles by uploading graphics, specs, and details such as size and colour. On a larger scale, automotive companies let customers design their entire vehicle, choosing everything from features and options to colours, materials, and accessories. That’s a big shift for an industry famous for Henry Ford’s quote, “you can have any colour you want, as long as it’s black.”
Improved product quality and safety
Technology advances are reshaping the way companies manage product quality and safety both before and after products leave the factory. Connected sensors capture data throughout the manufacturing process to detect defects or production issues as they occur, greatly increasing quality assurance and reducing defect rates. In other cases, companies can trace issues back to a specific batch, lot, location, or time, improving responsiveness and speed in the event of a recall.
Take, for example, food and beverage companies. As soon as an issue is identified, they need to react to ensure customers are safe. By being able to narrow down the affected products and communicate that information to customers, they can avoid pulling back hundreds of thousands of millions of dollars worth of products while also keeping customers safe and confident in the brand. Whether the issue is caused by a supplier, a piece of equipment, or a distributor, manufacturers can limit risk and ensure product safety for customers.
Giving customers what they want with automation technology
Faced with so many options, consumers need a reason to choose your brand. Manufacturers must think about how the technology they install benefits not just the production processes, but the end customers as well. They are the people who are going to be buying and using your products. By seeing automation technology as a way to achieve a competitive advantage, manufacturers can capitalize on these opportunities and make things better for their customers.