The Importance of Label Verification in Automotive Manufacturing
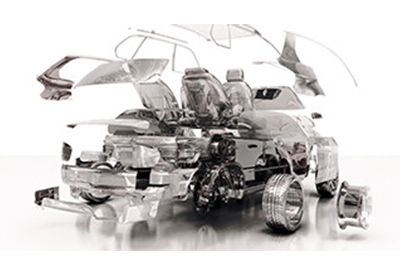
March 23, 2020
As many as 20,000 individual parts go into the production of a single vehicle, and each of these parts must be subjected to rigorous tracking. There are many ways to mark a part – including laser marking, dot peening, inkjet marking and labeling – and automakers generally use several of these, depending on the situation.
Labeling is one of the easiest methods for quickly adding identifying information to a particular part. Although it’s not permanent in the way that laser marking and other direct part marking methods are, labeling works quite well for a broad range of marking needs.
Because traceability is so essential to the automotive industry, it goes without saying that labels must be thoroughly verified before being added to a part, as well as during various stages of production. Here are some reasons that a rock-solid label verification system is essential for automakers.
Labels need to be readable throughout the production process
High heat, harsh chemicals, grease and pressurized water jets are characteristic of any automotive manufacturing facility. All of these elements can damage labels, even if they’re designed to be sturdy enough to hold up under such conditions. If the barcode on a label is significantly affected, it could trigger a no-read on the production line.
Depending on how the system handles them, no-reads can cause production delays that extend beyond the original item with the damaged label. Since automotive manufacturing is such a resource-intensive process, no-reads can cost the facility significant amounts of money if the part in question is allowed to proceed to far along the line.
Omron’s label verification systems use advanced algorithms to analyze barcodes and grade them according to a variety of ISO standards that designate the parameters for code integrity and readability. The LVS-9510 desktop barcode verifier, for example, uses a “stitching” feature that allows it to verify barcodes that are larger than the field of view.
Barcode verifiers from Omron provide detailed reporting on every aspect of symbol quality in an easy-to-read format. The LVS-9580 handheld barcode verifier, for example, shows a complete color-coded analysis to pinpoint exactly where readability problems are located within a symbol and help determine ways to solve the problem.
Labels need to accurately represent the item carrying them
Throughout the production process, labels – as well as other forms of part marking – are responsible for ensuring the correct movement of a vehicle’s component parts throughout the supply chain and providing necessary information on component-specific maintenance and safety.
It’s a serious problem if a label doesn’t represent what it’s supposed to represent, especially as automotive manufacturing becomes more automated and the information contained in labels plays more of a role in directing manufacturing processes. With incorrect information, the part could potentially be incorporated into the wrong vehicle.
In many cases, the issue is a mismatch between the human-readable information and machine-readable information on a part. Omron’s barcode verification systems perform simple validation of human-readable information and can check the results against the data gleaned from code to ensure that everything matches.
The LVS-7510 and other in-line label verification systems from Omron are integrated into standard thermal transfer printers, unlike the handheld off-line verifiers like the LVS-9580. Omron’s verification solutions also provide logging functionality allowing quality results to be exported to a database. In the event of a label error in an in-line system, the printer is stopped so that the defective label can be removed before it enters the supply chain.
What are some important labeling standards that apply to the automotive industry?
The Automotive Industry Action Group (AIAG) has put forth several key standards related to labeling and identification that all automakers should pay careful attention to. Another source of labeling-related guidelines is the Code of Federal Regulations (CFR).
Some of the most prominent labeling standards are the following:
- AIAG B-4, which provides requirements for parts identification and tracking
- AIAG B-10, which supplies criteria for printing unit load and package transport labels to ensure that they can be scanned easily
- AIAG B-16, which gives specifications on global transport labels for automotive manufacturers
- 49 CFR Part 541.5, which offers requirements for identifying numbers on passenger motor vehicles