Augmented Reality Modernizes Technical Support in Manufacturing
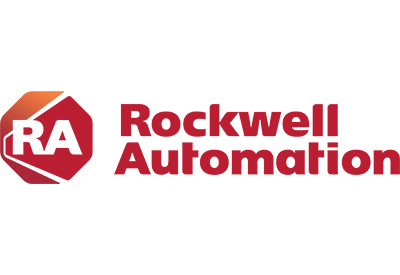
April 2, 2020
By Tim Brennan, Product Specialist for Innovative Technologies, Rockwell Automation
Machine downtime hurts. It hurts productivity and profits – and it causes frustration. Every minute that slips by with a machine unable to operate negatively impacts the bottom line. So, it’s no surprise that manufacturers are looking for the most cost-effective and time-efficient way to get the technical support they need to deal with downtime and repairs.
In many situations, technical support via a phone call with a knowledgeable advisor provides the answers you need to fix a problem. But other times, the issue might be more complex or unfamiliar. There can be a variety of obstacles to getting a machine up and running – including having workers who don’t have the necessary skills. Other barriers include:
- – It can be hard to describe a problem or know exactly what went wrong
- – If the directions from a technical support person are complex, it might be challenging to understand them – especially if you have no experience with the problem at hand
- – If you misunderstand the tech support directions, you may accidentally take steps that make the situation worse rather than better. That’s a common risk with potentially serious consequences.
- – Depending upon the time of night or day, a trained person may not be on-site. And with the skills gap widening, it gets harder to have a trained person always on hand.
And here’s the real time-killer: If the problem is serious enough that it requires an on-site visit, time is lost while the technical expert travels to the site. If the problem is in a remote location, travel time could amount to a day or more – rather than hours. And lost production time grows.
Of course, it would be ideal if a technical expert could be on hand, ready to respond on the plant floor for every maintenance issue – explaining and coaching to get the problem solved quickly and correctly. Unfortunately, that isn’t possible for many manufacturers. That’s why we’re introducing the Live View Support tool, which leverages PTC augmented reality (AR) technology to help you solve your most complex plant-floor problems.
What is augmented reality and how can it help manufacturers?
From retail giants like IKEA to the gaming experts at Pokemon Go and even the U.S. Army, companies and organizations have begun to harness AR to superimpose images on real-world views. Now, manufacturers are applying AR to the plant floor to help troubleshoot problems in real time.
Using an augmented reality application with live video feed, an experienced technician can view your equipment in real time and provide specific, detailed directions for repairing the hardware. 3D spatial notations can even be made on the screen, so you know exactly which component of the machine needs attention. And, for flexibility, the Live View Support tool is platform agnostic, so you’re not tied to a specific brand of mobile device or communication equipment.
As an added benefit, the on-site employee receiving directions is far more likely to remember how the repair was done, in case a similar situation comes up again. This is a modern answer to a long-existing problem, helping to provide thorough instructions that can be immediately carried out.
Most of us have experience using Facetime or Skype on our phones or tablets to stay in touch with friends and relatives. The Rockwell Automation Live View Support tool provides a similar but far more enhanced experience. With the Live View Support tool, a Rockwell support person can actually draw on the screen and mark an area to be addressed. So, you know exactly which cable or piece of hardware needs attention. The notations and lines stay in place on the screen view of the machine so there is less room for error. Live View Support also addresses background noise. Having specially designed noise-canceling headphones allows the person receiving information to hear the directions clearly. This allows troubleshooting to be done directly on the manufacturing floor.
Another advantage of using the Live View Support tool is that it helps protect your company’s proprietary information. Confidential data about a machine or application clearly has great value. To help protect sensitive communication, we guard both the audio and visual communication between the technician and on-site worker. During a Live View session, the participants’ video and audio “packets” are transmitted directly to each other – with no intermediary.
AR and TechConnect: An enhanced support experience
The new Live View Support tool is scheduled for availability in the spring of 2020, and we’ll be making it easy for you to enjoy the benefits. Downloading the tool is free and Live View Support will be a core feature of product support with a new or renewed TechConnect contract – at no additional cost. We’ll even help you get your hands on the noise-cancelling headphones with Bluetooth.
Rockwell Automation Product and Application Support Services help manufacturers of all sizes in any industry. And now, we’re modernizing the way we work with you to provide an even better technical support experience, so that downtime doesn’t have to hurt so much. Watch for additional information in the coming months and get ready to make augmented reality your plant floor reality.