Stay on Top of Alarms and Production Problems With the Right HMI
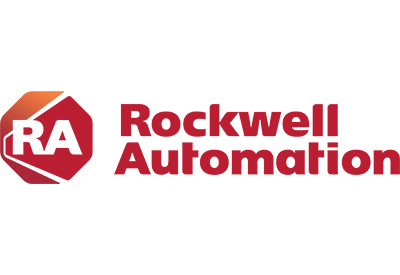
April 6, 2020
By Susan Burtch, Visualization Software Marketing Manager, Rockwell Automation
When a machine component fails or operating conditions start to change, the first sign for workers that something is wrong is often an alarm in the HMI. Factors such as how accurate, detectable and informative the alarm is can directly affect how quickly workers see and react to it.
That’s why many industrial producers have made the move to using modern HMI software.
Modern HMI software that is integrated with the production system can deliver more detailed and effective alarm information than HMI software of the past, giving workers more reliable visibility into critical conditions. The software also allows you to take advantage of advanced features like alarm commands and mobile access to alarms, which can help workers more quickly identify and resolve issues.
With modern HMI software, you can improve your approach to alarming in three key ways:
- Improved Speed and Accuracy
Traditional tag-based alarms monitor data points in a controller to look for state changes, routing the information to the alarm manager and alarm log. This approach is effective, but has some drawbacks.For example, the alarm tags must be configured in both the controller and the HMI. Alarm time stamps are also delayed, because they are applied by the HMI after polling and processing, rather than immediately when the alarm occurs.
Modern HMI software gives you a second option: device-based alarms. These alarms are detected and managed in a controller, which means alarm timestamps are applied immediately, rather than delayed until the alarms reach the HMI server. Because of this, you can detect alarm conditions faster and give workers more accurate alarm information.
- Improved Notifications
Modern HMI software takes advantage of the connected nature of modern operations. This means workers don’t need to be standing in front of screens anymore to know when alarms happen. Instead, they can be remotely notified by email, text message or smartphone alerts.The software also allows you to escalate alarm notifications to others, such as when a worker isn’t responding to an alarm or when conditions worsen.
For example, if a tank exceeds its acceptable threshold of 80 degrees, operators can be notified with both a traditional HMI alert and a text message to their smartphones. If that temperature increases to an urgent threshold of 90 degrees, text messages can also be sent to the plant manager and maintenance team. And if the temperature reaches a critical threshold of 100 degrees, the emergency monitoring system can be triggered to begin a plant evacuation.
- Faster Issue Resolutions
When something goes wrong in production, the last thing you want to do is spend time digging for clues into what happened.Modern HMI software can use associated tags to include process data with event information and alarm messages. So when an alarm is triggered, production personnel can automatically receive information that describes what the system’s operating environment looked like when the alarm occurred.
Smarter, Faster Alarm Response
The sooner workers are notified of HMI alarms, the more quickly they can respond to and recover from the production issues that can hurt your bottom line.