A Good Point of Departure for a Difficult Year
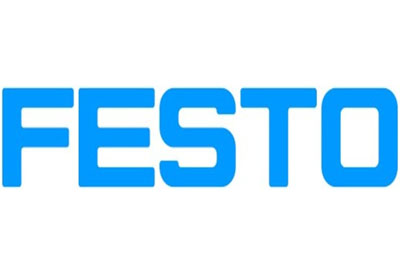
July 9, 2020
In the financial year 2019, the Festo Group extended its position in the market and in technology during the downturn and was able to maintain the number of its employees almost at the previous year’s level. Sales were just under the figure for the previous year. As a supplier to systemically relevant areas such as the food and packaging industries, medical technology and laboratory automation, Festo got off to a comparatively good start in the first quarter of 2020 and continues to supply its customers stably on a global scale. Along with measures to counter the crisis, the company is focusing on digitalisation, machine learning and AI. The global player in automation and technical education is concentrating on smart products and services in order to meet the great challenges in the machinery sector such as Industry 4.0, energy efficiency and climate-neutral production, lifelong training and individualised manufacturing.
The financial years 2019/2020
In the financial year 2019, the Festo Group further extended its position in the market and gained market shares in a difficult economic environment. Sales of €3.07 billion were achieved, slightly under the previous year’s figure (-3.7%). Around 21,000 employees worldwide were working for the company at the end of 2019.
“As a financially independent family-owned company, Festo is very solidly positioned and oriented to the future. During the downturn, we already adopted countermeasures at an early stage last year and secured our results. I am very happy that we were able to stabilise the number of our employees almost at the previous year’s level,” said the Chairman of the Management Board, Dipl.-Ing. Dr. h.c. Oliver Jung.
Festo initially managed to continue on its course of stability despite the Corona crisis. As a result, the company achieved good profitability and a positive cash flow in the first quarter of 2020. In the second quarter, the effects of the pandemic were clearly noticeable for Festo as well. “It is difficult for us to predict how the coming weeks and months will develop. Just like other companies, we will continue to implement counter measures, and adapt them very flexibly on a global and local scale. We are expecting catch-up effects for the second half of the year,” said Dr Oliver Jung.
Festo is systemically relevant in the crisis and is supplying customers globally to an increased extent in the areas of food, packaging, and pharmaceutical and medical technology.
“Our broad-based industrial footing helps us when some segments, such as automotive, are showing decline,” said Dr Oliver Jung. The Business Unit LifeTech registered a record increase. Festo is giving top priority to supplying automation technology components to manufacturers of medical and laboratory automation systems. At the moment, these are above all components used in respiratory ventilators and for in-vitro diagnostics.
The crisis is driving digital transformation
Digitalisation and Industry 4.0 are experiencing an enormous boost in the crisis. Today, Festo is already giving its customers comprehensive virtual support and is depicting the entire Digital Customer Journey with an extensive online offer. Added to this are digital learning offers from Festo Didactic.
The digital transformation is also at the focus of the new corporate strategy. For the innovation leader Festo, the core of this is its digitalisation strategy that is pushing in four directions: “Smart Products”, “Digital Business”, “Digital Enterprise” and “Digital Education”. “We will continue to strongly expand Digital Business. Artificial intelligence, software, and smart product and service worlds will boost our power of innovation,” Dr Oliver Jung explained.
Festo took over the Herford-based Resolto Informatik GmbH in Germany two years ago. Along with integration in Festo products, Resolto AI is now also coming much closer to developing software and Industry 4.0 value-added services in Festo Digital Business.
Shaping sustainable development
The further strategic orientation includes a climate strategy that aims for a 30% reduction of production-related CO2 emissions (Scope 1 and 2) by 2025. With energy-efficient, smart products and with consulting (Scope 3), Festo is also accompanying its customers along the road to climate-neutral production.
Employee training is another key factor for a sustainable transformation. For this purpose, Festo Didactic has developed its own broad-based, also digital, education offer to prepare future generations for the digital working worlds and for topics such as the energy turnaround, and is accompanying people in their professional lives with lifelong learning concepts.
“With our competence in automation and technical education, we are driving the industrial transformation forward. As a family-owned company we think in terms of generations, not quarters. We want to contribute to sustainable development of the environment, the economy and society,” Dr Oliver Jung concluded.