Digital and Visual Twins: FANUC’s Vision for the Future of Manufacturing
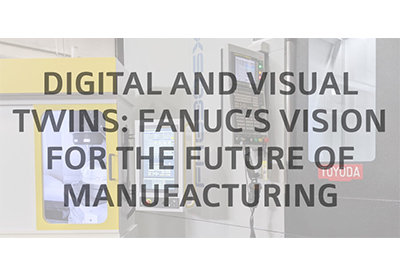
September 21, 2020
FANUC America recently unveiled its new visual twin demo at JTEKT Toyoda Americas Corporation’s Open House at their Arlington Heights, IL facility on Sept. 15-17, 2020.
A visual twin is a next-generation, high-resolution version of a digital twin, which is an exact software replica of a real CNC machine tool with a virtualized CNC. It connects to the controls and uses real physics to produce the authentic look, behavior and sounds of the actual machine tool cutting parts.
In the new visual twin demo, we are virtualizing the cutting of a robot head on a Toyoda FH630SX-i 5-axis machine tool designed for complex machining. This part requires more than 40 different processes and takes more than 16 hours to cut in the real world.
We collaborated with Toyoda to use the actual machine’s solid models and kinematics to produce the visual twin. We partnered with ModuleWorks to create the graphics and Mastercam to provide the CAM software.
The whole process can be set-up and proven out in the virtual world to improve the part and product quality. The twin enables the G-code program to be tested and the process simulated, showing a more realistic feel of the cutting. This is virtual commissioning, where new designs and concepts undergo evaluation BEFORE production, not after.
Virtual commissioning via digital twins offers many competitive advantages, like reduced manufacturing costs, less waste and greater flexibility. Machine tool builders and end-users alike can use digital twins to tweak the control code without taking the machine out of production. This helps to drive innovation while increasing productivity—all at a lower cost.
Digital twins are a crucial technology of Industry 4.0 because it transitions traditional analog processes to digital ones. FANUC, ModuleWorks, Mastercam and Toyoda are all working together to provide this end-to-end digitalization of the machine shop, from CAM to control—all to maximize process flow.