Machine Safety: A Comprehensive Approach to Identify, Assess and Control Safety Hazards
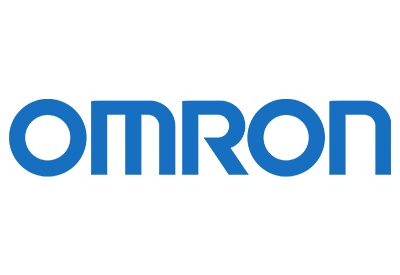
October 27, 2020
By Blake Marchand
Omron Automation is a company with safety ingrained in its DNA. In fact, the first product developed was an electronic timer for early X-ray machines designed to protect patients from excessive radiation exposure. Since 1933, that sense of social responsibility remains a core aspect of their culture.
However, the true value Omron brings extends further than products. With respect to machine safety, Omron is uniquely positioned as a trusted partner and solutions provider, offering a comprehensive portfolio ranging from product, training, and risk assessments to the design of safety solutions. This is where their social responsibility culture plays a big role. Prioritizing safety over product sales, results in a high-level of trust with their clients. And because they design and manufacture over 35,000 SKUs (Stock Keeping Units) for safety alone, they are deeply ingrained in the technology and standard development.
Mohammad El-Naji, Safety Sales Specialist for Omron, says that our primary focus is to ensure clients have a compliant solution that protects workers and optimizes production, and that does not always mean with Omron products. This approach establishes confidence with our clients that carry that into a trusting relationship that they foster with their customers. “We’re not just selling products, we’re selling a solution,” noted Mohammad El-Naji.
“Omron offers a comprehensive portfolio,” explained Dr. Todd Mason-Darnell, Safety Products and Services, Omron Americas, discussing what Omron offers from a safety perspective, “we are an authorized training partner with TUV Rheinland, we also have specific trainings on different regional standards. Moving beyond standards, we offer risk assessments. We have internal safety engineering teams that can design safety solutions and retrofits for existing equipment, as well as work with customers when they are designing new equipment. Then, finally, we have the capability in house to go out and retrofit safety onto customer’s existing equipment.”
Nearly everything is done in house. Which has an impact on their ability to ensure everything is undertaken at a high quality with high levels of efficiency, collaboration, and integration. When it comes to solutions, troubleshooting, and their products; there is not a question they can’t answer.
Their professionals, like El-Naji, sit on standard committees for CSA, RIA, ANSI and the various organizations relevant to the markets they serve around the world. They have 70 employees that sit on standards development committees and employ over 50 TUV certified engineers in the field. Including one of 33 certified TUV Rheinland Functional Safety experts around the world.
In Canada, they have two safety professionals that sit on 5 committees, Mohammad sits on three for CSA.
That commitment to the regulatory side of the industry is reflected in their product offerings.
“As an OEM for safety equipment we get pretty embedded in the safety standards and safety requirements, driven not only by the current rules and regulations, but also what’s coming,” said Mason-Darnell.
Omron designs over 90% of the safety products they sell, coming from their extensive safety R&D teams in Japan, California, and Europe. They are always in consultation with people in the standards community, so they know what’s coming out ahead of time.
They have a long-term philosophy when it comes to product development. They want to develop products with the future in mind. “We’re developing products and solutions that are going to be meeting the needs for years to come, rather than what’s happening this year.”
Their global reach is another asset for clients. If El-Naji is not familiar with a standard from regulatory organizations outside of Canada like NFPA or ANSI, he is able to lean on Omron’s safety experts in other regions.
“The great thing is we have a lot of experts around the world I can talk to,” he noted. If a partner is moving equipment to the U.S., for example, he can reach out to someone there for their professional opinion.
To that point, Mason-Darnell explained, “Right now, we’re doing consulting work with an OEM who is shipping a machine to Czech Republic. The company the OEM is working with has a global safety spec and internal safety requirements that the OEM has to meet, there are also machinery directives for Europe, as well as from Czech Republic – so, our safety engineers are able to help the OEM interpret the end-user’s specifications, as well as have familiarity with machine directives in Europe, and we can also reach out to one of our safety professionals in Czech Republic. So, in the end there are no surprises when the equipment is onsite.”
“There’s great collaboration among the whole safety team,” added El-Naji.
El-Naji provides an interesting perspective that illustrates Omron’s commitment to safety. He joined Omron a few months ago coming from a company that operates in a similar space.
“When I first joined, I was surprised by the amount of functional safety specialists on the team. It’s very comforting because I can have a conversation with them, and they understand my language. This translates to the products, as well. If you have people that talk about safety and understand safety, you know why the products are the way they are.”
“When you have functional safety experts, they know what differentiates between a safety product and a standard product and they can talk about it.”
“I truly feel with this company,” said El-Naji, “when it comes to safety, they take it unbelievably seriously and they understand it very, very well. And that translates onto the products and services.”
Looking ahead, Mason-Darnell, noted, “There’s a lot of discussion around collaborative robots and what collaborative robot safety will look like going forward in the next 5-10 years, within highly flexible manufacturing spaces.”
As robotics and collaborative robot (cobot) systems become more and more prevalent in the manufacturing landscape, the focus on safety in that space will only increase. Which is a trend tailored to Omron’s expertise as a leading provider of robotic solutions.
“What does safety need to look like in those types of situations? Where the manufacturing lines may be reconfigured multiple times in a shift and you may have an operator cell who is perhaps working with multiple collaborative robots,” he explained, “there could be a different item coming down the line every time. So, the buffer zones and the safety situation are going to have to evolve depending on the products that operator is working on at that time.”
Which is fundamentally different than the way safety is configured right now. Generally, safety systems are static configurations with specifically defined hazards and specifically designed safety zones.
As safety systems become more complex, manufacturers may not have the expertise in house to deal with their safety requirements. Particularly when it comes to robotics and cobots. With the importance safety has on operations and the increasing technological demands of the current industry landscape, manufacturers are leaning on companies like Omron that have a robust knowledge of products, solutions as well as global standards.
Go HERE for more information