HARTING Applied Technologies is “Toolmaker of The Year 2020”
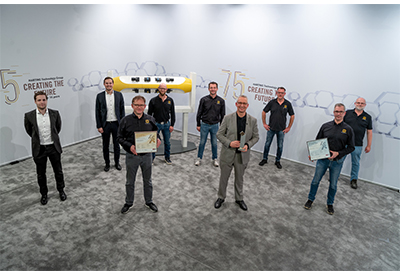
November 25, 2020
HARTING Applied Technologies GmbH has won the “Toolmaker of the Year 2020” competition, emerging as the overall winner in a top-flight field of participants with more than 200 companies. In addition to the overall victory, the HARTING subsidiary also took the award in the “In-house Toolmaker under 50 employees” category. The company had already won in this category in 2014, 2016 and 2018. The award is presented by the Fraunhofer Institute for Production Technology IPT and the Machine Tool Laboratory WZL of the RWTH.
In the jury’s opinion, the decisive factor in favour of HARTING Applied Technologies was the clearly defined strategy for each operating area, which included roadmaps with defined fields of action and goals, as well as the particularly high level of awareness of vision and strategy throughout the workforce. The high level of machine utilisation in all manufacturing technologies thanks to extensive automation, powerful machines and innovative solutions also played a positive role. The company has a complete system landscape in place ensuring high data consistency and relies on a colour system that provides information on tolerances, technologies and surface characteristics.
“I am very proud of the overall victory in this prestigious competition. The two awards can be credited to the entire team,” says Dr. Volker Franke, Managing Director of HARTING Applied Technologies.
HARTING Applied Technologies GmbH is an independent company within the HARTING Technology Group. In two independent sub-divisions, it develops, designs and manufactures injection moulding and die casting tools for aluminium and zinc, as well as assembly systems and special machines.
In the toolmaking area, the company’s 49 employees manufacture high-precision and productive tools based on single and multi-component technology. The range of products extends from relatively large-volume housing components for plastic and aluminium connectors to micro-injection moulded parts with shot weights of less than one gram and structural sizes of less than 100 micrometres, in connection with the highest demands on surface quality. In addition to the manufacture of injection moulds, the development of associated injection moulding processes for the production of metal-plastic composite components is a focal area of the company’s activities.
The process chain in the toolmaking shop at HARTING comprises in-house pre-development for new production processes and concepts, as well as comprehensive and consultation with customers at an early stage. The manufacture of tools includes engineering, design, production and assembly in an extensively equipped technical centre.
For more information, visit www.HARTING.com.