New Modular System Leads the Way for Modern Installation Solutions
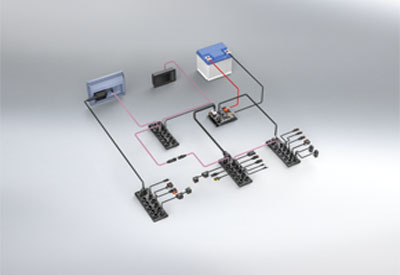
November 27, 2020
Here’s the dilemma, you consistently hit the same cable and wiring issue, the only solution you have uses existing products and you know the end result is far from ideal. But it’s all you have! This is a frustrating issue faced by many electrical engineers. Surely, there’s a better way, a better solution.
Data Panel GmbH, a company in the Murrelektronik Group, has risen to the challenge and now offers an electronic installation solution for mobile machinery that is modular, highly flexible and future-proof.
The market segment of mobile machines is still in its infancy when it comes to “rational installation technology”. Although cable harnesses and terminal boxes are the dominant technology, in recent years more and more electronic technologies have found their way into machines – and this has had a knock -on effects in terms of wiring effort for machine builders. In addition, manufacturers nowadays have more options in their product range to better cover market requirements. All this has meant that the cable harness and the terminal box solution are increasingly reaching their limits.
Depending on the type of machine, some manufacturers say that due to the weight, the cable harness can only be installed with several helping hands and in some cases, the support of an indoor crane is required. Another critical situation is as follows: when connecting many individual strands, it is difficult to ensure that each individual strand is tightened and leakproof. If even a single seal fails, moisture or an operating medium can penetrate right into the housing of the controller, sensor or actuator causing the machine to fail completely.
Simple, fast and error-free assembly
In March 2020, the Murrelektronik Group founded Data Panel GmbH with the aim of solving or eliminating the problems and weaknesses outlined above. Its portfolio includes high-quality, decentralized, electrotechnical installation solutions for mobile machinery. This modular system comprising of fieldbus modules, passive distributors and pre-assembled cables offers a highly coordinated, modular and pluggable system. Specifically manufactured for the mobile machines market, the new system has revolutionised wiring and cabling and makes it possible to economically realize smaller batch sizes.
The fully encapsulated CANopen fieldbus modules from the xtremeDB product family offer eight slots for inputs or outputs. The signal types – digital, analog, ratiometric, frequency/counter and encoder signals can be individually configured for inputs. DO (4A/10A), PWM/PWM(I) and PVG valve controls on the output side round off the signal range.
Thanks to the end-to-end DT-compatible connection technology, the module, which is made of a reinforced plastic housing material, can be used in machines in which the designer can use pre-assembled sheathed cables or, alternatively, use single wires for connection.
The use of passive distributors creates the intermediate step from parallel wiring harness or terminal box wiring to the plugged fieldbus technology and also offers the possibility of bringing “on-board” inputs and outputs on the controller into the field simply and cost-effectively. In contrast to the cable harness, the plug-in system allows subsequent expansions or adaptations of the machine electronics without any problems.
With the complete xtremeDB product family, machine setup and commissioning can be carried out without expert knowledge using Murrelektronik’s pre-assembled and tested connection cables based on DT plug-in technology. When these connecting cables are used, the active and passive modules meet the requirements of IP68, IP66K, and IP69K. Alternatively, the cable can be assembled with DT or compatible connectors. The modular system of pre-assembled and tested components and the extensive range of accessories ensure a high degree of independence when wiring sensors and actuators. Another advantage of xtremeDB is the independence from cable manufacturers. Due to the easy handling of the components of the new installation system modular system, machine builders are not dependent on their capacity resources.
In the terminal box, the change of technology results in a significant space saving, since additional input and output modules and the potential terminal level are replaced in addition to the mobile control. This means that signals are no longer wired individually and laboriously “in the box”, but simply and efficiently installed decentrally in the machine – the terminal box can thus be smaller or, in the ideal case, even completely omitted. Cable glands and thus potential weak points are no longer required. The installation time is thus reduced to a minimum.
In the event of service, the connecting cables can be quickly and easily replaced on site or repaired with self-attachable plugs.