What Are the Requirements of Lockout/Tagout?
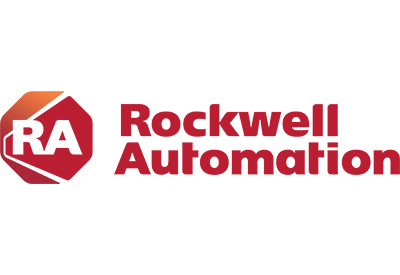
December 7, 2020
By Bill Leger, Safety Project Engineer, Rockwell Automation
When considering compliance with lockout/tagout regulation, many people think that locking out the hazardous energy sources is all that it takes. In reality, there is much more to it than just creating a safe work environment during servicing. There are five components of a proper energy control program that will help your organization remain OSHA-compliant and maintain employee safety.
1. Corporate Policy
A corporate policy is vital to define the scope and requirements of your lockout/tagout program. It explains when lockout is necessary, who is authorized to perform the work, how to safely lock out equipment, and how to address special circumstances. Every aspect of the program and what everyone’s responsibility is when it comes to lockout/tagout should be outlined in the company policy.
2. Employee Training
To be sure that work is safely performed, employees who will be involved in servicing must be trained to understand and recognize the dangers associated with lockout/tagout. A knowledgeable, experienced trainer can teach employees how to isolate energy sources properly and apply the correct lockout devices. Proper shutdown and restore techniques should be taught, as well as when to use lockout/tagout procedures. The training should also cover special circumstances such as group lockout to verify that employees understand the corporate policy. Affected employees–those not performing lockout/tagout–will also need awareness training on the purpose and use of lockout/tagout.
3. Documented Lockout/Tagout Procedures
Machine-specific lockout/tagout procedures should be developed for each machine at your facility. These procedures must list the energy sources to be isolated during the lockout, residual energy sources that must be released, and any additional warnings or hazards. Disconnect types, locations, and magnitudes must be part of the procedures. You’ll want to include steps to shut down and lock out the equipment as well as steps to restore the system to normal operations. Finally, methods to verify that the equipment is in a neutral state are necessary to help protect worker safety during lockout.
4. Proper Hardware and Devices
To lock out the equipment, specific locks, tags, and devices are needed. They must withstand the environment and not be easily removed without excessive force. All energy sources that accept a padlock must use one. Valves and disconnects that don’t accept a padlock will need specific hardware such as cable or breaker lockout devices to keep the disconnect in the off position. These devices must be properly applied and locked out. Locks and devices must identify the individual performing work, along with additional information about the purpose and duration of the lockout. A durable informational tag can also be applied to the isolation point, identifying the authorized employees.
5. Annual Inspection
At least once per year, your energy control program must be inspected to identify any errors that may exist. Procedures must be reviewed to verify they accurately reflect the equipment and needs of the workers. Authorized employees also must be observed performing lockout/tagout to confirm they know and follow the procedure and can preserve a safe work environment while performing maintenance.
OSHA established these five components to ensure that companies are providing their employees with everything they need to safely service potentially dangerous machinery. The corporate policy sets the company’s expectations for their employees. Employee training ensures communication of the company’s expectations. Documented LOTO procedures provide detailed instructions for employees to follow while servicing. Keeping good stock of the proper devices ensures that authorized employees have what they need to protect themselves. Finally, the annual inspection helps employers keep a pulse on the program to ensure the program is kept up to date.
Rockwell Automation has lockout/tagout specialists who have helped hundreds of companies reach compliance with their lockout/tagout programs.