Towards a Diesel-Free Mine
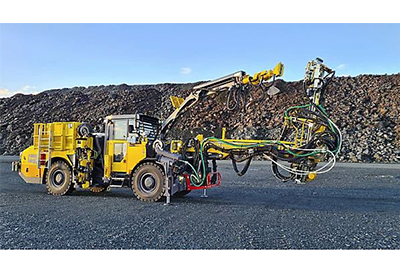
December 8, 2020
The European Union-funded SIMS project and the related field tests of Epiroc’s battery-powered mining machines turned the eyes of the entire mining world to Kittilä. Now, the mine’s first own battery-powered rigs, two Boltec E Battery bolting units, have started in production.
It takes courage to be at the forefront of development, but the benefits to be achieved – an improved working environment and a reduced carbon footprint – are considered worthy at the Kittilä mine.
“As a whole industry we should strive towards zero emissions, and we are doing a lot for this here in Kittilä. The benefits with the battery equipment are quite obvious. First of all, of course, the reduction of fossil fuels and the reduction of our carbon footprint. But also the major advancements we have made on safety and health of employees,” says Tommi Kankkunen, General Manager of the Kittilä mine.
SIMS project
Testing of Epiroc’s new generation battery-powered mining equipment in a real mining environment was a part of the European Union-funded SIMS project. The project took place during 2017–2020, with the objective of creating smart and environmentally friendly systems for the mining industry. The project involved several mining companies, equipment and system manufacturers, as well as universities. The test environment for Epiroc’s battery-operated mining equipment was provided by Agnico Eagle Finland’s Kittilä mine.
“SIMS was great” says André Van Wageningen, Manager of Technology & Development at the Kittilä mine. “It helped us to collaborate with universities and other companies in the mining industry to expand our knowledge and develop new technologies.”
Battery-driven rock bolting rigs
After the tests, the mine has now purchased its first battery-powered rigs. According to the investment plan, Boltec E rock bolting rigs were selected as the first battery-powered units. The important drivers behind the decision were sustainability of the rigs and the opportunity to create a better work environment.
The first bolting rig arrived at the Kittilä mine early November and had been in production for two days at the time of the interview. Another similar bolting unit joined the club a couple of weeks later. According to Jari Kolehmainen, Production Manager, the first messages are very positive: “The performance of the machines is at least at the same level as that of diesel machines. Productivity has improved with the development of equipment.”
Battery-powered machines have many advantages
The entire staff of the Kittilä mine is looking forward to taking the new technology forward. Operators’ well-being at work has clearly improved as exhaust fumes, heat, vibration and noise have decreased. For example, a rock bolting rig is moved several times during a shift, and in the past it has always meant starting diesel engines and blowing up an exhaust cloud.
In terms of maintenance, the equipment lacks a large component (diesel engine), and as a result, oil and filter changes are omitted. Also for fire safety, battery-powered machines marks a step forward in the absence of hot surfaces of the diesel engine and moving oils.
Air quality improves piece by piece when diesel engine equipment is replaced by battery-powered equipment.
“Especially on the loading and haulage side, the change in air quality is clear,” says Jari Kolehmainen. “In the future, we want to reduce our carbon footprint and move towards zero-emission technology, as well as move forward in well-being at work. The SIMS project showed that battery technology has made great leaps forward”. According to Jari Kolehmainen, a diesel-free mine sounds very possible even in the near future.
Changes to mine infrastructure
The mine’s infrastructure has been affected by battery-powered equipment in such a way that the design of its electricity network takes the electrification of the entire equipment into account. Battery-powered machines also require a battery replacement location. Preparing for battery-powered machines is fairly simple and besides above, no other special requirements were needed.
Agnico Eagle Finland’s Kittilä mine wants to profile itself also towards the introduction of other new technologies in addition to battery-powered equipment. A remote control room has been completed for the mining office, from which several machines are controlled simultaneously. Since the beginning of October, it has been a permanent turn for two people to operate mining machines remotely. The mine firmly believes that investing in new technologies will bring long-term benefits.
The Kittilä mine has also aroused great interest internationally, and a long list of requests for visits awaits a post-pandemic period. The Kittilä mine is positive about the collaboration and is open about its experiences. The introduction of new technologies requires transparency and cooperation.
“The mining industry needs pioneers like Agnico Eagle to help drive improvements that will benefit the industry globally,” concludes Peter Bray, Global Product Manager at Epiroc’s Underground division.