The Art of Mobilization: Ensuring the Continuity of Industrial Production
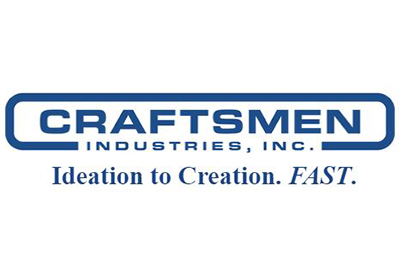
December 17, 2020
Industrial manufacturers require production reliability and continuity. However, a wide range of conditions can make this challenging – from unexpected emergencies, power grid failures and blackouts to partial plant shutdowns for maintenance, upgrade, replacement, or expansion.
So, when uninterrupted power, power storage, water pumping, filtration, treatment etc. is necessary for production, safety, or regulatory compliance, a growing number of manufacturers are looking to mobile trailer and containerized units. These modular units can complement, supplement, or replace such functions on a temporary or permanent basis. Notably, the units can be customized to meet specific needs and delivered in a fraction of the time and cost that it usually takes to build on-site or off-site.
With a collaborative approach and flexible design options, such modular systems can quickly be taken from concept to turnkey asset. When necessary, supplemental support solutions can even include mobile offices, command and control centers and foodservice kitchens. Organizations with multiple sites can transport the mobile units wherever needed at any time.
“Custom built trailers can be configured to act as rapidly deployable mobile units to provide remote power generation and distribution, water treatment, and battery energy storage systems (BESSs). The units can be designed to a variety of specifications and sizes with high output capabilities, sound mitigation, and minimal environmental impact,” says Mark Steele, CEO of St. Charles, MO-based Craftsmen Industries, a rapid designer and fabricator of mobile, containerized units for temporary or permanent use.
Since 1982, Craftsmen has fabricated mobile units for organizations such as Verizon, AmerenUE, Dell, and the U.S. Department of Veterans Affairs along with dozens of others
Overcoming Conventional Limitations
Traditionally, adding capacity to an existing industrial facility has been constrained by the limited amount of available space near production or processing lines.
Even when space was available outside, constructing structures outdoors to house and protect equipment needed for functions such as power, pumping, and water treatment is expensive, slow, and usually not feasible if the need is temporary.
While utilizing industrial equipment in mobile trailers has been an option, the solutions are rarely tailored to specific applications. Additionally, the lead time to receive a mobile solution can be excessive. This is a concern when the mobile units are built by firms that outsource much of the work to off-site subcontractors, each with their own production lead-time constraints and potential bottlenecks.
Building supplemental systems and delivering them to remote locations can have significant schedule and cost benefits. This is true where locations may have limited access to local skilled labor or where getting labor to the installation site. This is also beneficial when a schedule requires that many systems be installed in parallel by allowing subsystems to be built and delivered ahead of schedule.
Fortunately, more nimble, vertically integrated design and fabrication firms that can scale up for larger projects are now meeting the need for fast, flexible, collaborative construction of mobile assets. This ensures continuous industrial production capacity, even on short notice.
“Manufacturers may not always have much advance notice when they realize that supplemental or replacement power, water, or energy storage is required due to emergencies or unplanned repairs. So, expediting delivery and tailoring it to their process is often critical,” says Steele.
To speed mobile unit delivery and customization when it is necessary, Steele recommends that manufacturers work with a firm that offer in-house design, engineering, and fabrication capacity. This can cut traditional delivery time in half. In practice, this means that a partially customized mobile unit in a trailer or container can be received in about 12 weeks versus an industry typical 24 weeks, or a fully customized unit in about 20 weeks versus over a year elsewhere in the industry, if available.
Also important is working with a firm that is not only an integrator but also a fabricator with full engineering capabilities. This helps to resolve any issues that can occur at the drawing board as well as any difficulties that occur on the fly, according to Steele,
whose firm is ISO 9001:2015 certified and fabricates with a wide variety of materials including carbon steel, stainless steel, aluminum and alloys.
“To avoid delays and other issues down the road, I would also advise working with a firm that allows the design and fabrication teams to directly interact and communicate on the shop floor on a routine, preferably daily basis. This can safeguard against misunderstandings that could otherwise take the project off track,” says Steele.
Because circumstances can vary and change, Steele says that flexibility and collaboration should also be emphasized.
“Sometimes the manufacturer will provide the equipment and we will integrate it into the mobile unit. At times, they will specify and we will source it. Other times, we might design a portion of the project or most of it,” he says.
For more complex projects, however, it is important that the units are designed to be easily connected.
“The modular units are like Lego blocks that can be combined to optimize function in a minimal spatial footprint. If you have a generator unit, a power storage unit, a pump unit, and a filtration unit, you could link them all together wherever needed,” says Steele.
When necessary, additional mobile units designed for support purposes are required. For centralized control, a mobile command center can be utilized. This eases information flow and distribution through data, voice, and video through the center.
For example, with the use of mobile assets AmerenUE, an electric and natural gas utility provider to approximately 1.2 million Missouri customers, developed a creative way to enhance its effectiveness while responding to system power outages when major storms occur.
AmerenUE relied on Craftsmen to build two mobile command center trailers to improve its coordination and communication with field personnel during restoration efforts. Both command centers are 53-foot single drop trailers with custom modifications. The trailers are self-sustaining dispatch offices equipped with a communications room, custom antenna housing, conference room, field commander’s office, six work stations, satellite dish and 30- kilowatt generator.
The mobile assets provider also printed and “skinned” the trailers with a dramatic photograph of line workers on poles and the message “Help is on the way.” The trailers stay at an AmerenUE operating center in west St. Louis County until the units are dispatched. This occurs during incidents requiring the restoration of a large number of customers, when a communications center needs to be close to the action.
According to Steele, almost any requirement can be supplied as a mobilized solution. Mobile office trailers and training vehicles can also be used as temporary onsite work locations with specific seating, technology, restroom, and kitchen facilities available. If space is at a premium, single and double expandable trailer units can be designed with hydraulic bump-outs so that up to 980 sq. ft. of space is available.
In the marketplace, manufacturers have long been subject to excessive production downtime due to power failures and other unexpected occurrences.
With the availability of rapidly deployable, customizable mobile equipment trailers and containers, manufacturers today have a ready means to ensure reliable production despite emergencies like blackouts as well as necessary maintenance for upgrade, replacement, or expansion, which could otherwise lead to extended plant shutdowns.
For more information, visit www.craftsmenind.com.