A Closer Look at Safety Valves and the Value of Performance Level E
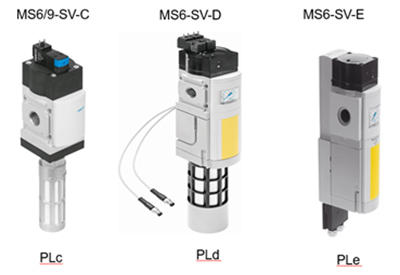
January 5, 2021
By Owen Hurst
Recently we had the chance to learn a little more about some of Festo’s output safety devices, with a focus primarily on the MS6-SV-E Safety Valve. Insight in this was provided from several Festo product specialists and a direct look at safety functions from Randy DeForge, Product Manager, Festo North America.
First and foremost a safe machine should be designed in a way that protects people and property amongst other things. Essentially the goal is to prevent physical damage of any type. The level of protection depends upon the level of risk. The focus on machine safety should always consider EN ISO 13849-1.
In his recent presentation at Pack Expo Randy went into detail about what is required to both determine the risks involved and how to ensure that you are utilizing the required level of safety for your machine.
First is determining what measures need to be taken to reduce risk. To determine the risk and necessary safety measures a risk evaluation is required. Once an assessment has been performed it is necessary to shift gears and focus on risk reduction. This could be undertaken at the design stage but if the risk cannot be reduced within the design than technical measures must be taken.
This is where safety functions come in to play such as safe exhausting, safety from unexpected start-up, or safe pressurization. There are several steps that need to be taken to determine safe functioning.
Performance level is the measure of the reliability of the safety function. These are divided through 5 levels, A-E. Level E is the highest and is required for operations with the highest level of risk. Some engineers also like to consider the SIL (Safety Integrity Level) The higher the SIL the more reliable the safety related system is. However, the SIL overlaps Performance Level and uses similar methodology to determine the requirement.
The next requirement is to determine how well the safety function needs to perform which will in turn identify the required Performance Level (PLr). For this it is necessary to determine severity or harm when someone would be exposed to a hazard, the potential frequency of that exposure and finally the possibility of avoiding the hazard. There are charts and scales available that allow you to consider these risks and determine the SIL or PLr to meet the safety needs for that machine.
It is prudent at this point to consider safety system structures. This is designated architecture defined as categories from B-4 with each safety function is designated with an input – logic – output device. Examples could be light curtain as an input, a safety PLC as a logic and a safety exhaust valve as an output. This is important when evaluating if the safety measures of the system meet the required Performance level.
- – Category B & Category 1 = Have a single channel architecture with no resistance to faults, meaning if it fails the system is no longer safe
- – Category 2 = Requires some frequent testing, used primarily for electrical systems
- – Category 3&4 = Have dual channel architecture, or redundant systems and differ only by the amount of diagnostics, or cross monitoring of the system in place
- – Category 4 = Has more diagnostics to monitor every channel of the system with a higher frequency
By assessing in this way, you can verify if the performance level of the safety functions put in place are equal or greater than the required performance level.
There are defined parameters that need to be determine for the safety components used in the safety system. You would need to know the diagnostics coverage, common cause failure values, design architecture and the mean time to dangerous failure calculations for each input, output, and logic component of the safety system. And as noted performance levels must always meet or exceed the analysis levels determined by the safety analysis.
With a general understanding of how to determine what performance level of safety component you need we can look more closely at your options Here we focus on the Festo MS series safety valves. A safety valve is used as an output device on a safety system that is designed to reliably reduce pressure quickly and then build it back up slowly. Typically, it is triggered by a safety device like a light curtain or e-stop.
Most safety valves require a dual channel signal, often one high one low, but they can be both high and both low. These devices are designed to ensure safe operation. These type safety valves always incorporate sensors to monitor the position of the spools. Those signals are then sent back to the monitoring device.
Typically, level D requires a smart controller that is sending signals to the device saying you need to turn off now, and did you? And then feedback is returned. Or it asks if the machine turned on and returns that feedback, but it requires an intelligent programmable safety relay or PLC and that logic is running the valve.
However, Performance Level E is a more self-contained and intelligent safety valve. It incorporates the engagement of the soft start functions via the soft start piston which is monitored by a third sensor. This valve has integrated electronics and self-testing diagnostics, status indication LED’s for power and error indication at the top of the unit, and all feedback sensors are fully integrated. All in all, Performance Level E offers an advancement in not just safety but intelligent monitoring and feedback that can perform without the use of external logic control.
Although it sees like an in depth and engaged process ensuring both equipment and safety for those working around machines is essential. Undertaking a risk assessment and ensuring you have a Performance level that meets or exceeds your requirements is critical to operating a safe machine and voiding injuries or costly damage.