Closing the IT/OT Gap: Adapting to Change Through Cloud Manufacturing
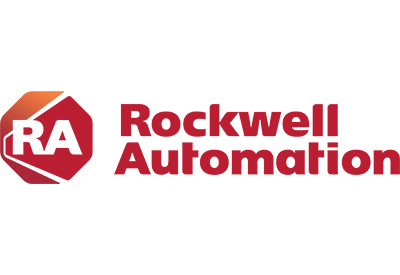
September 8, 2022
By Malte Dieckelmann, Regional Vice President – EMEA Software, Rockwell Automation
While digitalization has become a crucial goal across sectors, the application of digital solutions in manufacturing comes with added complications. Given the material nature of industrial process assets and equipment, the emphasis for manufacturing investment has still been predominantly hardware based, with upgrading plant machinery essential to meet production demand.
As companies adapt to new global circumstances around supply-chain management and closer integration with partners and customers, investment in IT is gaining greater focus. Cloud-based software is therefore on a growth trajectory within the manufacturing sector as more companies experience the efficiency and cost benefits of working in the cloud.
According to a recent industry report, for the first time ever, the average manufacturer will spend more on industrial software than on automation hardware. This marks an important turning point for the sector as the shift towards softwarization sets an irreversible course. To maximize the value of this investment, achieving convergence of OT and IT across the manufacturing lifecycle will be a key objective for businesses in the digital era.
The New Supply and Demand
Manufacturing has always been a supply-and-demand story. To stay competitive, it’s necessary that companies are attuned to shifts in the market and have the agility to increase or decrease production based on a feedback loop of sales data.
Now, with major economic and geopolitical shifts in full effect, the supply-demand equation is changing. On the supply side, manufacturers are dealing with challenges around the visibility, reliability and security of their supply chains. Not only are they seeking greater insight into the availability of materials, but also predictability around costs to determine price competitiveness moving forward.
Another notable change has been how manufacturers are engaging with their supply-side partners. As speed and resilience become key priorities, they’re seeking a more dynamic, data-driven relationship with OEMs. This ensures they can create an environment that can adapt to changes, predict problems and reduce the risk of downtime.
On the demand side, manufacturers are seeking to shift from B2B to a B2C-type relationship with their customers. Using digital technologies to establish a two-way interface, manufacturers can interact with end users in real time. This serves the purpose of gaining a better understanding of their needs, gaining feedback and adapting products to ensure satisfaction and differentiation. It also presents a fundamental change regarding their role in the supply chain, in effect becoming less transactional and more responsive to market information.
Gaining greater control over both sides of the supply-demand equation is difficult to achieve in a conventional hardware-led manufacturing. The approach for addressing this challenge brings with it an urgent need to implement connected, data-driven capabilities into the production environment.
Becoming Dynamic Through IT
The adoption of cloud-based software in manufacturing is helping to address the challenges and aspirations on each side of supply and demand. By taking standard manufacturing applications such as MES and ERP into the cloud, manufacturers are better positioned to plan, schedule and process according to their business goals.
This approach brings substantial benefits in areas such as supply-chain management, asset performance monitoring, and collaboration with stakeholders. By combining IT and OT, and leveraging the cloud, manufacturers can improve the performance of their environment, gaining greater predictability over both inputs and outputs. This facilitates the improvements in growth, cost and services that enable greater defensibility over their market position. They are also better placed to act on important considerations around sustainability and traceability, making them integral parts of their product’s story and differentiators in the minds of their end customers.
The transition towards digitalization also helps overcome longstanding issues around production siloes. By helping to connect geographically dispersed facilities and enable quicker decision-making, resources can be optimized. This includes the implementation of edge capabilities to increase the speed and value of insights coming from across their network of plants to enable greater coordination.
Converging OT and IT
Pursuing an approach led by the adoption of software and cloud is challenging for manufacturers that still have a functional divide between their IT and OT capabilities. To gain the benefits of digitalization, it’s important that your business builds a convergence of these functions at a foundational level. An expedient approach is to work with partners that already have relationships with cloud providers in place so that you can leverage their experience and capabilities.
For example, through our relationship with Plex, Rockwell Automation is helping manufacturers manage the convergence of OT and IT and, as a result, become more adaptable to changes in supply and demand. By offering Plex’s dedicated software solutions on Microsoft Azure, we are helping customers advance their cloud strategy and enable accelerated growth. As part of a cloud migration process, we work together to transition our customers’ essential applications, helping them to benefit from the cloud’s scalability while also reducing the need to invest in traditional hardware.
With decades of combined experience, we are well positioned to bring IT and plant-floor technology together. Our shared commitment to addressing the real problems manufacturing businesses face on the plant floor helps us to apply customized solutions that drive them to become more connected – and therefore more competitive – in their respective markets.
Learn more about cloud-based manufacturing at our ROKLive EMEA 2022 event, in Gothenburg, Sweden, on 24 – 27 October.