Four Questions to Ask Yourself When Getting Started With Robotics
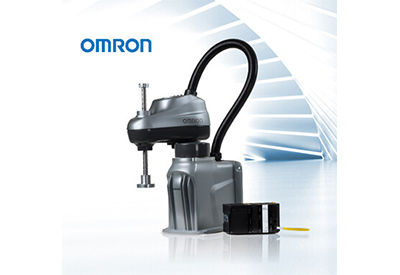
November 22, 2022
Many businesses of all sizes turn to robots for enhancing precision, speed, and consistency while minimizing expenses and downtime. However, many of them – particularly the smaller enterprises – are initially unsure of whether the payoff will be worth it.
Omrom provides a variety of robots to meet the specific needs of their customers. Whether you’re trying to automate highly repetetive tasks or shift some of the heavy lifting to machinery, they can offer to help you choose the right technology.
Before chatting with an Omron robotics expert, it always helps to consider the following questions about your plans, needs, and expectations.
What are the underlying problems you’re looking to solve?
The types of issues that robots can alleviate generally fall into three categories:
- 1. Concerns about employee safety
- 2. Concerns about precision and repeatability
- 3. Need for continuous productivity and uptime.
Robots can be great for eliminating manual tasks that are dangerous or could lead to repetitive stress injuries. Even tasks that don’t seem overtly hazardous, but that are highly repetitive, can cause problems for humans and are better performed by robots. For example, low-value-added tasks like palletizing are strenuous and repetitive and are prime targets for automation.
Tasks requiring extreme levels of accuracy and repeatability are also ripe for automating with robots. Some manual assembly processes require extensive training and have no room for error, leading to staffing issues and high scrap rates. Robots can outperform human levels of accuracy and repeatability, reducing waste and improving product quality.
If you’re looking for round-the-clock productivity, robots can keep working on low-level tasks throughout the day and night without needing to rest. Your team can focus on creative activities like designing new elements of the system and training the robots on new tasks when the need arises.
Do you need fixed industrial robots or collaborative robots (cobots)?
Industrial robots and collaborative robots both offer various benefits to be weighed against your target application. Traditional robots (such as articulated arms, parallel/delta robots, and SCARA robots) often boast best-in-class speed, payloads, accuracy, and repeatability.
Additionally, traditional robots often come with advanced software tools like full production line simulation and complex motion path capabilities (as seen in Omron’s ACE and Sysmac platforms). However, these robots require advanced engineering talent to program, integrate, and maintain. They also require safeguarding which increases a solution’s complexity, cost, and footprint.
Conversely, collaborative robots are designed to share workspaces with humans, and they’re easy to integrate and program. When coupled with a risk assessment, cobots can be installed with minimal safeguarding. However, their safety considerations necessitate limited payloads and speeds, so they’re generally outperformed in other specifications by industrial robots.
Cobots such as the Omron Collaborative Robot feature graphical programming interfaces, hand-guided programming options, and integrated vision to further simplify programming to the point where non-technical personnel can quickly learn to program and reconfigure cobots.
End-users should ask themselves several questions before purchasing a robot:
- – Would you benefit from easily reconfiguring a cobot in a high-mix/low-volume production scenario?
- – Can you achieve cycle times and production rates with cobots, or can that only be achieved with traditional robotics?
- – Is your target application safe enough to be collaborative, or would you be best served with higher performance industrial robots?
End-users should work with their robot providers and integrators to find a solution that best fits their application goals.
What are the simplest tasks you can automate today?
When implementing robots for the first time, it can help to start small. Even handing over some of the most menial tasks to a robot can make a tremendous difference in your facility’s productivity and in the satisfaction of your employees. In the case of cobots, the reduced safeguarding requirements may also eliminate the need to change existing workspace layouts.
Machine tending and pick-and-place applications are some starting examples of simple tasks for robots. These tasks are extremely repetitive, low value-add, and can sometimes result in injury. Given the simplicity of these tasks, robots such as the Omron Collaborative Robot may be best suited given its ease-of-use and integrated vision, which reduce implementation time.