Cobot Palletizers Evolve with Longer Reach, Heavier Payloads and Easy Interfaces
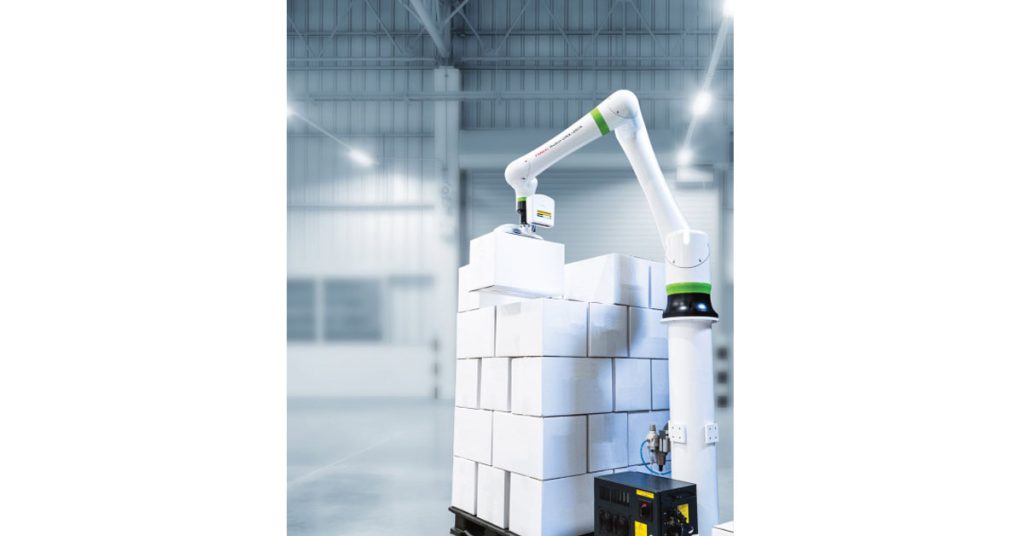
February 28, 2024
Robotic palletizing has been a game changer in packaging lines and warehouses for decades, but some considered automation not an option over concerns like space limitations and lack of robotic programming expertise. Collaborative robots have been opening up new automation avenues in many applications, but it wasn’t until higher-payload and longer-reach cobots, like FANUC’s CRX-25iA and CR-35iB, that are now causing many to reconsider automating palletizing to boost efficiency and productivity.
Read on to see how FANUC cobots with their new capabilities can help more businesses achieve their productivity goals.
Cobot Palletizing for a Smaller Footprint
According to a 2022 report from PMMI – The Association for Packaging and Processing Technologies, entitled “Robots and Cobots An Automated Future,” the percentage of cobots used in packaging automation is expected to grow from 27 percent to 57 percent by 2027. One of the main reasons for this growth is the flexibility and adaptability of cobots. Years ago, automating palletizing required a big footprint and a fixed application. Cobots have changed those restrictions, making automated palletizing a viable option for much smaller spaces as well as operations that might need to change their palletizing area.
FANUC’s CRX-25iA cobot has an enhanced 30kg payload capacity and long 1,889 mm reach, making it perfect for palletizing applications. If a higher payload capacity is needed, FANUC’s CR-35iB is the industry’s strongest collaborative robot featuring a 50kg payload capacity, a large work envelope and a small installation footprint, which works well in tight spaces.
Cobot Palletizing for Boosting Productivity and Worker Safety
With the labor shortage, companies from all industries across the U.S. are struggling with finding workers. This can lead to shutdown lines and unfulfilled manufacturing orders. Even if operations are staffed, having people repeatedly lift heavy boxes or other products all day can put them at risk for workplace injuries. Cobots are excellent alternatives for these palletizing applications. FANUC’s CRX product line excels with flexibility due to the 120 V power requirements and lightweight, which allows the cobots to be mounted to a portable platform. This enables manufacturers to move the automation between lines as needed.
With advances in FANUC’s sensor technology, the CRX-25iA and CR-35iB can be equipped with 3DV iRVision. This enables the cobots to locate and pick products on a pallet and place them onto another pallet or a platform part of an Automated Storage & Retrieval System (ASRS). Using information from the sensors, cobots can adjust their positions on the fly when the pallet location shifts.
This feature gives the cobots tremendous flexibility with the ability to handle one or more units at a time according to the pallet configuration. Additionally, cobots can form multiple layers on a pallet after picking the products. Cobot palletizing solutions can easily accommodate these different pallet patterns and handle multiple infeeds of different SKUs on the same line.
Finally, cobot palletizers are safe to work alongside people. With the proper safety assessment, cobots don’t require industrial fencing around their workspace. Cobots’ sensors can detect a person in their line of operation and stop their movement; this ability enables them to be placed in proximity to people.
Simplifying Cobot Programming
In the past, robotic programming was potentially a big hurdle to adopting automation for those that had no expertise or personnel to handle the task. However, FANUC cobots’ intuitive hand guidance and easy-to-use Tablet TP programming make it a snap for even those with no prior robot experience.
The cobots do not require special programming or complex languages. Operators simply program through the hand guidance option by leading the cobot through paths to teach a new task. They can also use the FANUC Tablet TP with drag-and-drop user interface to easily program the cobot as well.
Easy Pallet Building with Cobots
Building custom pallets has never been easier with FANUC’s PalletTool software. Once product dimensions are entered, PalletTool provides a list of possible pallet patterns as well as the space efficiency for each pattern.
When the pallet pattern is selected, all information about the pattern, including the product weight, total number of layers, pallet/infeed retreat, approach distances, and gripper information, are saved within the unit load created. This enables the operator to easily switch between products either at startup or while the system is already running just by changing the current unit load.
Operators can also create and modify unit loads directly from the Tablet TP with FANUC’s PalletTool 3 software using the newly updated user interface. This unlocks the ability to quickly modify systems on the floor without needing a computer.
Additionally, FANUC’s PalletPRO simulation software can be used to completely build and prove out a palletizing application on a PC. PalletPRO can create a complete work cell layout, including infeed and pallet stations, slip sheet and pallet dispensers. Hundreds of unit load pallet configurations can be created and visualized in 3D using PalletPRO’s built-in library of industry standard patterns. The data created in PalletPRO can be downloaded to a FANUC controller containing PalletTool software.
Cobots the New Palletizing Game Changer
Cobots, which were once thought for only low-payload applications such as pick-and-place and material handling, are now a viable tool in the packaging and production line. Even for operations that are working in tight spaces or limited resources, the ability of cobots to be deployed in a variety of environments is bringing all the benefits of automation to businesses that never thought it was possible.