Proax: Prevent Costly Downtime – The Critical Importance of Removing Water from Your Factory Air
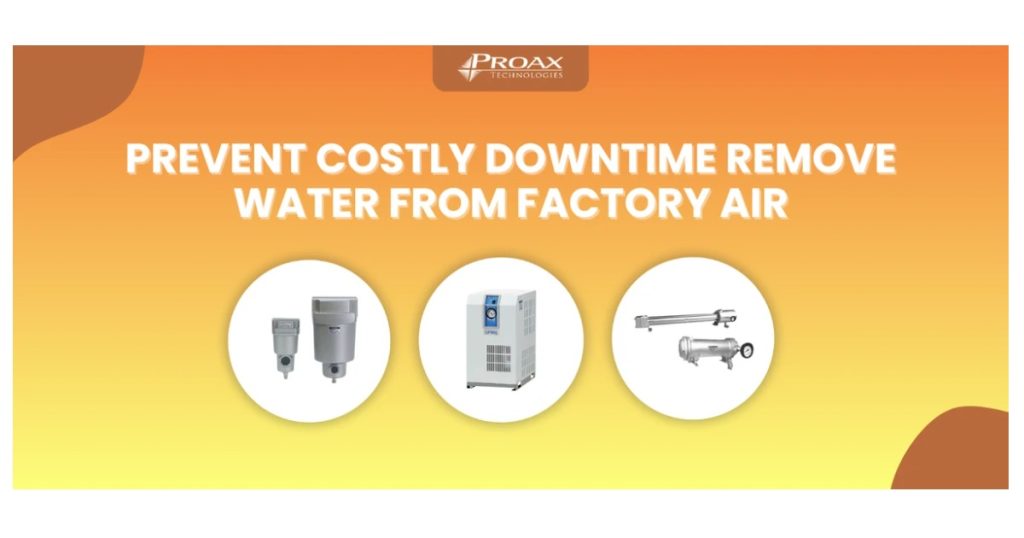
April 1, 2025
Proax Highlights the Importance of Preventing Moisture Accumulation in Your Factory Air
At Proax, they understand that unexpected downtime can devastate your production schedule and bottom line. As a reliable distributor of SMC pneumatic solutions, they have seen firsthand how one often-overlooked culprit—water in compressed air systems—can silently undermine your operation’s efficiency.
The Hidden Threat in Your Air Lines
While many manufacturers focus on removing oil and particulate contaminants through standard filtration, water vapor presents a more insidious challenge. A standard 100 hp compressor operating in typical conditions (86°F, 80% relative humidity, 100 psi) can produce a staggering 30 gallons of condensate during a single eight-hour shift.
This moisture doesn’t just disappear—it travels through your system causing:
- Corrosion and rust in pipes and components
- Scale formation that breaks loose and blocks air passageways
- Increased pressure drop reducing overall system performance
- Premature wear of pneumatic equipment
The Real-World Impact on Your Equipment
Water infiltration affects virtually every pneumatic component in your facility:
- Pneumatic cylinders lose their pre-lubrication, corrode, and respond slower
- Solenoid valves develop stiffened rubber seals that are prone to rupture and leakage
- Instrumentation can malfunction with even minimal moisture exposure
- Air-powered tools become prone to sticking, jamming, and reduced efficiency
Product Quality at Risk
Beyond equipment damage, moisture in your compressed air can directly impact your products:
- Spray painting operations suffer from color inconsistency and poor finish quality
- Industrial ink-jet printing experiences reduced adherence and quality issues
- Blow molding processes face altered viscosity and material consistency
- Packaging operations encounter reduced adhesiveness in gluing and taping
- Pharmaceutical and food processing risk contamination and compromised product integrity
The Proax Solution: SMC’s Comprehensive Moisture Management
As SMC’s elite distributor, Proax offers a strategic, multi-layered approach to moisture control:
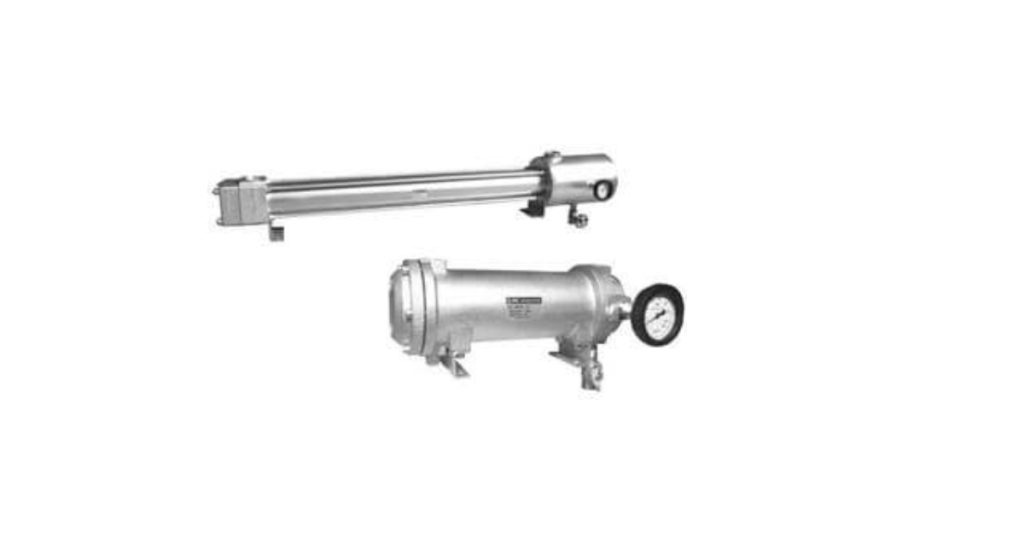
1. Aftercoolers: The First Line of Defense
Compressed air exits your compressor at temperatures up to 300°F—far too hot for industrial applications. By implementing properly sized aftercoolers, you can cool this air to near room temperature, removing 70-80% of excess water vapor in the process.
2. Strategic Drip Leg Installation
Proax’s pneumatic specialists can help you design and implement an effective network of drip legs throughout your compressed air system. These vertical pipes, installed at air drop lines below horizontal headers, utilize the principle of adiabatic expansion to condense water vapor into liquid that can be easily drained away.
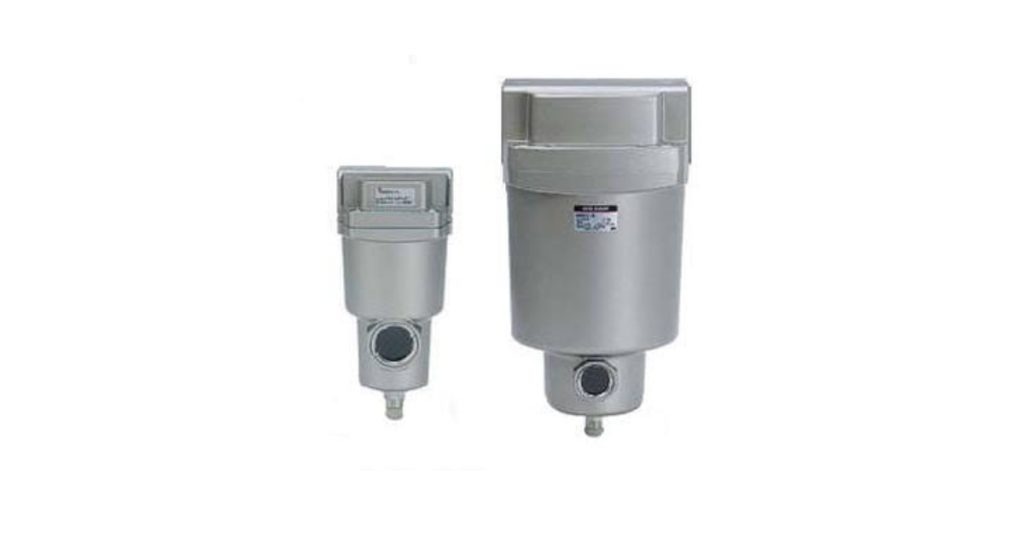
3. High-Efficiency Water Separators
For applications requiring enhanced moisture protection, Proax recommends SMC’s AMG Series water separators. These remarkable units:
- Remove water droplets with up to 99% efficiency
- Utilize a special resin filter technology to trap moisture
- Require no electrical power
- Can be installed as standalone units or integrated into modular air prep systems
- Offer simple installation and minimal maintenance requirements
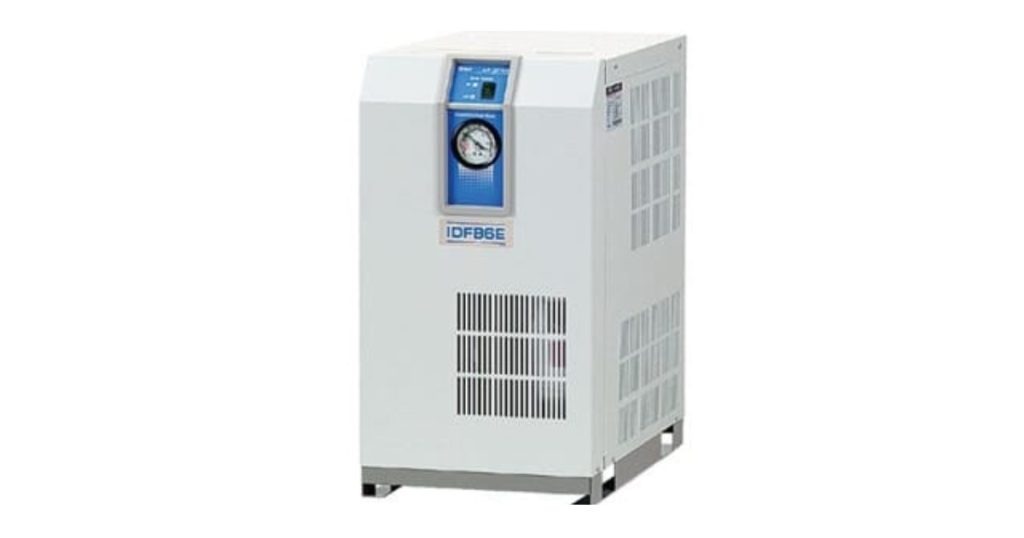
4. Advanced Drying Technologies
For applications requiring even lower dew points, Proax’s team can help you select and implement the right refrigerated air dryer or membrane air dryers for your specific needs.
The Proax Advantage
When you partner with Proax for your compressed air quality management, you benefit from:
- Decades of pneumatic system expertise
- Direct access to SMC’s industry-leading product lineup
- Customized solutions designed for your specific application
- Ongoing technical support and maintenance recommendations
- A commitment to maximizing your system’s efficiency and reliability
Take Action Now
Don’t wait for moisture-related failures to impact your operation. Contact Proax today for a comprehensive assessment of your compressed air system and tailored recommendations to eliminate moisture-related risks.
Their pneumatic specialists understand that every facility is unique and are ready to help you implement the right combination of aftercoolers, drip legs, main line filters, and air dryers to keep your system running at peak performance.