Digital Oilfield Operations Improve with Intelligent Artificial Lift System
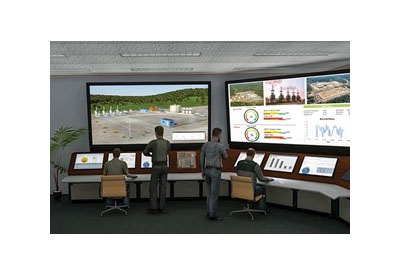
November 16, 2017
Oil and gas producers have been feeling the pressure in this down market to get the most from their existing assets and wellheads, as efficiently and cost-effectively as possible.
Fortunately, new technologies and capabilities that have been made available through digital oilfield innovation provide the means to effectively squeeze every bit of value from assets. A combination of low-cost sensors, intelligent assets and information tools allow oil and gas producers to gather more data, and have better control of their artificial lift systems.
These intelligent artificial lift systems can help producers realize three primary business benefits in their wellhead applications:
- Better visibility into operations
- Optimized production and asset performance
- Reduced operating costs
BETTER OPERATIONAL VISIBILITY
Large, multinational oil and gas producers often use downhole sensor systems to monitor underground pressure and temperature. However, many mid- and small-sized producers don’t have the luxury of using these systems, which have high upfront costs and long-term maintenance requirements.
When downhole sensor systems aren’t an option, virtual flowmeters (VFM) provide an economical alternative for understanding underground conditions. VFMs calculate the three-phase flow of water, oil and gas at the wellhead, and provide well analysis for performance improvement. They can calculate the data at either the wellhead site or at the control-system level.
VFMs do require some upfront calibration, but they’re also a fraction of the cost of downhole sensors, and can produce data of similar accuracy. In fact, one lab test that Rockwell Automation conducted for a major oil producer found the VFMs delivered more than 90% data accuracy compared to actual well-test data.
Another attractive aspect of VFMs is scalability. This means that the flowmeters can be deployed across multiple lift methods—from highly-productive multi-well pads, to low-producing wells.
OPTIMIZED PRODUCTION
For all of the value that VFMs offer, in truth, they are only valuable if an operator can put the data that is produced to good use. Once an oil and gas producer collects VFM data, they must be able to analyze it, and act on it, to improve operations.
Business intelligence software integrates data not only from VFMs, but also from all other inputs across an oil field. This creates a single information management and decision support system that can aid all aspects of production. Analytics software provides the means to turn raw data that has been collected into production intelligence.
With these software tools in place, oil and gas producers can tap into the power of their data to optimize their operations. For example VFM data can:
- Provide insights into underground conditions, which can be used to drive decisions about reducing bottom-hole pressure or keeping it constant.
- Be compared against well-test data. This can help verify well-test data, as well as validate planning and production allocation. What’s more, users can improve utilization of test separators by refining and prioritizing test schedules for each well.
- Identify underperforming wells. Once such wells are identified, operators can then quickly take any necessary corrective actions to limit production interruptions and deferments, and ultimately stay on track with their production targets.
- Collect information on system components from different vendors over time. This data can be used to better predict when components, such as a rod, might break. Also, it can improve equipment and supply logistics for maintenance, helping companies be more proactive in getting ahead of downtime issues.
REDUCED OPERATING COSTS
Intelligent artificial lift systems can help bring down production costs in multiple ways. For example, energy consumption is often overlooked in oil and gas production, which is surprising, given that it’s a significant operational expense.
Advanced artificial lifts primarily run on electricity, and intelligent systems can collect and analyze data on energy usage to help companies monitor their consumption. The artificial lifts also can be equipped with drives that can regenerate power and put power back on the grid, or they can use solar power to reduce electrical usage.
Variable speed control also provides another opportunity for cost savings. Traditional lift systems have no speed control. As a result, companies either run the systems until they break, or they turn the systems off, which can result in sand settling into the bottom-hole equipment and clogging it. Either way, oil and gas producers ultimately end up paying for these approaches in the form of costly repairs and unexpected production downtime. Modern artificial lift systems, however, can use variable speed control to help prevent plugging and maximize production efficiency.
Finally, intelligent artificial lift systems deliver improved insights into operations, which can help companies better manage their capital expenditures. For example, a company considering a well workover can use well data to determine if the potential future yield of a reservoir justifies use of alternative methods to enhance recovery.
TECHNOLOGY IN ACTION: ARC RESOURCES
One example of a successful intelligent artificial lift system application can be found in the vast oil reserves of western Canada. This is the region that ARC Resources calls home. The company is based in Calgary, Alta., and has assets located across Alberta and British Columbia for the exploration, development and production of conventional oil and natural gas.
In the Montney region of northeastern British Columbia, ARC Resources’ goal was to optimize the control systems for its large, multi-well natural gas production sites. The sites would soon need artificial lift to maintain production levels, but the control systems in place didn’t support the technology. Additionally, ARC Resources wanted to address the expansion and safety challenges that the existing systems presented.
SCALING UP ARTIFICIAL LIFT
Artificial lift was, by no means, a new concept for ARC Resources. The company’s smaller pads, of up to four wells, already used control systems that supported the use of artificial lift systems for optimizing production as wells depleted.
However, control systems used on the company’s pads of five or more wells didn’t support artificial lift. The control approach used on these larger pads consisted of multiple controllers that were hardwired together and used in conjunction with remote terminal units (RTUs) to handle the large amount of I/O required to run the entire well pad.
ARC Resources chose the ConnectedProduction well manager solution from Rockwell Automation to optimize its larger well pads. The solution includes an Allen-Bradley ControlLogix programmable automation controller (PAC) and FactoryTalk View HMI, which requires no custom coding. The PAC provides single-platform control for sites, with as many as 32 artificial lift wells, and contextualized production information to help operators troubleshoot issues and maintain optimal production levels, Fig. 2.
TRIAL RUN IN BRITISH COLUMBIA
The ConnectedProduction solution implementation began with a pilot project at an eight-well production site in British Columbia.
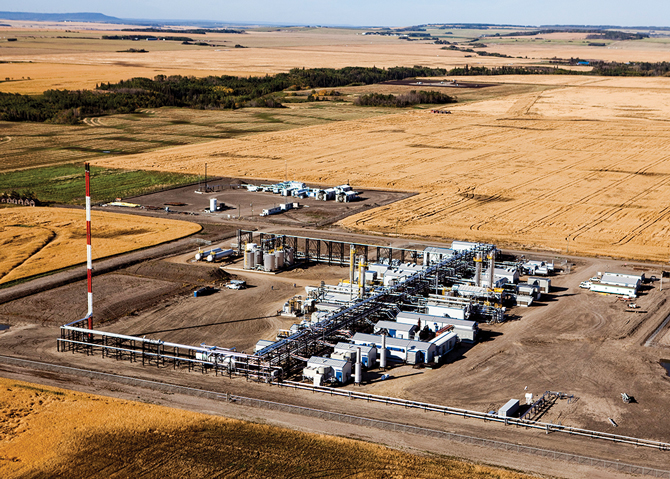
An early benefit discovered during installation was the solution’s add-on instructions, which helped the team save about two days of programming time. Additionally, integration with other vendor hardware at the site was easy, because the solution uses an open architecture.
Upon its implementation at the eight-well site, the system eliminated the need for multiple controllers and RTUs at the site. Instead, all well pad controls have been consolidated into a single control platform, Fig. 4. This not only simplified the control architecture, but also helped reduce the site’s hardware and software costs.
Additional cost savings were realized from the system because it can support a flow-measurement card within the control panel. This has allowed the site to eliminate its use of a separate flow-measurement computer and save tens of thousands of dollars as a result. The solution also allows the site to use artificial-lift systems, including on/off timers and plunger-lift systems, while also providing visibility into those systems.
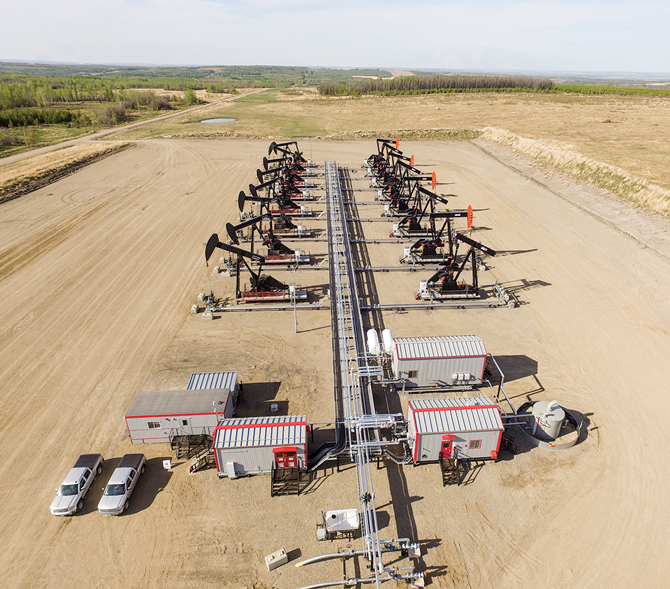
The system also is helping ARC Resources enhance safety at the site by reducing the risk of faults going undetected. If something goes wrong with the processor or if an I/O rack comes undone, for example, the control platform can fault to a safe state and shut down all processes.
Following the successes seen in the pilot project, ARC Resources is planning to extend the ConnectedProduction system to at least four more large multi-well pads that need assisted lift.
Monitoring downhole conditions and equipment performance in artificial lift systems is no longer a cost-prohibitive effort. The digital oilfield is bringing these insights to more oil and gas producers at a low cost with smart and connected artificial lift systems that can help monitor wellhead applications, optimize production, reduce equipment issues and bring down production costs.
Article by: Srikanth Mashetty, Rockwell Automation