Modules for Smart Chemical Plants
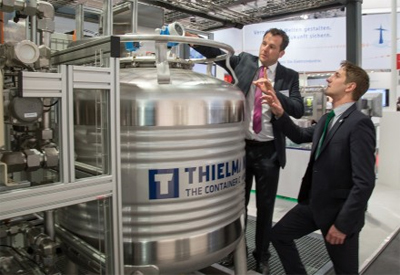
April 9, 2018
Digitization is paving the way to higher productivity in the process industry. At the special presentation “Process INDUSTRIE 4.0: The Age of Modular Production” in Hall 11 at HANNOVER MESSE 2018, visitors can learn how to increase productivity by greater use of intelligent automation and instrumentation, as well as by modularization. The presentation is sponsored by ZVEI , NAMUR and ProcessNet , an initiative developed by Dechema and VDI. Big-name suppliers such as ABB , Emerson , Endress+Hauser , Festo , HIMA , Phoenix Contact , Samson , Siemens , Wago and Yokogawa are contributing to the presentation. Also taking part are the Technical University of Dresden and the Helmut Schmidt University in Hamburg, as well as numerous major users such as BASF, Bayer, Clariant, Covestro, Evonik, INVITE, Lanxess and Merck from the chemical/pharmaceutical industry, in collaboration with module producers.
“Competitive advantages in the process industries depend increasingly on how effectively and efficiently the production operation is set up”, says Felix Seibl, head of the section “Instrumentation and Process Automation” within ZVEI , the association that represents Germany’s electrical and electronics industry. According to Seibl, plant operators want their production operations to be “more flexible, faster and cheaper that those of their competitors – and therefore superior.”
At the “Process INDUSTRIE 4.0” showcase in Hall 11, members of ZVEI and industrial users will be demonstrating – for the second time since its 2017 debut – how plant flexibility in the process industry can be greatly improved by the standardization of interfaces: through modularization of the entire process chain, and the increased use of intelligent, decentralized automation.
For a number of years now, NAMUR study groups and ZVEI research groups have been working together with Dechema and VDI on the specification of a vendor-neutral description language for modules. “We can use a so-called ‘Module Type Package’ (MTP) to link the individual modules and integrate them very quickly into a complete process. The result is a more efficient production chain”, explains Seibl. MTP plays a key role in the automation of a modular process plant. This approach, says Seibl – devolving control intelligence from the central process control system to the plant modules, addressing plant modules in a digital description language and ensuring there is a neutral interface between plant module and process control system – amounts to “a significant change in existing automation paradigms in the process industry”.
A demonstrator at HANNOVER MESSE 2017 for the human-machine interface helped the initiative to establish that the methodology can be used vendor-neutrally. Since then, according to Dr. Linus Schulz of Dechema, good progress has been made on functionalities, condition-based process control, diagnostics and maintenance, and we now know how information can be transferred vendor-neutrally, and without great expense, to the host process control system. The results were presented at the most recent annual general meeting of NAMUR, which means that manufacturers could now start to introduce this technology. In any event, the latest advances will be on display at HANNOVER MESSE 2018.