Festo: The Self-Learning Workplace for Human-Robot Collaboration at Hannover Messe
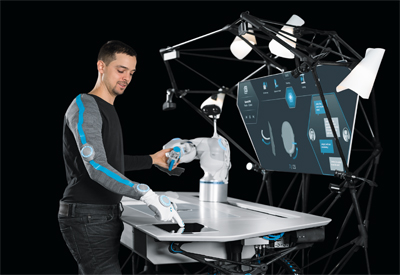
The networking of humans, machinery and IT is shaping tomorrow’s production. Not only production plants are now increasingly automated: even the components themselves are becoming more intelligent and are being networked to an increasing extent, thanks to the increased use of software components – in keeping with “Connect and Collaborate”, the motto of this year’s Hannover Messe. Festo is setting out to make its customers even more productive by means of new technologies from the field of digitalisation. “For us, this means focusing even more strongly on software development. We are paving the way for flexible functionalities by depicting more and more product functions in the form of software,” said Management Board member Dr Frank Melzer in summing up the prospects for the future. He has been Head of the Product and Technology Management department at Festo since October 2017.
The Festo Motion Terminal
A prime example of this development is the Festo Motion Terminal, in which the fusion of hardware and software has yielded the first valve to be controlled by apps. In future, components from Festo will be designed in such a way as to acquire and pre-sort data for analysis.
Festo offers various digital platforms for the appropriate evaluation and use of these data. “Our focus for the future will be on supporting and accompanying our customers even more closely with these platforms – not only in planning and commissioning their systems, but also in regular operation,” said Andreas Oroszi, Senior Vice President Digital Business at Festo.
The concept of the booth: Learn – Build – Operate – Inspire
The configuration of the company’s booth in Hanover also provides insights into this customer journey through the world of Festo: in the “Learn” section, Festo Didactic is presenting learning systems for the working world 4.0 and is demonstrating its training and consulting programmes.
“In the ‘Build’ section of our booth, we show how we can support our customers with intuitive configurators and simulation methods. With this virtual commissioning they can avoid unintentional collisions, optimise processes in terms of cycle times and programme control procedures in advance. This helps to reduce costs and effort for commissioning, and operational safety is also enhanced,” said Andreas Oroszi.
Operate: Festo accompanies its customers in the operation of their systems
Machinery and production data at shop floor level provide valuable insights into production processes. Thanks to condition monitoring of the systems and predictive maintenance, the customers can intervene before a malfunction arises. With the exhibits on the topic of “Operate”, visitors to the fair can experience further advantages brought about by intelligent networking for flexible, automated production processes.
The new opportunities opened by artificial intelligence and collaborative robotics for the working world of tomorrow are being presented by Festo in the “Inspire” section with its Future Concepts from the field of bionics.
Bionic Learning Network: the self-learning workplace for human-robot collaboration
“With the BionicWorkplace we are showing a self-learning workplace for human-robot collaboration that combines the advantages of the BionicCobot – the lightweight pneumatic robot – with IT systems from the field of artificial intelligence,” said Dr Elias Knubben, Head of Corporate Bionic Projects. The flexible workplace is fitted out with numerous assistance systems and peripheral devices that are networked and communicate with each other. Along with artificial intelligence, machine learning methods make the BionicWorkplace a learning and anticipatory system that constantly optimises itself. People can directly interact with the BionicCobot and control it by means of gestures, touch or speech. Remote manipulation of the system is also possible. This efficient, safe human-robot collaboration enables the manufacture of individual products down to lot size 1.
BionicFlyingFox: partly autonomous flight with motion tracking system
Flight is a constantly recurring topic for the Bionic Learning Network. For many years, Festo has been working together with universities, institutes and development companies in devising research objects based on fundamental principles derived from nature. For the BionicFlyingFox, the developers have turned their attention to the fruit bat, also known as flying fox.
Despite its wingspan of 2.28 metres, this ultralight flying object can turn with small radii of curvature. This is made possible by its intricate kinematics based on the scissors principle. The secondary wing is retracted during the upstroke and is unfolded again for the powerful downward stroke. To enable the BionicFlyingFox to fly partly autonomously within a defined airspace, it communicates with a motion tracking system that constantly records its position. At the same time, the system plans the flight paths and issues the necessary control commands. Take-off and landing are carried out by the human operator.
BionicWheelBot: unique forms of movement on the model of the cyclist spider
The cyclist spider was discovered at the edge of the Sahara in 2008 by the bionics expert Prof. Ingo Rechenberg. Like other spiders, the cyclist spider can run, but it can also move forwards using a combination of somersaults and rolling along the ground. Since its discovery, Prof. Rechenberg has been working on transferring these movement sequences to technological applications. The kinematics and the drive concept have now been developed in cooperation with the bionics team from Festo. The BionicWheelBot rolls along the ground by forming a wheel with three legs on each side of its body. Two more legs, which are retracted during running, are then extended. When the spider is rolled up like a ball, these legs push it off the ground and propel it forwards in a continuous rolling motion.
Bionics4Education
To generate enthusiasm for technology among young people, Festo is launching a bionics kit on the market this year. It contains the construction materials required for three different bionics projects: The Bionic Elephant’s Trunk, an adaptive gripper with Fin Ray Effect®, the Bionic Fish, and the Bionic Chameleon Gripper. The hardware is supplemented by a digital learning environment (www.bionics4education.com) with further content relating to bionics and some helpful tips for practical implementation at school or at home. This content, which is free of charge, helps pupils in constructing and programming the models, and teachers in planning their classroom lessons.
Festo at the Hannover Messe 2018 trade fair
From 23rd to 27th April 2018, Festo will be exhibiting the new Future and Bionic Concepts as well as further product innovations for factory and process automation at its main booth in Hall 15, Booth D11, with the stations “Learn, Build, Operate, Inspire”. Booths with products from Festo can additionally be seen at Siemens in Hall 9, Booth D35; here, Festo is introducing the topic of Dashboard E2M for the Siemens Mindsphere, and a display with the Multi-Carrier System. At Microsoft in Hall 7, Booth C40, a presentation can be seen on the topic “From the device to the Cloud via OPC-UA, as shown with E²M”. In Hall 6, Booth H30, at EPLAN in the Partner Community area, Festo is also represented with a computer workstation. You can also experience Festo in Hall 16, Booth F04 at Eichenberger Gewinde, and at the shared stands of PROFIBUS & PROFINET International (PI) in Hall 9, Booth D68, and Plattform Industrie 4.0 in Hall 8, Booth D24.
https://www.festo.com/net/no_no/SupportPortal/press.aspx?tab=10&s=t