HARTING Identifies Six Major Trends in Building IIoT infrastructure
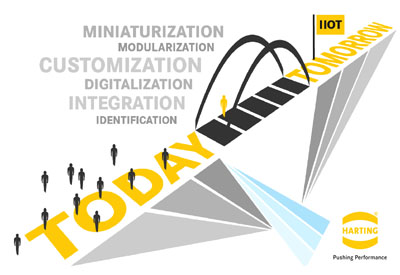
May 18, 2018
Six key trends are driving HARTING’s development program for the cyber-physical control infrastructure needed for advanced manufacturing. HARTING’s strategy, outlined by Jon DeSouza, President and CEO of HARTING Americas to guests at the company’s Open House at EDS Summit 2018 in Las Vegas this week, covers the company’s solutions for the digital production environment.
These six key trends are miniaturization, modularization, identification, integration, customization, and digitalization said DeSouza. “All six are important for realizing the full potential of the Industrial Internet of Things (IIoT), including the analytical benefits derived from Big Data. Globally, a great deal of emphasis is being placed on gathering, distilling and analyzing data at the Edge and in the Cloud, and with good reason because of how it can improve the entire supply chain. At the same time, HARTING is very focused on integrated solutions that include power and/or signal transmission, which are indispensable to optimizing IIoT manufacturing.”
DeSouza outlined what HARTING is contributing to each of the six trends.
Miniaturization: As more data via ever-smaller devices and sensors is added in the IIoT environment, more connection points are required. As a consequence, applications cannot get larger, so components must either offer higher density or a smaller footprint. One of the products DeSouza pointed to is the award-winning ix Industrial®. This extraordinary new connector series delivers Cat 6A performance for 1/10 Gbits/s Ethernet. This new standard requires 70% less installation space than the legacy RJ45.
Modularization: Modularization means offering flexible, reconfigurable production elements that have standardized interfaces for mechanical connections and power, data and signal transmission. HARTING’s Han-Modular® series illustrates this trend perfectly. Introduced to the market in 1994, this revolutionary connector concept allows the combination of multiple connection types into a single interface, for significant space-saving and flexibility as well as future-proofing.
Last October, HARTING launched a new campaign focusing on Han-Modular® to capitalize on this trend. In the six months since the launch, the company’s Americas group has seen a 23% increase in Han-Modular® sales, 27% increase in sample orders and a thirty-fold increase in Han-Modular® webpage views. This illustrates just how important modular connectors are to the industry.
Identification: Adding tracking functionality to systems through technology like RFID gives an object the ability to store information about itself throughout its entire lifecycle and have that information easily retrieved. This need is especially important in the industrial space. In 2006, HARTING introduced an industrial RFID solution developed specifically for utmost reliability even in harsh operating environments, with a product lineup that has continued to grow over the past dozen years.
Integration: Implementing communications protocols allows systems and sub-systems to talk to one another. Among its many current and planned functions, HARTING’s MICA serves as an ideal communications hub in a decentralized IIoT production environment. For example, the HARTING MICA has been used for energy monitoring in factory settings. It can monitor the amount of power used at the machine, measure power quality, provide insights into machine health and ensure process quality.
Customization: Adapting standard components to the needs of specific industries is highly cost-effective and responsive to customer needs. For example, HARTING customized the hood for its tremendously popular, economical Han-Eco® series of thermoplastic connectors to make them suitable for data center applications. This is why the customized Han-Eco® was selected as the connector for Microsoft’s open-source Project Olympus data center developed through the Open Compute Project.
Digitalization: Digitalization is taking things that typically do not transmit data or are analog and make them digital so that they can be integrated into larger IIoT systems. The flexible configuration possibilities with MICA mean shop floor and machine operations can be retrofitted to perform digital, networked applications for more efficient production processes, predictive maintenance, and documentation of process data.
“Innovation has always been a hallmark of HARTING – it’s always been part of in our corporate DNA,” said DeSouza. “Yet I can’t remember another time when we have been involved in so many developments that are changing how things are made.”