Rockwell Automation: Predictive Maintenance as a Service Helps Prevent Unplanned Downtime
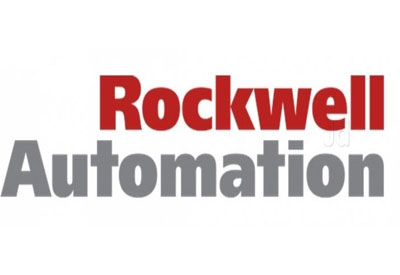
June 1, 2018
Losing critical assets can be devastating, causing unplanned downtime that can cost billions of dollars per year. In order to be more proactive in preventing these events, manufacturers and industrial organizations are beginning to schedule downtime events by employing advanced technologies and predictive maintenance. To help identify and prevent downtime on critical assets, Rockwell Automation has announced its Predictive Maintenance as a Service offering.
The service, which is applied on critical assets identified by the customer, analyzes data from connected technologies, such as sensors, control systems and smart machines. Leveraging FactoryTalk Analytics and applying machine learning technology, engineers from Rockwell Automation can identify normal operations and build out data models to help predict, monitor for and mitigate future failures or issues as part of a preventive maintenance strategy.
“By building up that backlog of historical data, we can start to see when there might be issues down the road,” said Phil Bush, remote monitoring and analytics product manager, Rockwell Automation. “This helps end-users focus on solving the problem proactively and minimizes the impact on production, rather than waiting for something to fail and trying to troubleshoot on the fly.”
Prior to deploying a predictive maintenance solution, one Rockwell Automation customer in the oil-and-gas sector experienced a bearing failure that resulted in over $3 million in costs related to maintenance and lost productivity. After working with Rockwell Automation to review over a year’s worth of historical data on the asset that failed, engineers found that the bearing cooling system had not been correctly operating for six months. If a predictive maintenance service had been deployed, the organization would have been able to identify the bearing failure and its root cause before the failure occurred.
This new service will be crucial in industries like oil and gas, where the uptime of critical assets drives the bottom line. This also includes critical machines in continuous-manufacturing operations. Additionally, OEMs can implement the service on an asset and use the predictive capability to provide better uptime performance scaled across all similar customer assets.
Using this service provides customers the ability to monitor predictions and analyze details of an alert without needing to build their own data models or engineer their own solution. Rockwell Automation delivers the data collection, machine learning and engineering support to build the models, validate and monitor patterns and predictions and keep those models up to date as data sets evolve.