Yokogawa Adds to OpreX Control and Safety System Family with Development of Redundancy Software Platform for Use with PCs
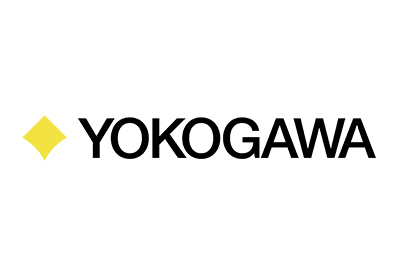
November 13, 2018
Yokogawa Electric Corporation announced that it has developed a software platform that enables software packages to run on general-purpose computers in a redundant configuration, and has added this to its OpreX™ Control and Safety System family. This redundancy software will help raise the availability*1 of all the solutions that make up Yokogawa’s OpreX Control category of systems, software, and devices. The first software packages based on this platform will be released in March of next year. These are the Exaopc OPC interface package and the Exapilot operation efficiency improvement package.
For enhanced availability in plant operations, Yokogawa plans at a later date to incorporate this redundancy software in other packages that make up the OpreX Control family.
Development Background
Our industrial infrastructure depends on having highly reliable systems that will keep running even when a fault occurs. Such systems often have redundant features such as a hardware control unit with the same functional capabilities that stands ready to take over in the event of a fault in the primary hardware unit. Yokogawa’s CENTUM™ VP integrated production control system, ProSafe™-RS safety instrumented system, and STARDOM™ network-based control system all achieve high availability and reliability thanks to the use of such redundant hardware.
Manufacturing execution systems (MES) and other types of applications typically run on a general-purpose PC that is not set up for use with another PC in a redundant configuration. To accomplish that, it is necessary to either install some kind of dedicated hardware or add a function to the PC software.
Many of our customers have expressed an interest in a solution that would enable them to achieve a redundant configuration at a reasonable cost. To satisfy this need, Yokogawa has developed this software platform.
Features
- High availability
If a fault occurs, this software initiates a transfer of control from the active PC to the standby PC that takes no longer than one second to complete, which is well within the operating parameters of oil, petrochemical, chemical, and other process facilities, where the collection of data and the issuance of control commands based on that information typically takes a few seconds or more. Since the data and status information on the two PCs is always synchronized, processing can continue without interruption, even when the system is performing sequential control of multiple tasks. This feature minimizes the probability of any loss of data and ensures there is no interruption in control. This software thus ensures the high availability of the systems that make up a vital part of our industrial infrastructure. - Long-term operational support with online PC replacement
General-purpose PCs often remain in use for years in plants and need to be replaced when they grow outmoded or fail. Thanks to this software that enables applications to run in a redundant configuration, an outmoded or defective PC can be replaced while the system is online. It is even possible to operate different PC models in a redundant configuration providing they have been tested and approved by Yokogawa. This will help customers operate their systems stably over long periods of time and improve productivity.
Major Target Markets
Process industries such as electric power, water supply and wastewater treatment, industrial water, semiconductors, foods and pharmaceuticals, iron and steel, pulp and paper, oil, petrochemicals, and chemicals
Applications
Configuration of a high-availability redundant system using two PCs