Sandvik launches new underground drill operator training simulator for learning anywhere, anytime
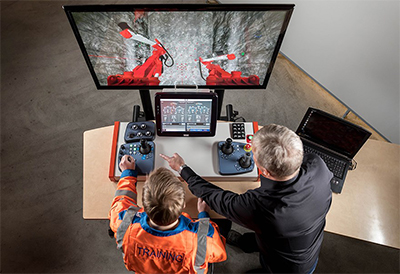
Febraury 27, 2019
Sandvik Mining and Rock Technology has introduced an operator training simulator to provide a compact and flexible solution to safely train operators and maintenance teams on its DD422i, DD422iE and DT922i drill rigs. This latest development provides a low weight safe training tool that is highly portable, enabling it to be used where it is most needed – on site. The new Sandvik Operator Training Simulator has been designed specifically to improve both operator and drilling performance, delivering real benefits for underground drilling applications.
The latest development from Sandvik is a fully mobile system which weighs less than 50kg, enabling training to be undertaken anywhere. The simulator delivers ‘real life’ training in a simulated working environment, with drill rig operators and maintenance teams learning about rig capabilities before progressing to the actual equipment. The simulator acts like a real rig, operated with authentic controls and combined with the same control system software as that installed on the drills themselves.
The simulator comes with purpose-developed software that includes a range of specific exercises for recording and measuring operator behavior. The trainer can initiate machine faults, incidents or hazards to train and assess operators, thereby ensuring they are able to respond correctly to any scenario with maximum efficiency. Additionally, training sessions can be conducted for multiple participants in a safe environment, preventing risk of injury or material damage. Furthermore, it facilitates regular operator retraining and the implementation of an operator assessment process without impacting on site productivity.
Learn anywhere, anytime
Thanks to its compact size and its wheeled carrying case, the simulator can easily be carried by a single person to wherever it is needed. With a very short set-up time, operator training can begin even before the rig has been delivered and commissioned. This provides increased levels of operational efficiency, with no learning curve required prior to using the rig on site.
The simulator has been designed to enable tailor-made training sessions to suit trainee experience levels, using a range of exercises and simulated conditions in a variety of applications and situations. A report evaluates and measures trainee performance, ensuring that the training is of direct benefit to operators.
Improved EHS
The simulator safely develops and refreshes operators’ skills within a protected environment and significantly reduces the drill start up period. It has been designed to ensure that rig operators are fully familiar with the features and the capabilities of the Sandvik rig from day one. The shorter transition to using the real equipment results in quicker familiarization, improving efficiency and productivity. Additionally, there is no risk of equipment damage, zero consumption of rock tools and fuel, zero emissions and no exposure of the trainees to risk in familiaring them with a new drill rig.
Up and running fast for optimized operational performance
Ensuring that operators can use the drill rig to its full potential safely and productively as quickly as possible is what the simulator is about, with the training simulator performing all boom and feed movements, as well as the entire drilling cycle. It is fully compatible with Sandvik iSURE software – Sandvik’s tunnel management tool for accurate drilling, charging and blasting plans.
Thanks to the training course management tool, the trainer can customize training and use multiple pre-planned training scenarios. This ensures 100% peace of mind, with training routines and exercises repeated until the appropriate level of knowledge is reached.
The use of the simulator is estimated to produce a 5% increase in annual productivity in rig availability alone. In addition, training costs are reduced by up to 35%, with training sessions being easily and safely conducted on site with multiple operators.
Key features of the Sandvik underground drill simulator
- Simulator weight: 20 kg
- Protection case weight: 25 kg
- Total weight with accessories: 50 kg
- Simulation Laptop: i7 processor, Nvidia GTX1050 graphics, 8GB Memory, 250GB HDD (provided with simulator)
- Available languages: English and Spanish, others on request
- Power supply: 100, 240 VAC, 200 W delivered with European (SCHUKO) power cables. Other plugs available on request
- Recommended optimal setting: adjustable table for the console to enable best ergonomic height:
- Distance to the TV screen: 1 meter for 50”, 2 meters for 65” (ideal)