Schneider Electric Launches First Smart Factory in the U.S. Demonstrating Quantifiable, Real-Time Benefits of Innovative EcoStruxure Solutions
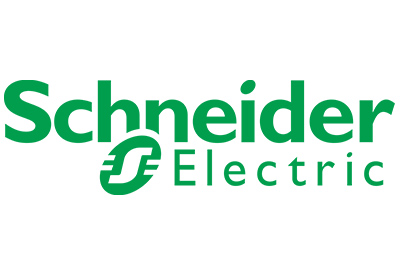
June 18, 2019
Schneider Electric has launched the first Smart Factory in the U.S. to demonstrate in real time how its EcoStruxure architecture and related suite of offerings can help increase operational efficiency and reduce costs for its customers. Embracing cutting edge technology and the benefits of the Industrial Internet of Things (IIoT) to drive process optimization, the facility has opened its doors to share their IIoT knowledge and smart manufacturing technology best practices with customers and partners across industries.
In operation for more than 60 years and employing nearly 500 people, the Schneider Electric Lexington facility has embraced modernization and digitization as critical aspects of their continued success. Today the factory is smart and integrated, relying on digital tools such as augmented reality, which empowers operators to gain visibility into operations maintenance, driving a 20% reduction in the mean time to repair on critical equipment, and process digitization eliminating paperwork by 90%.
Schneider Electric has launched several Smart Factories around the globe in countries including Mexico, China, France, India, Indonesia, and the Philippines. These are core in its Tailored Sustainable Connected 4.0 supply chain digital transformation where Schneider Electric leverages digitization across its supply chain operations to deliver end-to-end integration and visibility to enhance its performance.
“We understand the value of IIoT and the positive business impact that innovation and digitization can have on our operations – particularly in our global supply chain. As a living example of how our EcoStruxure solutions deliver benefits to our customers, we are gaining those same benefits in our operation and sharing that knowledge,” said Mourad Tamoud, Executive Vice President, Global Supply Chain, Schneider Electric. “With our latest Smart Factory showcase, we are able to demonstrate this value in real-time, show the solutions at work and share the tangible benefits that we ourselves are seeing from our own IIoT investment as we accelerate our Tailored Sustainable Connected 4.0 digital transformation.”
Digital transformation and modernization of a legacy facility
Modernizing a working facility that has been in operation for over half a century presented a challenge. Unlike a greenfield facility – one that is built new with the latest technologies incorporated from the beginning – modernizing this legacy brownfield facility needed to be done over time, requiring the Lexington team to strategically balance the need to embrace new, connected technologies with the needs of the business and a set operating budget. This successful digitation evolution took a step-by-step approach, adding new EcoStruxure technologies individually where they would provide the greatest value and connecting them with existing equipment.
As part of the Smart Factory program, Schneider Electric outlines that brownfield implementation for customers who may be facing the same challenges with their existing production facilities. The team is able to offer strategies and talk through the challenges they faced to help customers exploring IIoT connected technologies to overcome those same hurdles toward their modernization goals. By sharing their experience in leveraging EcoStruxure solutions, visiting customers can better understand the value of the brownfield modernization and the resulting operational efficiencies.
Lexington facility benefiting from Schneider Electric EcoStruxure innovation
The Lexington factory is a heavily-automated operation critical to the Company’s supply chain, producing Load Centers and Safety Switches. The facility will now serve as both a working operation and a showcase for customers and partners to witness how digital transformation can help them make informed, data-driven decisions to bring about improved profitability, asset management performance, operational efficiency, and a smarter productive workforce while keeping the operations secure, agile and environmentally sustainable.
The Lexington Smart Factory serves as best practice and example of the benefits of digitizing energy management and automation in manufacturing. In this production environment, these solutions have demonstrated operational and quantifiable value since their implementation:
- EcoStruxure Augmented Operator Advisor – Delivered a 20% reduction in the mean time to repair on critical equipment where it has been implemented.
- EcoStruxure Resource Advisor and Power Monitoring Expert – Delivered 3.5% YOY energy savings in the Lexington facility in addition to $6.6 Million in regional savings since 2012; sophisticated reporting capabilities and increased transparency also drive operational performance.
- AVEVA Indusoft Web Studio – Delivered powerful Edge digitization of paper processes to eliminate paperwork by 90% and cloud connectivity has enabled digital dashboarding of a critical process.
- RFID OsiSense – Eliminated 128 daily fork truck miles and eliminated $500,000 in Work in Progress (WIP) inventory with a 33% first-year ROI.
- AVEVA Insight Data – Unlocked and shared silos of data in a mobile manner reducing downtime in critical processes by 5% with ROI of less than 6 months.
- Magelis GTU/GTUX HMI – Provided agile operator management of the process and vivid visual of the process onsite and via mobile devices.
For more information, visit HERE.