Siemens presents extended Digital Enterprise portfolio for more effective use of digital data
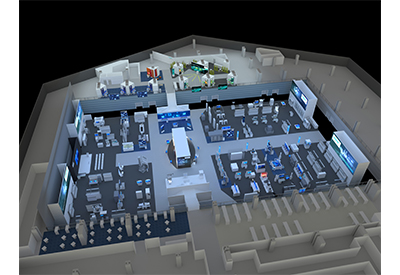
October 8, 2019
- This year’s trade fair slogan: “Digital Enterprise – Thinking industry further!”
- Next level of digital transformation will be achieved through cutting-edge technologies such as Edge and cloud computing
- This leads to increased productivity, flexibility and efficiency
- Data can be evaluated and used more comprehensively and in greater depth. Data sovereignty always remains with the data owner
At “SPS– Smart Production Solutions” 2019, Siemens is presenting industry-specific applications and future technologies for the digital transformation in the manufacturing and process industries under the slogan “Digital Enterprise – Thinking industry further!”. At the heart of the over 4000 square meter booth are products, solutions and services from the Digital Enterprise portfolio, which help customers to reduce their time-to-market and to increase productivity, flexibility and efficiency.
Siemens is introducing a newly developed complete system for industrial operation and monitoring: the web-based visualization system comprises Simatic WinCC Unified visualization software and a new generation of Simatic HMI Unified Comfort Panels. With Sinumerik One, Siemens presents the CNC system for the digital age. By seamlessly combining the virtual and real world, this system makes machine tools more productive, reduces time-to-market and increases machine performance. As part of Digital Connectivity, Siemens is also presenting new CloudConnect products. They enable data from each plant to be transferred quickly, easily, and securely to the cloud.
The integration of cutting-edge technologies in the portfolio provides companies in all industries with new, extensive opportunities to make better use of the rapidly growing volume of data in industry: these range from the use of artificial intelligence and Edge computing to future factory and process automation. Data sovereignty always remains with the data owner. Using the example of the automotive industry, Siemens will demonstrate at the fair how development and production times can be reduced regardless of the engine concept (diesel, gas, electric). Fully automated manufacturing concepts with high quality and accuracy as well as industrialized additive manufacturing lead to increased performance, shorter setup times and a transparent battery development and production process. The strengths of modular process plants are illustrated at the booth using a “plug and win” separator unit from GEA, which is automated with Module Type Package (MTP) and supported by web-based applications as well as digital services based on MindSphere. These apps increase the transparency and efficiency of the plant through the optimization of control circuits and maintenance schedules.
AI services to improve plant availability and product quality
Siemens service experts support digital transformation with a comprehensive approach of services from consulting via implementation through to optimization. This also applies to AI-based services, which connect the field level to Edge and the cloud. Data are analyzed both locally on the machine and subsequently in the cloud using AI-based algorithms. This enables the customer to predict unscheduled machine downtime and to adjust product quality. With Predictive Services, Siemens presents modular service packages for the early detection and correction of faults. In addition, with “Closed Loop Analytics Services”, Siemens shows how data analytics and AI can be used to unlock previously untapped potential in the production and process environment. Therefore, reduction of test applications, increase of manufacturing throughput and improvement of machine learning models through new data in MindSphere can be achieved.
Easy data transfer to all popular cloud platforms
Siemens is also introducing innovative CloudConnect products for Digital Connectivity at the fair. They enable data from each plant to be transferred quickly, easily, and securely to the cloud.Siemens is also presenting PlantSight, the cloud-based portal for all plant information. With this solution, data can be efficiently consolidated, contextualized, validated and above all visualized. This creates a comprehensive, seamless digital context across a range of information sources and data formats. Plant operators can benefit from the excellent reliability and quality of the information and the resulting increase in operational availability and reliability for their plants.
Simatic PCS neo is a completely new development in terms of system software and is based entirely on web technologies. It provides brand new opportunities for companies in process industries in the age of digitalization. Besides direct and secure system access from any location and from any device with an HTML5-capable browser, Simatic PCS neo offers unique usability with all relevant information available within a single workbench. An optimized, easy to use GUI for all tasks and system users means that any information can be reached with just a few klicks. A consistent object-oriented data model increases efficiency in engineering and operations with clear and accelerated workflows.
Setting new standards for industrial operation and monitoring
At SPS, Siemens is introducing a newly developed complete system for industrial operation and monitoring: the web-based visualization system initially comprises Simatic WinCC Unified visualization software and new generation Simatic HMI Unified Comfort Panels. The new system provides the user with a solution for HMI and SCADA (Supervisory Control and Data Acquisition) applications, and in the future also for Industrial Edge, Cloud and Augmented Reality scenarios. A further product innovation is the compact drive-based Simatic Drive Controller. The device integrates the Simatic S7-1500 controller with Motion Control functionality directly into the modular Sinamics S120 multi-axis drive system. With the Simatic Drive Controller, synchronizations (gear or cam synchronization) can be implemented between axes that are on different CPUs. This makes it easier to distribute power over several CPUs and provides the basis for the easy implementation of modular machine concepts.
New Security Services protect productivity
Digitalization is leading to further increases in networking – right down to the sensor level. For automation, it is particularly important to be protected against possible risks. To support users in this area, Siemens offers a comprehensive, wide-ranging protection concept that complies with the recommendations of IEC 62443, the leading standard for security in industrial automation. A new concept being presented at SPS is Industrial Security Services specifically for Simatic automation systems, which include solutions for appropriate security configurations and efficient management of weak points.
Innovative solutions for digitalization in drive technology
At the trade fair, Siemens is also presenting its digitalization portfolio for the drive train: this covers the entire value chain from design through planning and engineering to production and services. With innovative products such as the new Sinamics G120X converter series, Simatic Micro-Drive and Sinamics S210 servo drive systems, plus Simotics low-voltage motors, Siemens offers a hardware portfolio that combines with intelligent software to create transparency along the drive train and to ensure reliable operation. New interfaces and connectivity modules in the form of Sinamics Connect 300 for low-voltage converters and Simotics Connect 400 for mains-operated motors enable machine and plant builders and users to acquire data from the drive train. This data can be used to create digital data models such as a digital twin and therefore for the overall optimization of machines and plants. With existing low-voltage converters, Sinamics Connect 300 ensures that data is sent to the cloud, while in future Siemens will also offer the option of retrofitting running low-voltage motors in the field with the Simotics Connect 400 connectivity module. This will enable low-voltage motors to send operating data to the cloud-based Sidrive IQ Fleet app without the need for any structural modifications. In addition to the Sidrive IQ Fleet MindSphere app, the Analyze MyDrives app can be used to obtain important information on the status of drives, leading to fewer downtimes and the increased productivity of machines and plants.
Solutions for an intelligent and secure electrical infrastructure
The electrical infrastructure is crucial for the smooth operation of automated production plants. Integrated in digital environments, it ensures secure, reliable and efficient power supply for plants, machines and buildings. It also provides important data for increasing energy efficiency and for optimized production processes and predictive maintenance. At the trade fair, Siemens is demonstrating how low-voltage systems, communicative protection and measuring devices and industrial switching technology can be optimally integrated into automation and cloud systems.The 7KN Powercenter 3000 IoT data platform will also be presented. As a central gateway, it collects and processes energy and status data from electrical consumers and forwards the bundled data to automation or open cloud-based IoT systems such as MindSphere. Using Sivacon 8PS busbar trunking systems with innovative powerline technology, data can be transferred from the measuring and switching devices installed in the tap-off units directly via the conductors on the busbars – an additional data cable is no longer required. With the Sirius portfolio for industrial control technology, machine and control cabinet builders benefit from a universal system of switching devices, which helps them to find the ideal solution for all switching and control tasks. The devices are part of Totally Integrated Automation and support efficient project engineering and flexible use. They are also able to acquire machine data and make it available for detailed analytics in higher-level systems and IoT environments.