Cobots – the ultimate all-round power tool
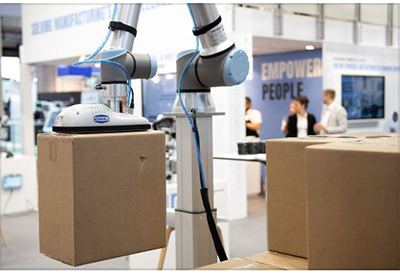
January 23, 2020
When humans and robots collaborate, the key – somewhat paradoxically – is to ensure the robotic half of the duo does not operate at maximum power and speed. And the reason for that is very simple: safety. Human workers should be able to walk away uninjured from their interactions with their robotic colleagues. That is why cobots have a range of design features, including sensor systems, to prevent them from accidentally harming their human counterparts. Safety in human-robot collaboration will feature strongly in the robotics displays in Hall 6 at the upcoming HANNOVER MESSE.
In addition to safety, the displays will focus on the many advantages of cobots in factory settings. Cobots can relieve their human co-workers of unpleasant, highly demanding physical tasks and make processes steps more flexible and, ultimately, more cost-effective. “A cobot is a versatile, all-round power tool for highly fluid production environments,” comments Dr. Jens Kotlarski, CEO of Yuanda Robotics. “You start by showing the cobot what its required task is, and then you instruct it to perform the learned task autonomously.” The cobot’s value in this scenario is that it combines the twin benefits of versatility and cost-effectiveness. “Even if you use the cobot system to automate process steps at a different machine or plant every day, it still makes good commercial sense.”
HANNOVER MESSE 2020 will present numerous cobots of various types and makes. Market leaders like ABB, Atlanta, Bosch, igus, Pilz GmbH, Stäubli, Universal Robots, Yaskawaa and, of course, Yuanda will present their collaborative robots in an extensive line-up that will be clustered primarily in the new robotics section of the show in Hall 6. The line-up will also include robot components, such as gripping systems by providers like Schunk and Zimmer, and industrial image processing systems by leading providers, such as ISRA Vision and Stemmer. The Hall 6 showcase will also include conventional industrial robots by Yaskawa, Stäubli, Yamaha and many others, as well as supporting software solutions for robot programming, such as the suite developed by ArtiMinds Robotics.
“Robots and cobots offer major potential for flexible automation in manufacturing, especially when used in conjunction with machine learning and artificial intelligence,” said Hubertus von Monschaw, Deutsche Messe’s Global Director Automation, Motion, Drives for HANNOVER MESSE. “HANNOVER MESSE showcases what is technically possible today and skips forward into the near future to explore tomorrow’s digitalized industrial landscape.”
But back to the issue of cobot safety. Working alongside cobots takes some getting used to, obviously, but it is certainly no cause for concern or fear, given the existence of worldwide safety standards paired with risk analysis and compliance requirements. “When selecting a cobot, the first step is to make sure the one you are thinking of buying complies with the applicable safety standards,” explains Yuanda Robotics CEO Dr. Jens Kotlarski. “No cobot can be truly safe unless it has been certified as being able to reliably monitor its own speed of movement, position and force applied.”
Apart from that, safety very much depends on what applications the cobot is used for, including what tools and work-pieces are involved. “It is very difficult, for example, for a robot intended for cutting applications to be deployed collaboratively,” explains Kotlarski. “In these higher-risk applications, we recommend adding a non-mechanical safety barrier. For example, safety light curtains can be connected to the cobot system and integrated at the push of a button, providing a reliable means of immobilizing the robot if anything crosses the barrier. The result is a safe automation solution that is fast and simple to implement without convoluted risk assessments, despite the involvement of potentially hazardous machines and work-pieces.”
HANNOVER MESSE’s central platform for robot manufacturers, system integrators and providers of industrial image processing solutions is the Robotics, Smart Automation & Vision Technology pavilion in Hall 6. Offering live demonstrations and loads of opportunities for networking, the pavilion is always an absolute hive of activity. There are also special Mobile Areas for mobile robotic solutions.
Hall 6 is also home to the Automation Forum, where speakers from industry and research will be sharing information and insights on a range of topics, including robotics, mobile robots and industrial image processing. And last but not least there’s the ROBOTICS AWARD, the annual highpoint of all things robotic at HANNOVER MESSE where the best applied robot solutions are celebrated and honored.