Presenting the Newest EPLAN Platform
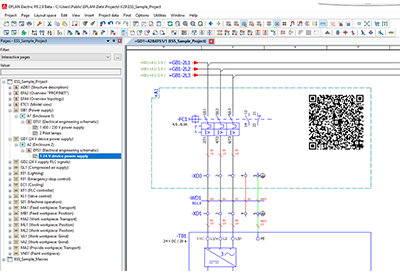
March 3, 2020
EPLAN Platform, Version 2.9, has been available since the end of January. Quickly generated QR codes can store hyperlinks, which can be opened out in the field. Layers Management ensures all changes are saved automatically, making implementing company standards even easier. Projects can be completed faster with mass editing of project data using expanded navigators. And speaking of standardization, macros can now easily be re-used.
In EPLAN Platform, Version 2.9, QR codes can be easily generated. Users can store hyperlinks in their documentation that can later be scanned and opened with apps on mobile devices such as smartphones or tablets. It can be used for both internal and external links, making tedious typing a thing of the past. The QR code also works on printed documentation, making it faster and easier to use. Exchanging symbols in placeholder objects has also been simplified and they can now be replaced by selecting the appropriate value sets. Users benefit from greater transparency with fewer macro variants.
Dockable Layers Management Layers
Management has been made even easier than before as a dockable dialogue: all changes are now saved automatically. Additional functionality, including searching layers and changing their properties round off the improvements. Starting now, it is easy to search a project for all objects that have been assigned to a particular layer in a project or subproject. Designers can then use the Properties dialogue of a found object in the search results list to change the assignment of the layer they just searched for. This allows layers that were added to a project via DXF or DWG import to be easily found, quickly modified and used as userdefined layers. An additional benefit is that users can implement company standards with simple adaptations and definitions, analogous to the navigators.
Quickly reaching the goal: Navigator display
The list view of the Macro Navigators was changed into a table with cells in the previous version of EPLAN Platform, which can be edited fairly easily as a result. In the newest version, this function was expanded to additional navigators, for instance the Parts Navigator, PLC Navigator and Wire Navigator. This gives Version 2.9 powerful practical advantages since project data can now be edited en mass in the blink of an eye. Speaking of macros, once a macro project is completed, standard-ised macros can be inserted into other projects from the Macro Navigator using drag & drop. It naturally also works within a macro or schematic project in which the user has created the window and symbol macros. This results in considerable time savings because the previous cumbersome selection via the macro selection from the directories is no longer necessary. An additional plus is that data are being re-used, which ensures and increases the project quality.
Cleverly configured: Property arrangements
The new Management dialogue makes it much easier for users to edit user-defined property arrangements for schematics and 3D device placement. Users can check these in the Management dialogue and easily remove user-defined property arrangements that aren’t being used. A Context menu helps users easily find the used properties. The benefits are clear: All the property arrangements existing in a project can be displayed in one place. Furthermore, several properties can be edited simultaneously when exporting and importing property arrangements for different components. The names can also be just as easily translated, and the new search possibilities assist in making adjustments to implement company standards even faster.
Translations: Much clearer
In Version 2.9, multilingual entries can be made for many properties and input fields in both projects and Parts Management. User can then manually translate them into a uniform language or have it done automatically. EPLAN Platform, Version 2.9, now provides an extra helping of clarity: fields for which multilingual input is possible are now marked at the front with an icon on the user interface as the standard. How does it work? When the designer enters a text into a multilingual field, it is initially languageindependent. In case it needs to be translated, it will then be assigned to the specified source language.
For more information, visit www.eplan.de/platform29.