Pilz Launches a Dedicated Playlist for Webinars
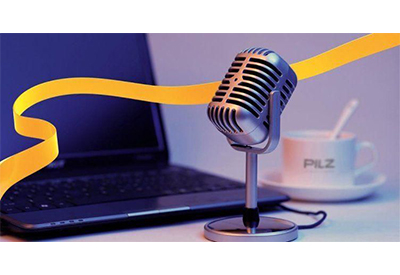
April 6, 2020
Pilz US hosts numerous machinery safety webinars on its dedicated YouTube channel.
The channel gives you the opportunity to brush up on their machinery safety knowledge on your own time, or to revisit previously watched webinars for a further review of key standards and technologies.
The webinars include:
Protect your staff and your workplace with Optoelectric devices: Safety managers know that the proper use of optoelectronic sensors protect their staff and capital goods – safely, efficiently and economically. These devices provide optimum protection for plant and machinery when there is active intervention into the production process. Optoelectronic sensors range from light barriers/curtains to area scanners to vision systems and more.
Optoelectronic sensors can provide finger, hand or body protection in accordance with specific standards, depending on the requirement.
In this webinar, you’ll learn how optoelectronic technology helps protect specific danger zones at your workplace. If a light beam is broken, for instance, the sensor will immediately trigger a safe shutdown command. Muting, blanking and/or cascading open up a wide range of possibilities for optimum incorporation of the light barrier into your plant. Learn more about why this safety technology is appropriate for a wide range of industries and applications.
- – Types of optoelectronic sensors
- – Standards used for presence sensing devices
- – Safe distance formulas for different presence sensing devices
- – Calculation techniques of stop time
- – Applications for optoelectronic sensors
Calculating safe distances – An Application of Presence Sensing Devices: The effectiveness of particular types of safeguards depends in part on the correct positioning of the relevant parts in relation to the danger zone. ISO 13855 primarily defines human approach speeds. These approach speeds need to be considered when designing safety measures and selecting the appropriate sensor technology. Different speeds and sizes are defined, depending on the direction and type of approach. Even an indirect approach is considered.
Viewers will learn:
- – Safe distance formulas for different presence sensing devices
- – Calculation techniques of stop time
- – Application standards used for presence sensing devices
Ergonomics – Operator compatibility: Guidance for the designer, supplier and end user: Ergonomics is the scientific study of people at work; assessing the capabilities and limitations of the worker in relation to the demands of the machine, job and work environment. The primary goal of ergonomics is to reduce the physical stresses on employees, thus minimizing or eliminating injuries and disorders in the workplace. Poor worksite and machine related designs can lead to painful and costly injuries for employees and lower productivity for the employer.
What you will learn:
- – Standards available for guidance
- – What elements to consider in an ergonomics improvement process
- – What factors to consider with regards to the worker population
- – What percentile of men/women should be considered
- – Why educating employees is so important
- – How to reduce risk with a cost vs benefit analysis
Machine guiding – Back to basics: Once the risk assessment has been performed, the methods and techniques to be applied to reach the maximum risk reduction level will be the focus. When the hazard cannot be eliminated, design measures to properly reduce the risk to the hazard to an acceptable level will be shared. Expected functionality and practicality of the selected safeguarding applications include the selection of the prescribed safety standards currently available.
- – Selecting the prescribed safety standards
- – Understanding the key factors of proper guard design
- – Utilizing the proper guarding methods and techniques
- – Recognizing proper guarding vs. awareness barriers
- – Applying color coding and safety signs
Human-Robot Collaboration: Robot Safety Requirements: The closer man and machine work together, the more efficient work practices become. However, safe interaction between human and robot increasingly demands new technologies and solutions. The demands on safety increase, the closer human and machine get to each other.
This webinar will familiarize attendees with the regulations and standards applicable to robotics in the United States.
Topics will include:
- – What’s new in robotic safeguarding
- – Relevant safety regulations and standards for robots and robot systems in the USA
- – New safeguarding requirements
- – Why a risk assessment must be performed
- – Collaborative robots
The Facts on CE Marking: Industrial machines shipped into the EU are subject to the CE marking process. This marking process is also true for industrial machines produced or substantially modified within the EU. The CE mark declares that your machine meets the essential requirements of all relevant EU directives. Products that carry the CE mark may be imported and sold without restrictions from national regulations within the EAA. Assemblies of machines such as robotic cells and production lines also fall under this obligation and will be required to be CE marked accordingly.
The aim of this webinar is to enable you to understand the requirements of the Machinery Directive in relation to CE Marking
- – How to determine the scope of machinery that is applicable to CE Marking legislation
- – The role of manufacturers, importers, designers etc., of machinery with regards to CE Marking
- – The requirements and process of CE Marking
- – Other main directives applicable to CE Marking and their requirements: Machinery, Electromagnetic Compatibility (EMC), Low Voltage (LVD), etc.
Safety Lockout System – An Alternative Method for LOTO: Typical existing equipment used to isolate motive power are not designed to handle the frequency of access required for modern machinery, and changing out disconnects is expensive and inherently an unsafe job. The Safety Lockout System, SLS, is a system to safely disconnect machines and facilities from electrical, hydraulic and pneumatic power, provide automatic zero energy verification in order to protect personnel, and comply with industry standards to prevent unexpected start-up. This webinar will review LOTO procedures and relevant standards and concepts for achieving compliance, along with the advantages of the SLS as an alternative.
Topics will include:
- – The challenges with manual disconnects
- – The challenges with using a contactor as an isolator
- – UL 6420 Equipment Used for System Isolation and Rated as a Single Unit
- – OSHA acceptance for System Isolation Equipment use
Upon completion of this webinar, attendees will have a better understanding of LOTO requirements and how a Safety Lockout System may be a more appropriate alternative for their manufacturing facility.
Risk Assessments: Risk assessments are the key to machinery safety. They pave the way for a level of risk reduction that’s both effective and economical. Many activities carried out by operators and maintenance staff represent a high risk.
Often it takes just a few factors to cause an accident. If you build, retrofit or interlink machinery, a competent risk assessment is the most important basis on which to design machinery safely or determine the necessary protection measures.
A thorough risk assessment should include:
- – Identifying the applicable standards and regulations
- – Defining the machine’s limits
- – Identifying all the risks in each of the machine’s lifecycle phases
- – Estimating and assess the risk
- – Recommending an approach for reducing risk
Learn more about all aspects of risk assessment from this webinar.
Reducing Risk – by Design: In terms of safety, each machine in your plant must be considered individually as it relates to its lifecycle. This applies whether the machine is new, retrofitted or converted. The process starts with a Risk Assessment. So now that the risk has been assessed, what’s next?
Participants will learn:
- – Overview of Risk Assessment methods
- – Risk reduction methods
- – Ways of reducing risk in compliance with Standards and Directives
- – Guarding by the numbers
- – Designing for safety
- – Selecting the proper safety components
- – Validating your risk reduction
So grab a bowl of popcorn, sit back and relax as you click on any of the titles above for some informative presentations.