State of the Canadian Automation and Control Industry
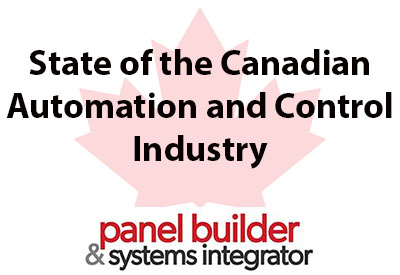
April 21, 2020
I think many of us right now are caught at a point where we are either looking back at where we were, or forward in hopes of better to quench the worry and uncertainty of the times. And although we have heard it often, we will come through this, and it is those who are focused forward that we all need to follow.
To put things in perspective and consider where we as Canadians working in automation and control stand Panel Builder & Systems Integrator asked you about your business operations, how your work life has been affected as well as whether your digital learning tendencies have changed.
The survey was conducted Nationally across a variety of automation and control related markets.
The survey returned 136 results from Panel Shops, System Integrators, OEM’s, Electrical Contractors. Engineering Firms, Manufacturers, Distributors and select End-Users. Integrators, Manufacturers and Distributors returned the highest number of results.
Secondly, we asked respondents to identify their current activity level of their company. And although we knew the results would vary for a National survey, the results are certainly more positive than anticipated.
There is no question that all industries have been hit hard and those working in automation and control are no different. However, with many sectors in complete shutdown only 6% of respondents noted that all work was on hold. Certainly, things are difficult with 11% only performing emergency services, 19% on reduced hours and 25% having had to commit to layoffs. But 39% are at full operating capacity, which does show some promise that the automation and control markets have not completely halted and with demand still in place it will likely be a quick sector to rebound.
When looking more closely at the specific responses we can make some deeper insights. Manufacturers had the highest result for working at full capacity at 65%, followed by Systems Integrators at 45% and Panel Shops at 37%. Distributors had the highest number of layoffs at 46%, while 39% of electrical contractors noted they are only performing emergency services.
We should look at these numbers for what they simply are, a point of fact that although many are affected, and much work has slowed the industry you serve has not ground to a halt. Automation is vital to our future and when looking for above it continues to move forward.
As part of survey we also respondents to comment on how the current situation is affecting their work and we received a wide range of responses. Overall the most direct and common response was working remotely and doing the best we can (For this I comment you all, it is not an easy to task but from Atlantic Canada to Western the comments about safety and protection were consistent).
That said there have been some other key points from various sectors. Those in sales have noted that they often worked from home so that has not changed. However, several stated that as salesmen they are very social, and some are feeling the lack of social interaction. Some have said that digital meetings work but are not ideal, with several even noting it has hindered their ability to interact and read body language.
Those that are open have noted increased cleaning and social distancing measures on the shop floor, and all noted where possible office staff are working remotely.
Another interesting point, and one that is of great importance for those still operating is to carefully monitor receivables and payables as these have slowed down, although the actual workload has not.
The most interesting note however was a unique business model shift that was implemented by a systems integrator. This systems integrator redistributed all work to the homes of staff by bringing tools and setting up small workshops in the homes of their employees, essentially setting up decentralized workstations. I found this to be extremely ingenious and a great way for the company to support their employees, ensure they are safe and keep business going.
In all we were not disappointed by our readers in their comments and there were some great points made.
Finally, we also wanted to learn about whether companies are also increasing their digital learning opportunities. For this we asked how likely companies are to attend virtual events and webinars and what topics they are most interested in learning about.
Of those surveyed 36% said they were likely to attend events while 29% noted they were highly likely. This demonstrates that currently 65% of professionals in the automation and control market are currently considering engaging in virtual events and webinars. And with another 17% undecided it is only 18% of people that are unlikely to engage.
Regarding desired topics there was a very broad range of ideas presented, each of which we will be addressing and attempting to develop content to support. The most desired topics were industry trend information, industry 4.0, IIoT Trends, Technical and Product information sessions, and safety training.
In all, the impact has been substantial, not just on those in Canada but around the world. And although many have individually felt pressure there is light at the end for an industry that will certainly weather the blows coming its way and will again continue to grow across Canada.