FANUC to Feature Robot and Cobot Solutions for Picking, Packing, Fulfillment and Palletizing at Pack Expo Las Vegas
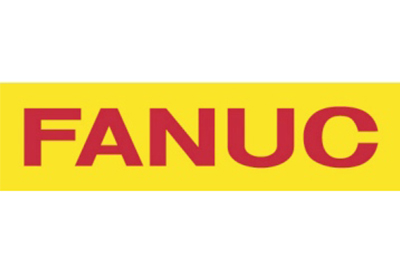
September 7, 2021
FANUC America, a major supplier of CNCs, robotics, and ROBOMACHINEs will demonstrate a wide range of automation solutions for picking, packing, fulfillment and palletizing at Pack Expo Las Vegas, Sept. 27-29, in booth #1441.
CRX Collaborative Robot
FANUC’s CRX cobot is an easy-to-use and flexible solution for a variety of applications, including palletizing, packing, inspection, and many more. Built-in sensors on each axis can allow the CRX cobot to work safely alongside people without the need for expensive guarding. In addition, the CRX can operate for eight years maintenance-free, which is a game-changer for companies looking to lower costs and maximize productivity.
At the show, a FANUC CRX-10iA/L equipped with an iRVision 3DV/200 vision sensor will demonstrate case palletizing. The CRX will use the 3DV sensor to find a box, pick it up from one pallet and place it on another pallet.
The CRX collaborative robot offers the same high level of performance that all FANUC products are known for including the latest technologies and world-renowned reliability. It supports several of FANUC’s advanced features including iRVision, and is a perfect fit for any application where collaborative robots can help customers achieve higher efficiencies. Also, interactive programming enables users to teach points using hand guidance or a new tablet interface with drag and drop icons. Click here to watch the FANUC CRX in a wide range of applications.
High-Speed SCARA Robots
Pack Expo attendees will have the opportunity to see two SCARA demos. First, the new FANUC SR-20iA will pick and transfer milk crates between two trays. The demonstration shows the SR-20iA’s ability to handle heavy parts in a wide operating area at high speeds.
In a second SCARA demonstration, a FANUC SR-12iA robot with the Environmental Option will pack and unpack bottles of mouthwash. This option includes white epoxy coating, bellow covers, anti-rust bolts and seals, and an IP65 rating to withstand dust and liquids.
FANUC’s family of 4-axis SCARA robots has grown to include the SR-3iA, SR-6iA, SR-12iA, and new SR-20iA models with 3kg, 6kg, 12kg and 20kg payload capacities, and a 400mm – 1100mm reach, respectively. FANUC’s SCARA robots are designed to help customers increase productivity in a number of industries including consumer goods, auto components, plastics, food and beverage, lab automation, appliances and medical device manufacturing.
The small SR-3iA and SR-6iA SCARAs have a compact footprint and space-saving design for maximum efficiency. In addition, the SR-3iA/H and SR-6iA/H are 3-axis variants that provide strong performance and an affordable alternative to small linear slide products. The higher-payload SR-12iA and SR-20iA robots provide flexibility with a large vertical stroke, and an Environmental Option for harsh conditions. All of FANUC’s SCARA robots include exceptional robot motion, speed and precision.
Powered by the R-30iB Compact Plus controller, FANUC’s SCARA robots have the same intelligence and reliability that’s available on all FANUC robots, including integrated iRVision, conveyor tracking (iRPickTool), and most other software options. FANUC’s latest SCARA iRProgrammer user interface makes it easy to setup and program the robot on a Tablet or PC (Teach Pendant is optional).
DR-3iB/8L Food Grade Delta Robot
FANUC’s DR-3iB/8L food-grade delta robot uses 3DV iRVision and iRPickTool line tracking software to pick randomly oriented pieces of chicken from a continuous infeed conveyor. Equipped with a Soft Robotics gripper, the robot picks chicken breasts and reorients them onto an outfeed conveyor. The cell features high-speed picking with product re-orientation. The DR-3iB sets a new standard for robotic food handling in terms of payload, speed, reach and sanitation.
The DR-3iB delta robot is FANUC’s latest solution for picking and packing primary and secondary food products. Rated IP69K, the robot meets the strictest food handling regulations. Its design features corrosion-resistant materials, an unpainted finish, and a fully enclosed body allowing it to tolerate high pressure/temperature and sanitizer wash down environments.
A powerful four-axis design and higher wrist inertia allows the DR-3iB/8L to handle 8kg payloads at very high speeds. Improved repeatability maximizes accuracy, and a hollow wrist design keeps all gripper wires and piping tucked inside. In addition, a large work envelope featuring a 1600mm reach (500mm height) is ideal for applications that require more range such as reaching into tall boxes or handling product on wide conveyors.
The DR-3iB operates with FANUC’s latest R-30iB Plus controller with integrated intelligent functions such as iRVision, Force Sensing, Robot Link, Collision Guard and Zero Down Time (ZDT).
High-Speed Tote Picking with iRVision 3DV/400
At the show, an M-10iD/12 robot will create random orders by picking from four homogenous totes, each with a 3DV/400 vision sensor mounted overhead. Each of the four sensors provide “best pick” locations from the homogenous totes, and then the robot picks parts to fill a customer order. Once the order is complete, the order tote will move to an LR Mate 200iD robot station also equipped with a fixed 3DV/400 to remove the parts from the bin for further order processing. The demonstration highlights how the use of fully integrated robotic 3D Vision is an ideal solution for applications in the warehousing, logistics and e-commerce markets.
The 3DV/400 Vision Sensor is lightweight and can be used as a fixed or robot mounted 3D Vision camera. The 3DV/400 offers single snap 3D image acquisition enabling faster bin picking and the ability to perform applications such as line tracking. Compared to conventional 3D vision sensors it provides better acquisition of shiny parts, and offers a solution for glare caused by reflective parts. The 3DV/400 is part of FANUC’s iRVision suite of fully integrated and complete machine vision products for robot guidance and inspection. FANUC designs all of the hardware and software specifically for FANUC robots, providing our customers with solutions that meet their production needs.
The M-10iD robot series includes four compact material handling robots – the M-10iD/12, M-10iD/10L, M-10iD/8L and M-10iD/16S. Rated best-in-class for speed and repeatability, the M-10iD robots offer a sleek and lightweight design, and feature internal cable routing and a curved J2 robot arm, minimizing interference with work pieces and fixtures. The robots’ payload capabilities range from 8-16kg, allowing them to handle a variety of products. In addition, a long reach (1103mm to 2032mm) and stroke – even in the backflip region – makes it easier for customers to apply the robots while maximizing their available workspace – including larger parts or tooling.
The popular LR Mate 200iD series of tabletop industrial robots offer a “best in class” work envelope for both upright and invert mount installations. Ten models include clean room and wash proof versions, each with various wrist speeds and reaches to accommodate even the most limited workspace. Since the LR Mate series was launched nearly 30 years ago, it has become one of FANUC’s biggest sellers, with over 70,000 units installed across the globe.
FANUC M-410iC/110 Palletizing/Depalletizing with HMI
At the show, the M-410iC/110 robot picks cases from two conveyors and palletizes mixed layer unit loads. Attendees can select from a preset number of unit loads using an Allen-Bradley HMI screen. Once selected, the HMI displays the unit load and the robot palletizes up to three layers. The demonstration shows how easy it is to change layers on the fly. Finally, the robot depalletizes the cases, and the cycle repeats.
The system highlights FANUC’s latest PLC Motion Interface option designed to enable palletizing operators to program homogeneous or mixed unit loads using FANUC Add-On Instructions (AOIs). This helps simplify the deployment of FANUC robots into facilities with operators that have no robot programming experience, but are familiar with Rockwell PLCs.
The M-410iC/110 robot is designed for high-volume case, bag and bottle palletizing operations. It features a 110 kg payload, four-axis articulation, a compact footprint, and a slim arm with through-arm cable routing to simplify dress-out and minimize interference with tooling and other peripheral devices. The ability to perform 2200 standard palletizing cycles an hour with a 60 kg payload makes the M-410iC/110 the fastest palletizing robot in its class. It also features a compact footprint and a 646 mm interference radius, ideal for tight workspaces.