Yokogawa Enhances Plant Safety with IEC 61511-Compliant Exaquantum Safety Function Monitoring
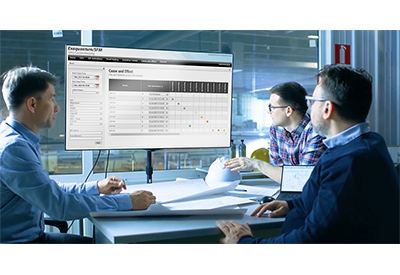
September 21, 2021
Yokogawa Electric Corporation announces a major upgrade to its Exaquantum Safety Function Monitoring (SFM) software, an OpreX™ Asset Operations and Optimization solution that helps identify whether actual operating performance meets safety design targets. Improving health and safety is one of Yokogawa’s six sustainability focus areas. SFM R3.35 provides continuous monitoring and evaluation of safety data to highlight deviations or failures in plant safety system performance.
Already in use across the globe in industries such as oil and gas, SFM collects all safety-related data to track and analyze key performance metrics, including safety instrumented function (SIF) activations and maintenance (proof testing), independent protection layers (IPLs), and initiating causes and overrides. This new version now supports the International Electrotechnical Commission (IEC) 61511* standard and includes several new features to help SFM users identify potential safety issues, optimize maintenance activities, and improve overall safety solution design.
SFM R3.35 enables users to monitor the effectiveness of the performance of defined safety instrumented systems against their design targets.
Development Background
Safety systems are designed to ensure that process plants are operated within tolerable limits, reducing risks to humans, the environment, assets, and production continuity. To sustain the required safety integrity level, processing facilities must have a means for verifying the performance of their safety instrumented systems (SIS) during operations. Procedures need to be established and information must be collected that will ensure the quality and consistency of proof testing, demand rates, and failure data of SIS. The challenge is determining if the real-time operating data can be verified against the analysis, design, and assumptions to highlight deviations or failures in safety system design performance.
Yokogawa recognizes the continuous challenges that plant owners face in trying to efficiently maintain process safety integrity over the entire life cycle of their plant facilities. As one component of a sustainable SIS solution, SFM automatically monitors operational safety data to quickly determine whether real-time operating data meets safety design targets and to track and analyze key safety performance metrics. Proof tests are recorded to track when they took place and identify when they reach their expiration date. SFM assists plant managers by identifying any potential safety issues, reducing unnecessary maintenance activities, and improving the overall safety solution design.
Features
- IEC 61511 compliant
SFM R3.35 employs a cause & effect matrix to quickly verify the logic of SIF activations and final element (valves, vents, actuators, etc.) actuations to see if they match their configured or intended safety design, as required by the IEC 61511 standard. - Enhanced proof testing
A proof testing status function has been added to SFM R3.35 for the monitoring of the expiration dates of proof tests on SIFs and final elements. Users can also claim proof test credit based on actual demand on the SIS during operation, with the functionality to record when proof tests have taken place and their expiry date to help maintain the validity of the safety system. - PHA-Pro compatibility
Safety configuration data for layers of protection analysis (LOPA) using PHA-Pro® (a third-party software solution from Sphera) can be used to generate an initial SFM configuration file. A PHA-Pro export template exports information from the LOPA in a format that can be imported into SFM.
*IEC 61511: A regulatory standard for functional safety in the process industry. It covers the design and management requirements for SISs throughout the entire safety life cycle.
Major Target Markets
Oil and gas production, oil and gas midstream, refining, petrochemicals, chemicals, and power generation.
Applications
Plant-wide monitoring, analysis and reporting of functional safety performance across SIS and final elements.