Electromate: Hazardous Environments & Sensor Technologies Explained
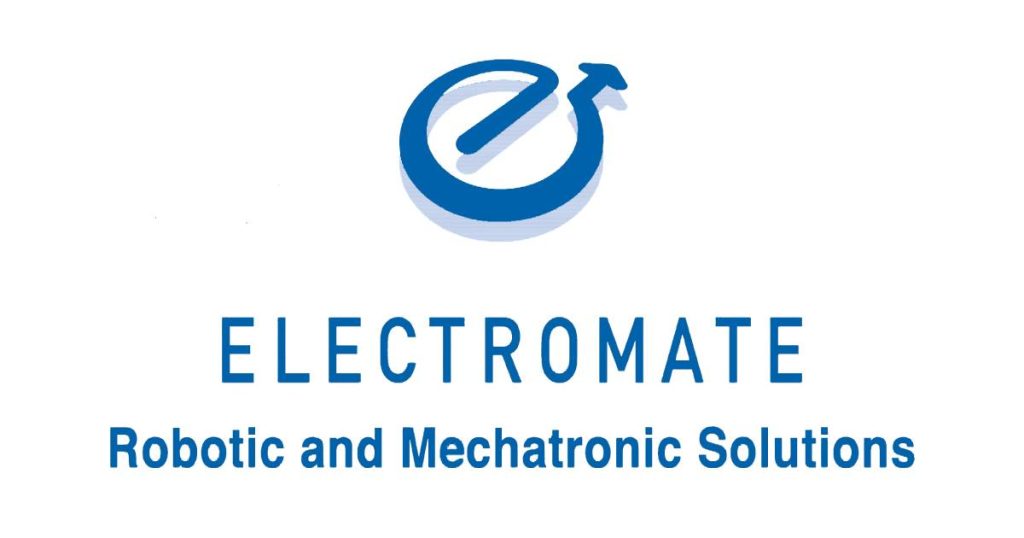
March 6, 2025
Electromate Provides Informative Explanation of Hazardous Environments & Sensor Technologies
Hazardous environments present significant risks due to the presence of flammable gases, vapors, or combustible dust. These areas require strict safety measures to prevent ignition and ensure worker safety. The classification of hazardous locations helps determine the appropriate safety protocols and equipment necessary for each setting.
A hazardous environment exists when a mix of air and flammable substances creates an explosive atmosphere. The presence of potential ignition sources, such as electrical equipment, increases the risk of combustion. Industries such as oil and gas, mining, and manufacturing must implement specialized safety solutions to mitigate these dangers.
Hazardous Location Classifications
To ensure safety, hazardous environments are categorized based on the frequency and presence of explosive substances. These classifications help define the necessary protective measures and suitable equipment.
In North America, hazardous locations are classified under UL and CSA regulations:
- Class I: Flammable gases or vapors, such as those found in oil refineries and chemical plants.
- Class II: Combustible dust, commonly present in grain silos and coal processing plants.
- Class III: Ignitable fibers, a risk in textile and paper mills.
- Division 1: Hazardous materials are present under normal operating conditions.
- Division 2: Hazardous materials are present only under abnormal conditions.
In Europe and Internationally, the ATEX and IECEx classifications define hazardous locations:
- Zone 0: A continuous presence of hazardous substances.
- Zone 1: An occasional presence of hazardous substances during normal operation.
- Zone 2: Hazardous substances are rarely present and only under abnormal conditions.
Understanding these classifications is essential for selecting the right equipment and safety strategies in hazardous environments.
Sensor Technologies for Hazardous Environments
Specialized sensors play a critical role in monitoring and ensuring safety in hazardous locations. These sensors are designed to prevent ignition while providing accurate and reliable data for industrial operations.
- Intrinsically Safe Sensors limit electrical energy output to prevent ignition, making them ideal for environments with continuous hazardous exposure.
- Explosion-Proof Encoders are built to contain internal explosions, preventing ignition from spreading to the external environment.
- Fiber Optic Rotary Encoders offer a non-electrical solution for hazardous environments, eliminating ignition risks associated with electrical components.
- ATEX and IECEx Certified Sensors meet stringent global safety standards for use in hazardous locations.
Industry Applications
Hazardous-rated sensors are used across industries to enhance safety and operational efficiency.
- Oil & Gas – Explosion-proof encoders are used in pump and compressor systems, while intrinsically safe sensors help prevent ignition in volatile gas environments. Pipeline monitoring systems ensure the safe transport of flammable materials.
- Mining – Conveyor belt positioning sensors help maintain safe operations, while gas detection sensors monitor hazardous conditions in tunnels. Automated mining equipment relies on rugged sensor solutions to operate safely in extreme environments.
- Manufacturing & Processing – Printing and textile operations require dust and vapor management solutions to prevent combustion hazards. Pharmaceutical production facilities also rely on hazardous-rated sensors to ensure compliance with strict safety regulations.
Ensuring Compliance & Safety
Regulatory compliance is essential for protecting workers and maintaining safe industrial operations. Hazardous locations require specialized equipment designed to meet ATEX, IECEx, UL, and CSA standards.
Key considerations for ensuring safety in hazardous environments include:
- Environmental Durability: Sensors must withstand extreme temperatures, humidity, and mechanical shock.
- Regulatory Compliance: Selecting devices that meet global safety standards.
- Reliability and Accuracy: High-precision sensors reduce false alarms and improve operational stability.
- Long-Term Durability: Investing in rugged, low-maintenance sensors enhances safety and efficiency.
Overcoming Challenges in Sourcing Components
Securing certified sensors for hazardous environments presents several challenges:
- Navigating Complex Regulations: Compliance with ATEX, IECEx, UL, and CSA standards can be difficult.
- Limited Availability of Certified Components: Finding specialized sensors that meet industry regulations.
- Cost Considerations: Balancing investment in certified equipment with long-term operational benefits.
- Supply Chain Disruptions: Ensuring timely access to compliant components.
Planning ahead and working with trusted suppliers helps mitigate these challenges while ensuring uninterrupted operations.
Hazardous environments require a deep understanding of risk factors, classification systems, and regulatory standards. Implementing the right sensor technology enhances safety, ensures compliance, and improves operational efficiency. By selecting certified sensors tailored to industry needs, businesses can minimize risks and maintain secure industrial processes.