The Power of Brewing: Barnstormer Brewing & Distilling Co
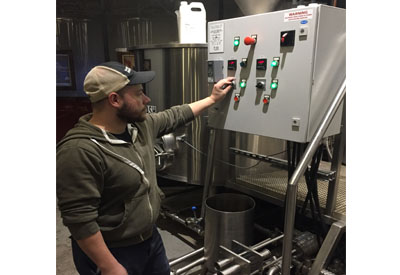
Applications for electrical control panels and automation have reached nearly every sector imaginable, including the brewing industry. In Canada, micro breweries are on the rise, and one of leaders of that charge is Barnstormer Brewing and Distilling Co located in Barrie, Ontario. Owned and Operated by Dustin Norland, since 2012 Barnstormer has advanced the abilities of their brewery with the installation of electrical controls for monitoring brewing temperatures, emergency electrical shut-off switches to protect staff and equipment, and implemented a fully automated filling and seaming system.
Barnstormer has been so successful that they are expanding with a new location to be built in downtown Midland, ON. Conveniently only a few blocks from our publication’s head office, the new facility is going to be bigger and better, with advanced electrical controls and automation. Dustin has agreed to allow us to tour the new facility during the installation phase of the electronic controls that will be implemented at Barnstormer’s Midland location.
The current location in Barrie not only offers a full line of craft beer made in house but also has a great pub-style restaurant. A unique feature at Barnstormer is there viewing walls that allow patrons to see into the brewery from the bar and restaurant. Barnstormer also offers weekly tours of their brewing facility.
Early this April Brad Ariss, Creative Director and Assistant GM, provided a guided tour of the brewery while it was in full swing so we could see just how the modern electrical systems have helped the brewers to more accurately control the brewing process and speed up their canning abilities. Head Brewer Jeff Woodworth (Seen at the panel in the photo) was on site using an electronic control panel to tightly monitor and adjust temperatures, an essential component to perfect beer. The electronics allow for greater precision and immediate temperature adjustment than previous brewing methods.
Safety in the brewery is always ensured by the team of experienced brewers as well as electrical shut off switches to eliminate any electricity from running to components while they are being cleaned or repaired. Emergency switches are also strategically placed to allow staff the ability to easy cut power to their systems in the event of an emergency.
Highly interesting is also their fully automated filling and seaming system that can fill and seal 24 cans per minute. Although the system is fully automated with a user friendly interface the product still required staff to undertake training to fully operate and take advantage of its features. The implementation of an automated canning system has significantly advanced barnstormer’s distribution of craft beer to local Beer stores and LCBO locations.
As a side note we must applaud Barnstormer’s commitment to ensuring they operate as efficiently and as green as possible. Used grain, which retains its nutrient level even after the brewing process, is placed out back for local farmers to collect free of charge as feed for their livestock.
By: Owen Hurst